なぜ糸引きやコールドスラグは起こるのか?
エンジニアリングプラスチック(以下、エンプラ)の成形では、糸引きやコールドスラグといった不良が発生しやすく、特に精密成形や光学成形では厄介な問題となります。これらの不良の背景には、エンプラ特有の物性と、ノズル先端・金型スプルブッシュ周辺の熱管理が密接に関係しています。
エンプラにおける3つの課題特性
1.樹脂流動性が低い
エンプラは溶融しても流れにくく、金型内の隅々まで届きにくいため、充填ムラや滞留が起こりやすくなります。
2.樹脂粘性が高い
高粘度な樹脂は、ノズルやスプル内で熱が逃げやすく、流れが急に鈍化、冷却され、スラグの原因となります。
3.溶融温度が高い
成形温度を高く設定する必要があり、そのぶん温度管理がシビアになります。ノズルの冷却で樹脂が早期に固化し、糸引きやスラグの発生につながります。
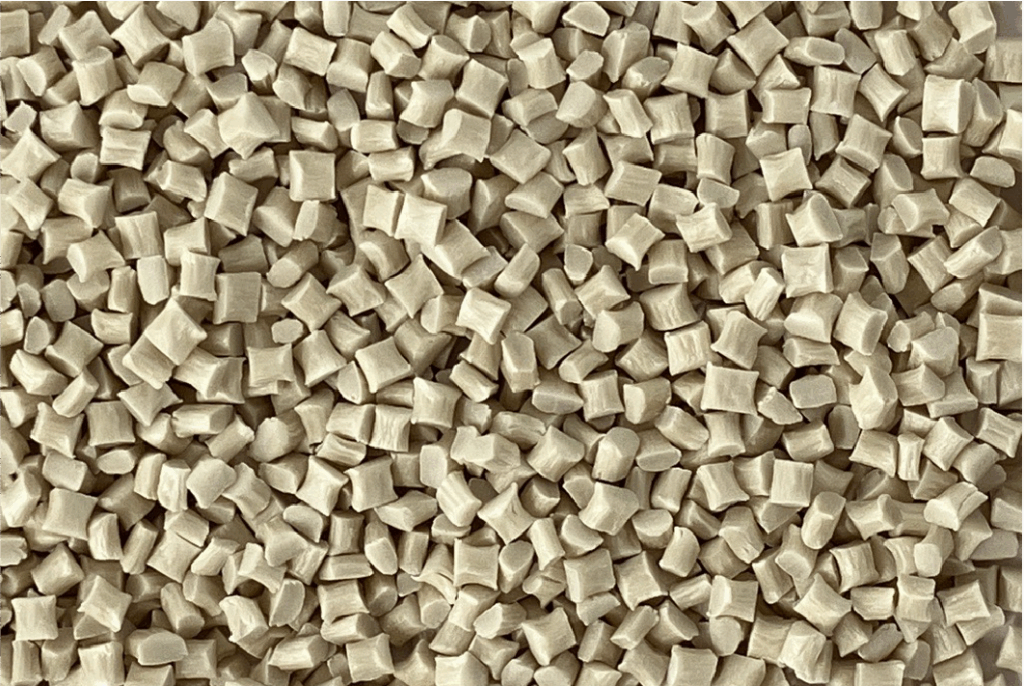
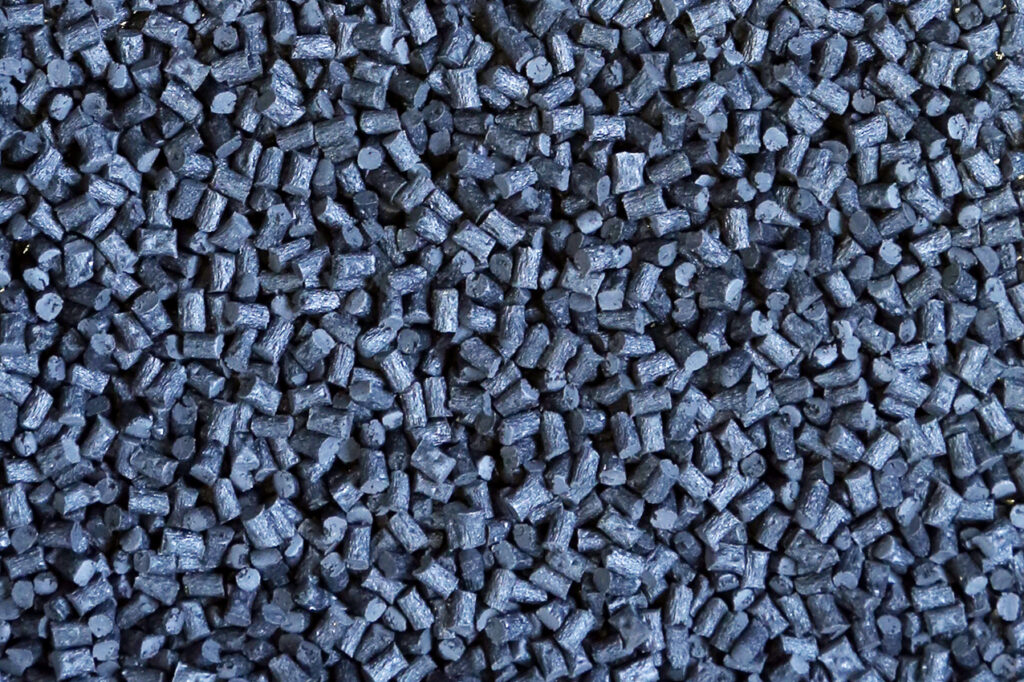
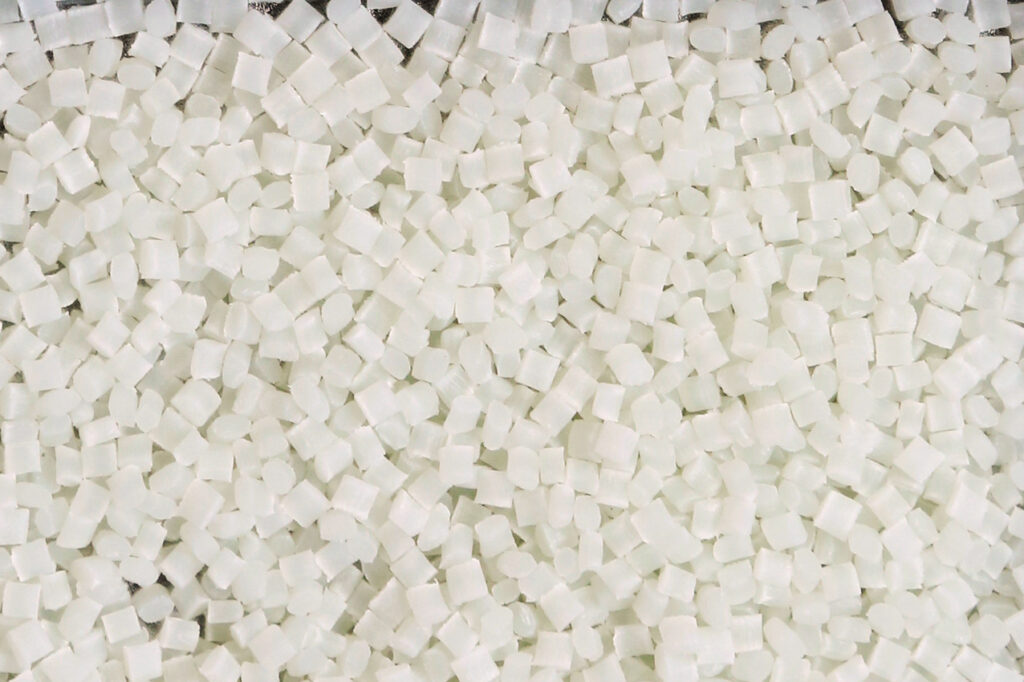
熱移動と成形条件のトレードオフ
射出ノズル先端が金型(スプルブッシュ)に接触することで、ノズル温度が急激に下がり、樹脂がノズル内で固化・詰まりを起こすリスクがあります。これを防ぐため、ノズル温度を高めに設定すると、今度は冷却が間に合わず、樹脂が糸状に引かれてしまう(=糸引き)現象が起こります。
