成形工場のfactor4を目指して
樹脂成形品の軽量化を実現する3つの成形方法
2023.03.17
成形品の軽量化は、これまでも成形業界にとって重要な課題の一つでした。自動車や航空機、また物の輸送に必要なプラスチック製品(例えば荷物をまとめるコンテナやパレットなど)の軽量化は燃費の向上、CO2排出削減に繋がります。住宅・建築業界においては建材の軽量化が耐震性の向上に、電子機器や医療機器などであれば移動時や使用時の負担の軽減に、普段使用するものであればその持ち運びや使い勝手などにつながります。
また、成形メーカーにとっても、樹脂の使用量そのものの削減と、原料費や生産コストの低減につながります。特に近年の世界的な SDGs の取組みや、燃料の高騰といったエネルギー情勢により、成形品の軽量化は、より一層重要なテーマとなってきています。
このコラムでは弊社の主要なお客様である自動車業界を例にとり、その重要性と、成形品の軽量化を実現する3つの成形方法を、ご紹介いたします。
自動車業界での軽量化の重要性
自動車は車重を軽くすることで燃費が改善するため、従来から金属パーツを樹脂パーツに置き換えるなどの軽量化が進められてきました。近年では、電気自動車への移行が進み、より長い航続距離を実現するために、バッテリーを多数搭載する必要が出てきました。また、自動運転に向けては、カメラやモニター、多数のセンサー類が必要で、これらを繋ぐ配線やコネクター類も合わせ、重量増の要因となっており、更なる車体の軽量化が重要な課題となっています。
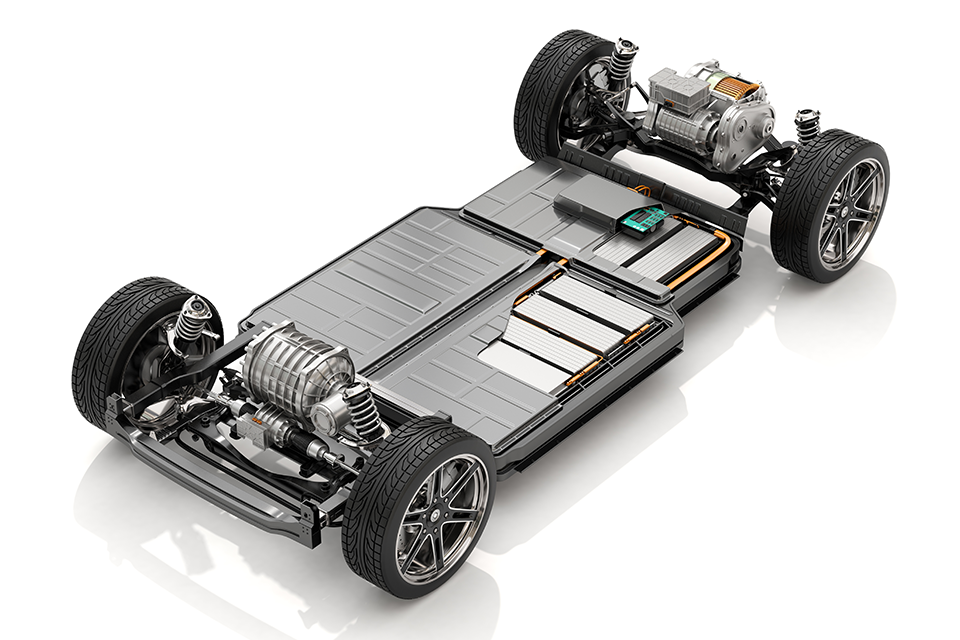
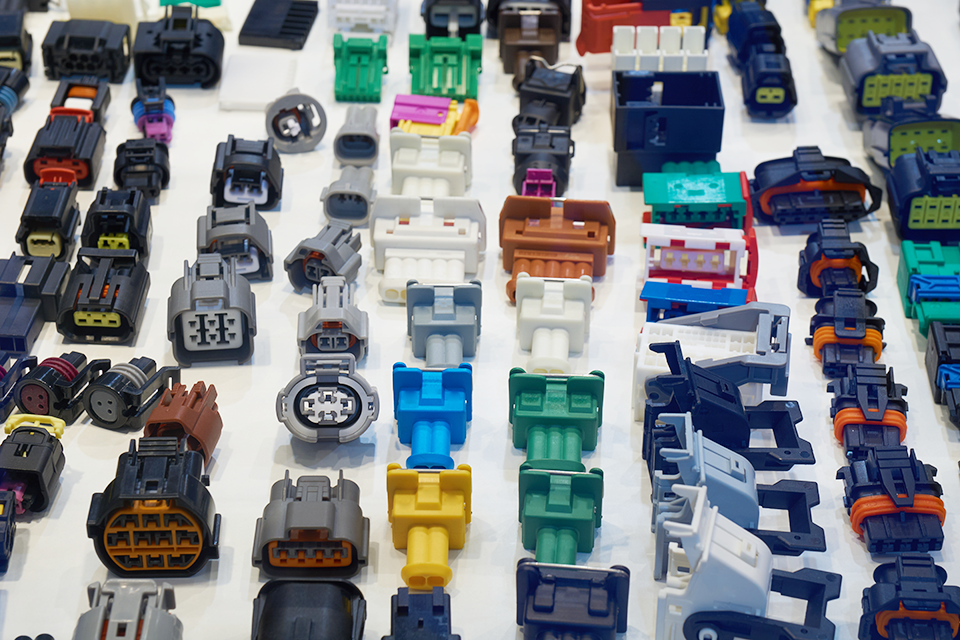
自動車における樹脂成形品は、部分的な外装パネルのほか、エンジン関連パーツ、機構パーツに加え、室内にはドアの内張やダッシュ周り、コンソール、メーターパネル、モニター、スイッチ類と、と非常に多くのパートで使用されています。このことからも、樹脂成形品の軽量化は、車重の軽減に大きく寄与することが想像できます。
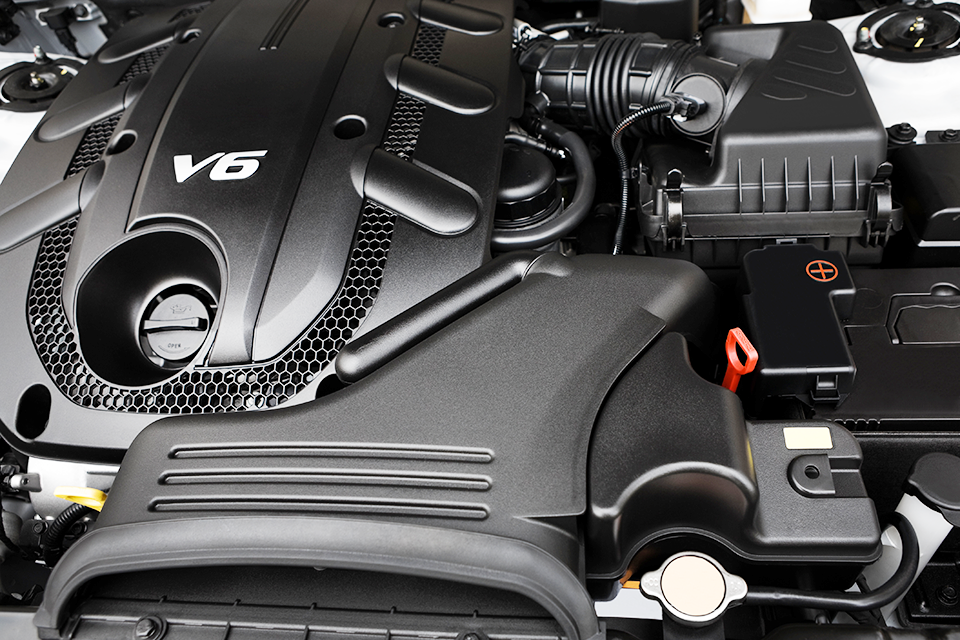
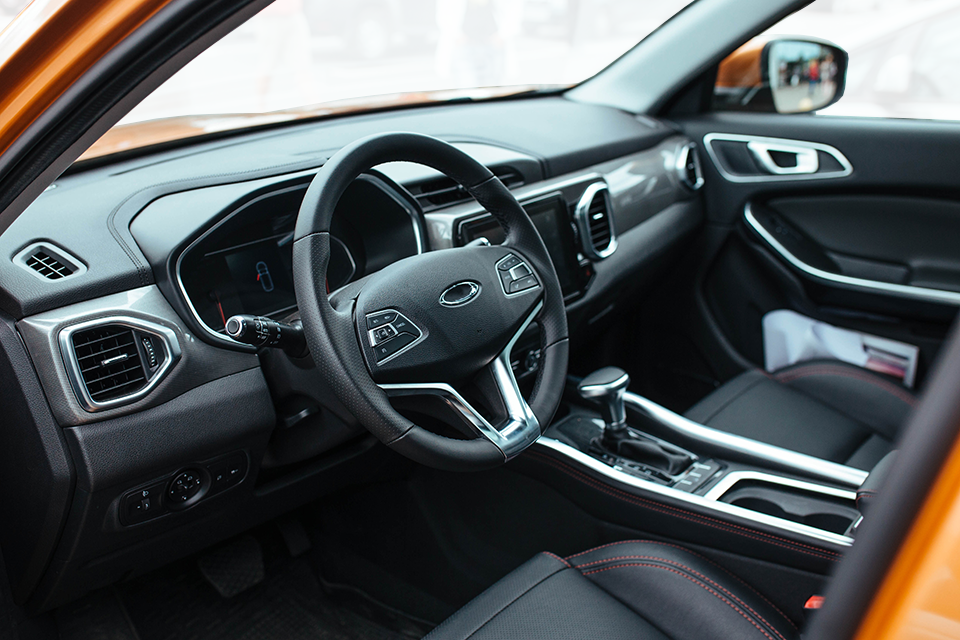
成形品の軽量化における課題
成形品を軽量化する際に課題となるのは、その成形品の強度についてです。成形に使用する樹脂量を減らして肉厚を薄くすれば、強度が落ちる事は必至です。日常使う雑貨類であれば然程問題にはなりませんが、自動車や航空機など、人の移動や輸送に関わる乗り物に使われるパーツ類は、安全上の理由からその強度と剛性を確保する必要があります。
相反するように見えるこの課題を解決するためには、新しい材料や技術、構造設計の見直しが必要となるため、様々なメーカーで日々研究が進められています。
成形品の軽量化を実現する成形方法
成形品の軽量化を実現する成形方法は様々ありますが、その中から自動車や航空機用として用いられている3つの成形方法をご紹介します。
繊維強化プラスチックを用いた成形
一つ目は繊維強化プラスチック(FRP)を用いた成形で、材料の種類としては、炭素繊維強化プラスチック(CFRP)、ガラス繊維強化プラスチック(GFRP)、アラミド繊維強化プラスチック(AFRP)などがあげられます。
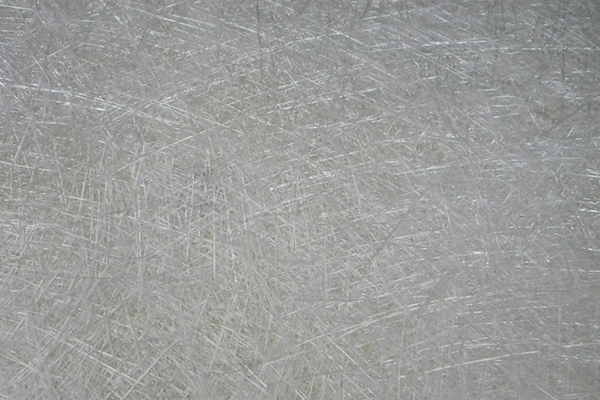
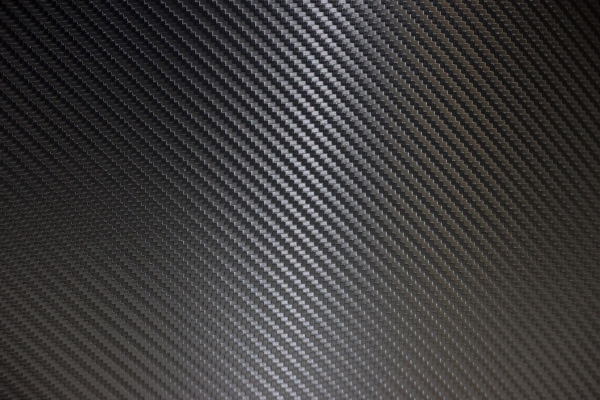
自動車や航空機などに使われる大型部品では、主に圧縮成形(プレス成形)が用いられ、小型・精密部品などは射出成形が用いられています。いずれも樹脂原料に繊維を混ぜて成形する事で通常のプラスチックに比べて高い強度や剛性が得られるため、金属パーツの代替品として使用されたり、それ自体の厚みを抑えられる事から、強度を維持した軽量化が可能となる成形方法です。