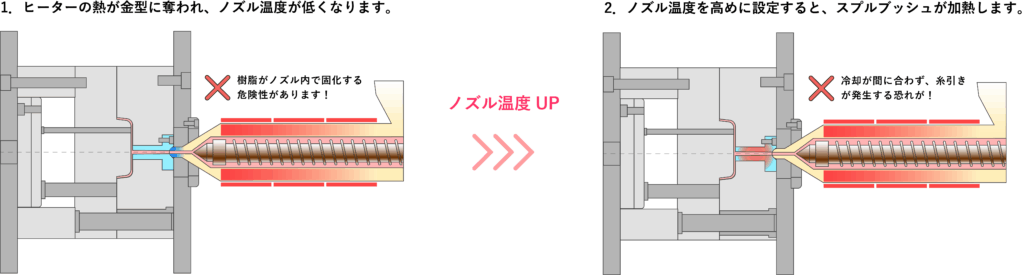
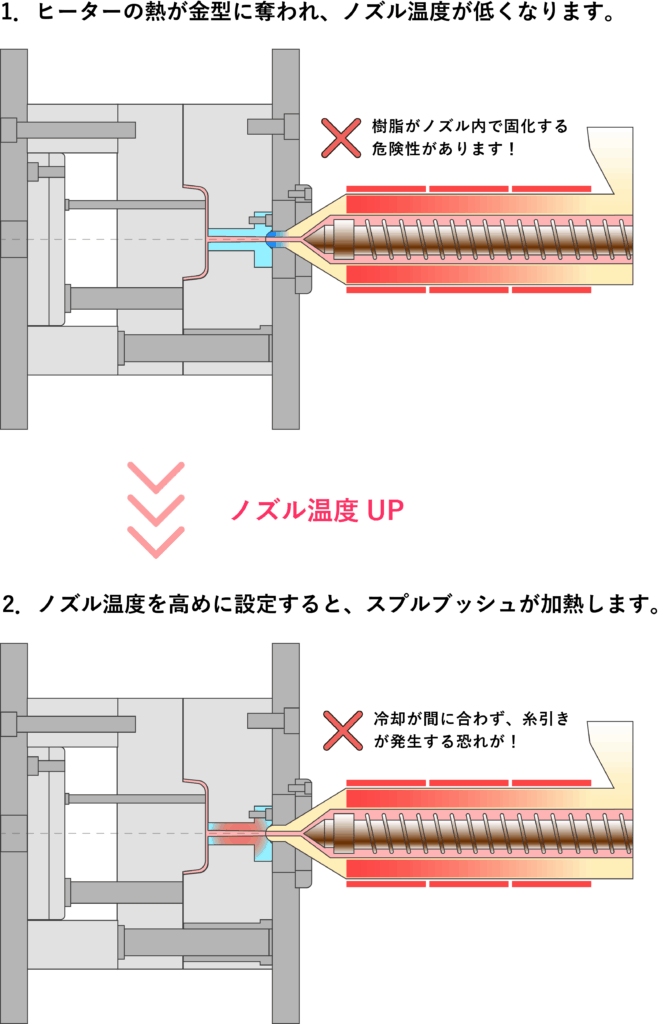
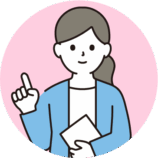
糸は金型内に付着すると、次のショットで成形品に転写されスジ状のへこみとなり、外観不良を引き起こします。特にエンプラでは糸の挟み込みが金型を傷つける恐れもあり、除去作業が必要になることで生産性も低下します。
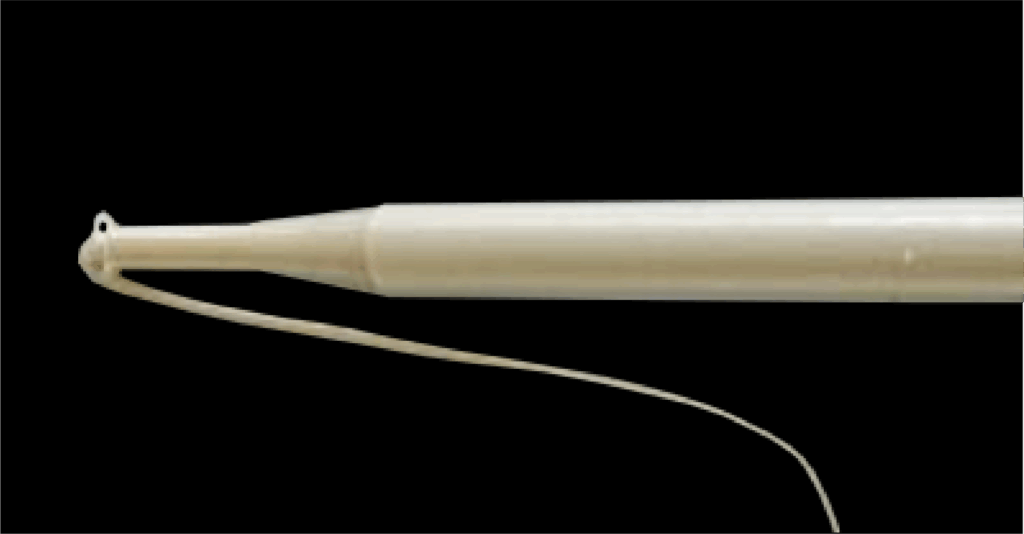
その対策として、計量後にノズルを後退させて糸引きを防ぐ方法もありますが、この場合ノズル内に残った樹脂が空冷され、次のショットで未溶融のままスラグとして混入する(=コールドスラグ)問題が発生します。
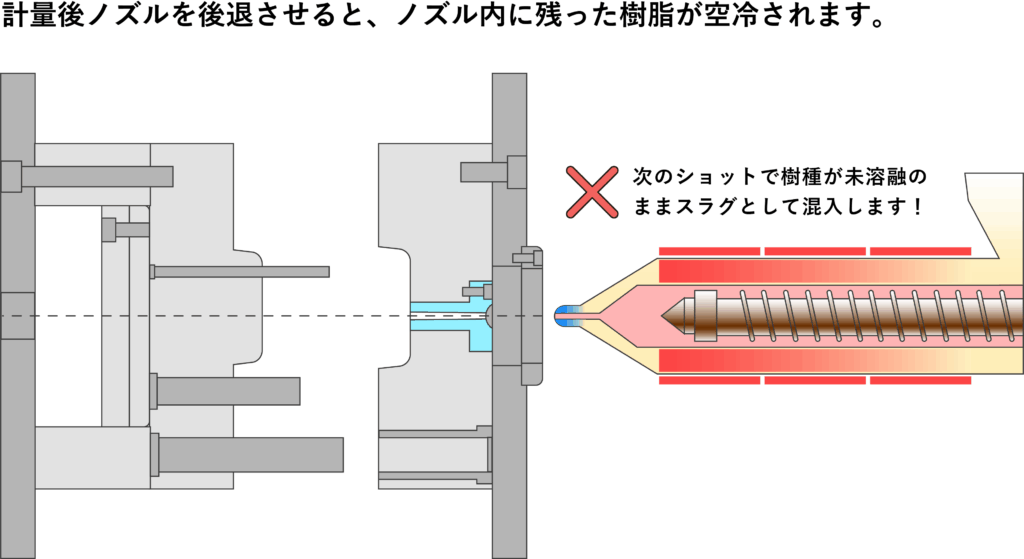
つまり、糸引きとコールドスラグは”温度管理のジレンマ”から生まれる表裏一体の不良といえます。では、どのように対処すべきなのでしょうか?
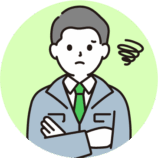
ノズル温度を上げたら糸引きするし、下げたらスラグが出るし…。
正直、どっちを優先すればいいのか分からなくて困ってるよ。