発泡成形
発泡成形とは、樹脂内部に気泡構造を作り出し、樹脂の使用量を抑える事により成形品の軽量化を実現する成形方法です。勿論、通常成形で作られたものと同じ形状(構造)のまま発泡成形で成形品を作った場合、樹脂使用量が減った分、強度は落ちてしまいますが、発泡成形の特性を理解し、成形品の構造から見直す事で、同様の外観形状を維持しつつ、強度を落とさずに軽量化することが可能となります。
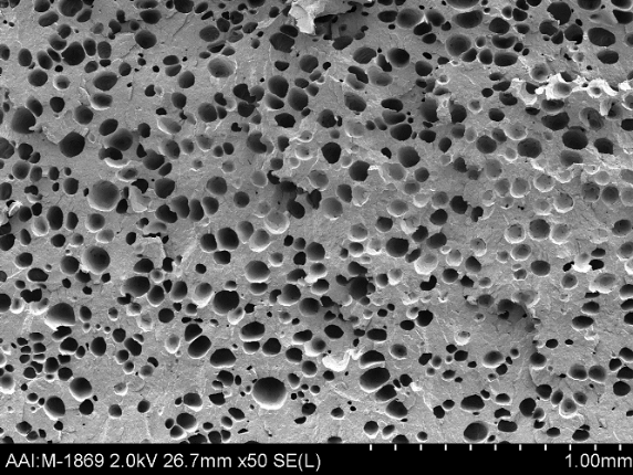
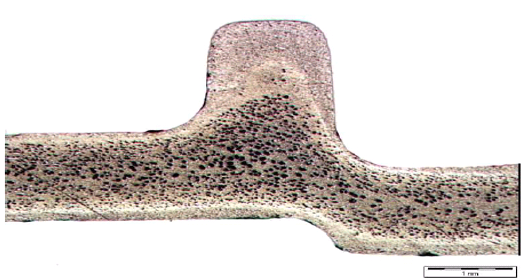
この発泡成形には、大きく2つ、化学発泡と物理発泡があります。
化学発泡
化学発泡とは、樹脂に化学的な発泡剤を混ぜ込むことで発泡させる方法です。こちらは既存の設備を大きく変更する必要がないため、初期導入コストが抑えられるというメリットがあります。しかし、発泡剤の種類によっては、成形後の匂いが問題になる、熱分解によって有害物質を生成する、金型の腐食を招くなどのトラブルや、成形品に化学薬品が含まれてしまうためリサイクルが困難になるなどのデメリットがあります。
物理発泡
もう一方の物理発泡とは、高い圧力の中で溶かした樹脂原料の中に超臨界流体(高圧のガス)を溶融させ、射出時の圧力の低下により気泡を発生させる方法です。こちらは成形機への改造と、超臨界流体の生成、コントロール装置、成形機シリンダーへの注入の仕組みなどが必要となる事から、初期導入コストのかかる点が化学発泡と比較してのデメリットになります。しかし、化学薬品を使用しないため、先に述べたような薬品に起因するトラブルを心配する必要がなく、成形原料自体の物性が変わらないため、リサイクルが容易です。そのため、 SDGs 的な観点から、大手メーカーではこの物理発泡成形を導入している例が多くなっているようです。
マツイは、この物理発泡の MuCell® 微細発泡成形を提供する TREXEL社と提携しております。 MuCell® 微細発泡成形では、窒素または二酸化炭素を超臨界流体状態にして樹脂に溶融させ、金型内に射出した際の圧力の低下によって均一な微細発泡構造を形成します。適切な製品設計と組み合わせることで、強度を落とさずに 5〜40%もの成形品の軽量化を実現しています。
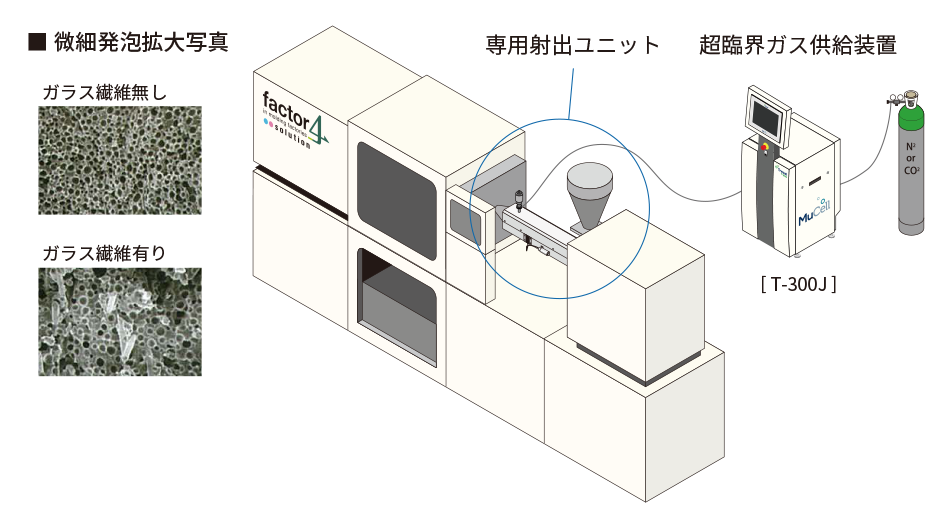
ヒート&クール成形
ヒート&クール成形とは、成形品の開口部の周囲に発生するウェルドラインを解消するために開発された技術で、金型の成形面を樹脂が溶融する温度域まで上げた状態で射出し、その後急冷するという成形方法です。射出時に金型の温度を高く設定することで樹脂の流動性があがるため、ウェルドラインが目立たなくなったり、転写性が向上するなど、成形品の表面品質が良くなるだけでなく、一様に急冷することで成形後の変形が抑えられ、寸法精度の向上にもつながる画期的な成形方法です。
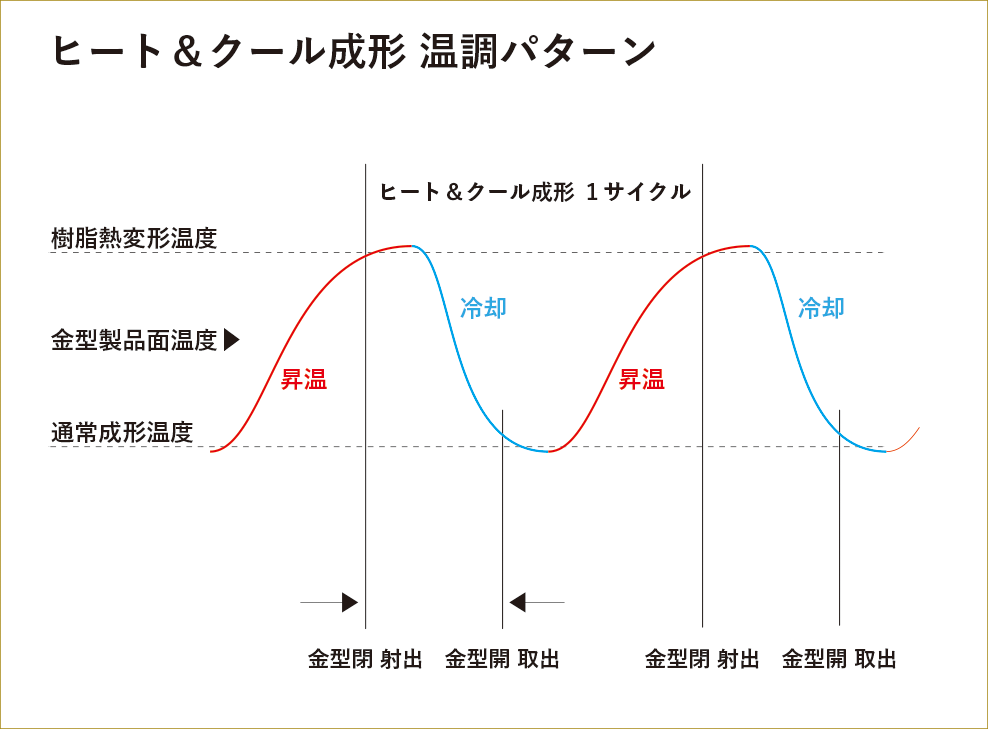
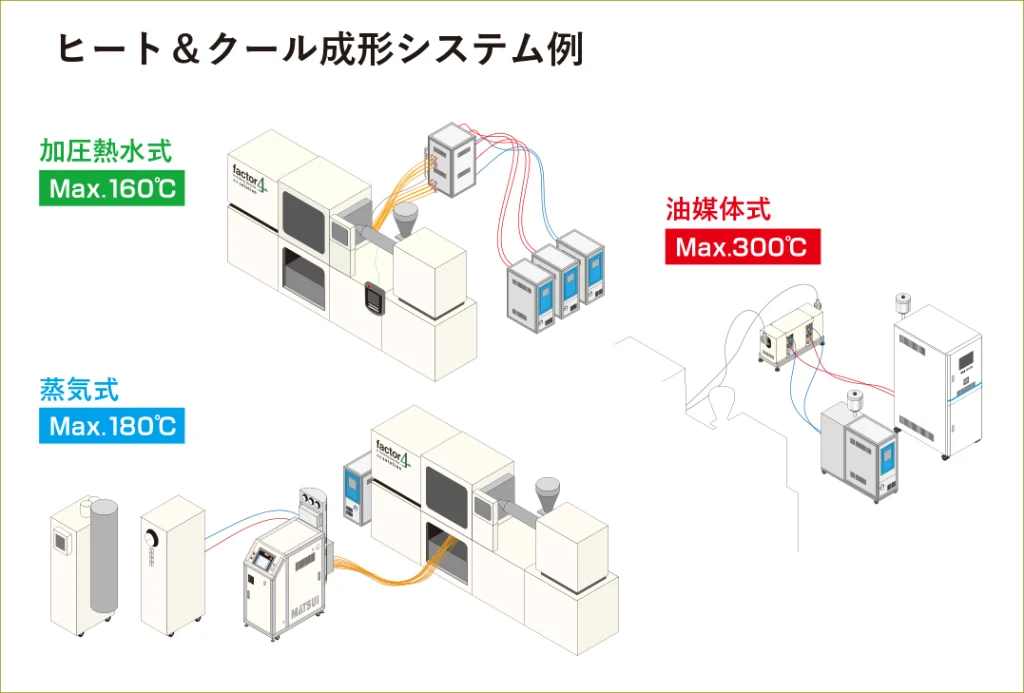
ヒート&クール成形による成形品の軽量化は、樹脂の流動性のが向上するため、必要最低限の厚みに設定できる(余分な材料を使用しない)という点において有効という事で、この成形方法のみでの効果はあまり大きくはありません。実は、先に紹介しました「繊維強化プラスチック成形」や「発泡成形」などの技術と組み合わせることで、相乗効果を最大限に引き出すことができるのです。