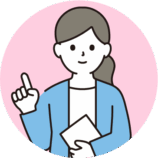
それ、“温度管理のジレンマ”ですね。こうしたエンプラ成形特有の不良は、従来の成形条件の微調整では根本的な解決が難しい場合もあります。
糸引きとスラグ、どちらを優先すべきか?
糸引きとコールドスラグの両方を完全に防ぐには、成形条件の細やかな調整が求められますが、以下の対策にはそれぞれ限界があります。
成形条件の調整による対策方法
対策①:ノズル温度の上昇
ノズル部の温度を高く保つことで、樹脂の固化(スラグ)を防止することが可能です。しかし、その反面、糸引きが発生しやすくなるという課題があります。
対策②:ノズル後退(リトラクト)
充填完了後、ノズルを金型から離すことで、糸引きを防止します。ただし、ノズル内で樹脂が冷えて固まり、コールドスラグの原因となります。
対策③:スクリュー計量/射出タイミングの最適化
ショートショットやノズルシーケンス調整も一定の効果が期待されます。しかし、成形機や金型の制御レベルに依存し、現場での再現性が難しいこともあります。
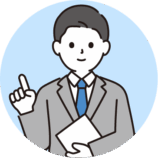
これらの対策はいずれも一長一短。
糸引きを防げばスラグが、スラグを防げば糸引きが…。
この”温度管理のジレンマ“を構造的に断ち切るアプローチが求められます。
ZiRKONが成形現場にもたらす3つのメリット