通常温度での二つの成形方法では、成形品の表面に、繊維質や湯じわ、フローマーク、スワールマークなどが現れてしまうため、軽量化できても外観品には使えない、とされてきました。しかし、ヒート&クール成形と組み合わせる事で、綺麗な外観が得られるようになり、家電製品や車の内装パーツなど人の目に触れる外観品にも広く採用されるようになりました。
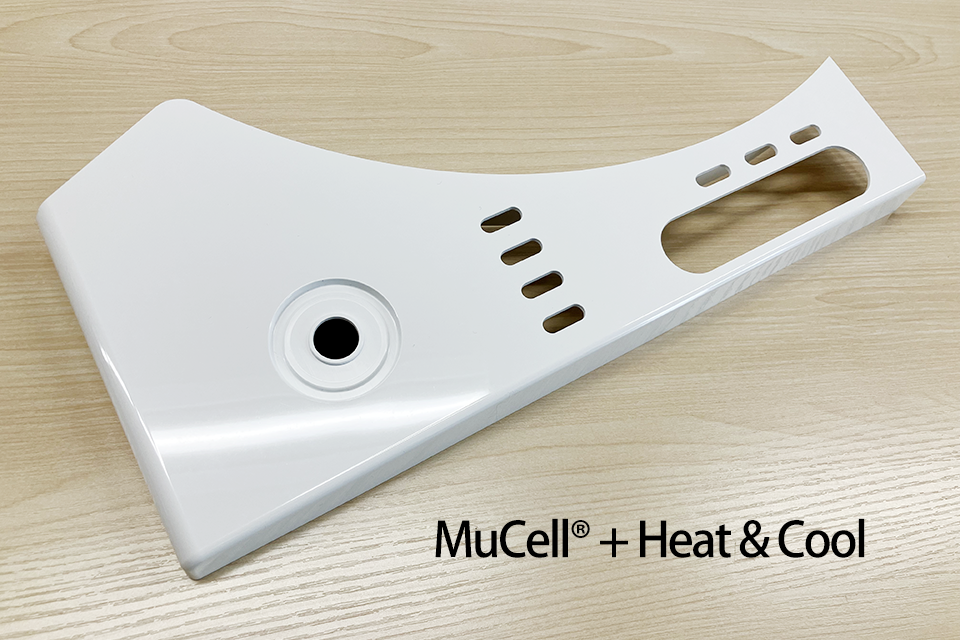
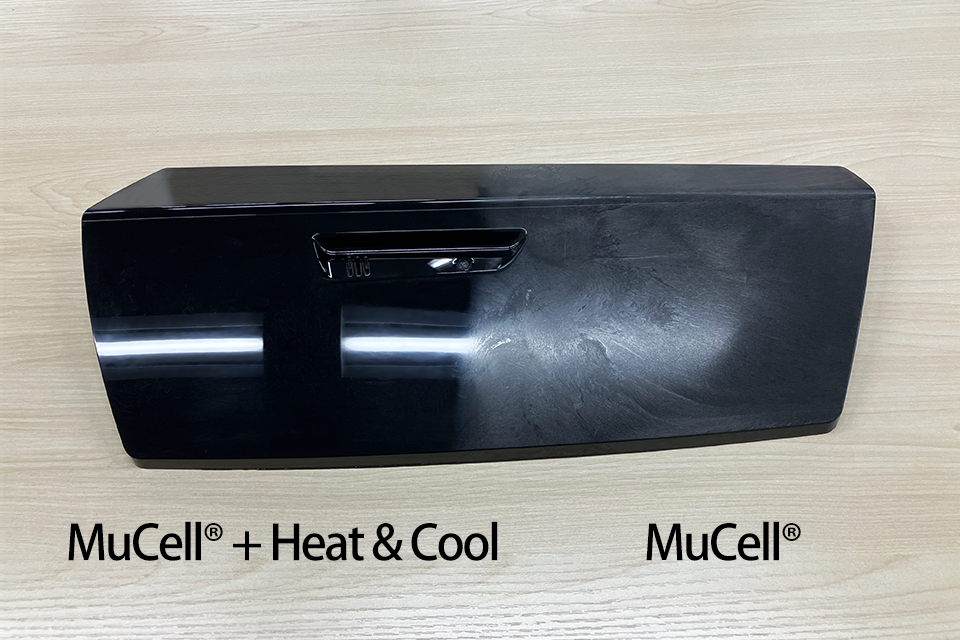
まとめ
成形品の軽量化は、樹脂使用量や、生産コスト及びエネルギー、CO2排出の削減につながるため、今や世界的なトレンドとなっています。自動車や航空機だけでなく様々な分野で、より一層の軽量化が求められていく事でしょう。
今回ご紹介した他にも、成形品を軽量化する技術や成形方法は様々あります。より高い効果を生み出すためには、生産形態や成形品に適した手法や装置の導入が必要となります。
松井製作所では「成形工場の’factor4’を実現する」をミッションとし、成形工場の資源生産性の向上、成形品及び成形工場の付加価値向上を実現するさまざまなソリューションを提案しています。ぜひお気軽にご相談ください。
CX デザイン部 飯島 泰彦