これらエンプラ成形ではよくあるお悩みも、ZiRKONなら構造的にその問題を解消します。
ZiRKONは、ノズルと金型の接触部分(以下、ノズルタッチ部)を断熱する構造を持つ特殊なスプルブッシュです。この断熱層が、ノズル先端の温度低下を抑制し、安定した成形環境を実現します。
1.ノズル内の過剰な過熱を防ぎ、安定した温度管理を実現
ノズルタッチ部を高い断熱特性を持つジルコニアセラミックで断熱することで、ノズル内部の樹脂が必要以上に加熱されることを防ぎます。この温度管理の最適化により、「糸引き」の発生を大幅に削減し、金型や製品への付着・転写による外観不良を抑制します。特にエンプラのような粘度の高い樹脂を使用する現場においては、糸引きの抑制は製品品質の安定と生産効率の両立に直結します。
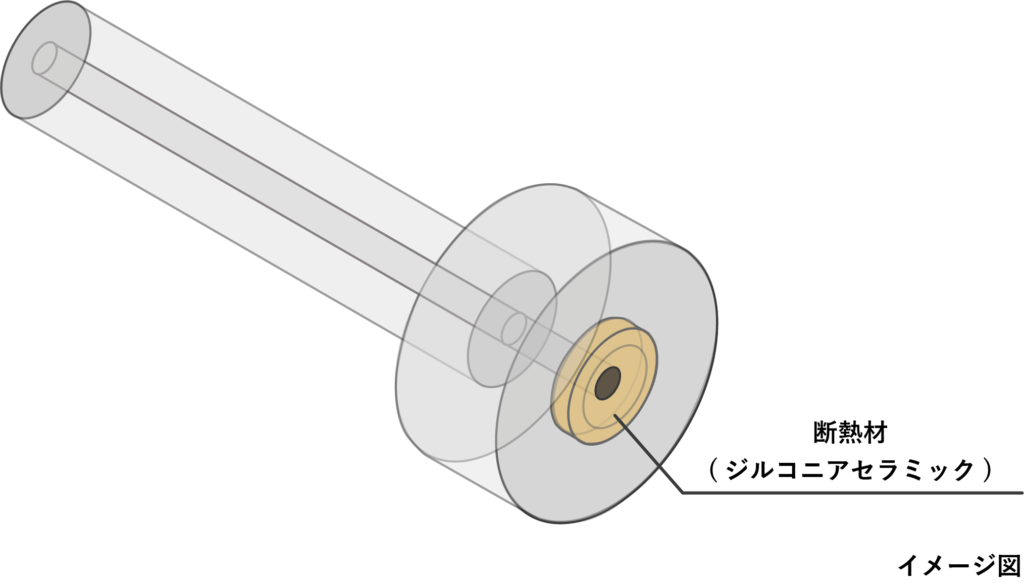
2.ノズル後退不要で、冷えた樹脂の混入リスクを回避
従来の糸引き対策であるノズルを後退させる運用方法では、ノズル先端に残った樹脂が冷却され、次のショットで「コールドスラグ」として成形品内に混入するリスクがあります。
ZiRKONは断熱構造により、ノズル後退を行わずとも糸引きが起こりにくい環境を実現。そのため、ノズル先端の樹脂を冷やすことなく、スラグ発生の原因を根本から断ちます。異物混入やゲート詰まりなどの問題を未然に防ぐことで、金型トラブルやチョコ停といった成形機の突発的な停止時間の削減にもつながります。
3.温度ムラを排除し、スムーズな立ち上げと安定生産をサポート
ZiRKONの断熱効果により、ノズルと金型間の熱バランスが安定することで、成形条件のばらつきが抑えられます。特に立ち上げや材料替えなど、成形条件の微調整が必要な場面では、捨てショットを削減し、樹脂のムダを軽減できます。不良率の低下と稼働率の向上によって、総合的な生産効率アップに貢献します。
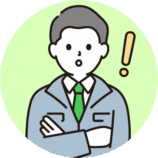
えっ、断熱するだけの単純な構造で、成形の安定化に効果があるんですか?
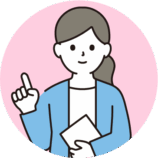
はい、ノズルタッチ部を断熱することで、熱移動による問題を解決できるんです。お客様から「設定をいじらなくても不良が減った」というお声もいただいています。
注意事項
※1 スプルブッシュをノズル側から黄銅棒などで叩くと、セラミックが損傷する可能性がありますので、ご注意ください。また、ノズルの芯ずれはセラミックのエッジの破損原因となります。
※2 ジルコニアは焼結セラミックで、割れることがあるため、非保証とさせていただきます。ご利用開始後の返品はご遠慮くださいますよう、ご理解のほどよろしくお願いいたします。
※3 損傷リスクが増えるため、計量後ノズル後退モードでの使用はお控えください。