
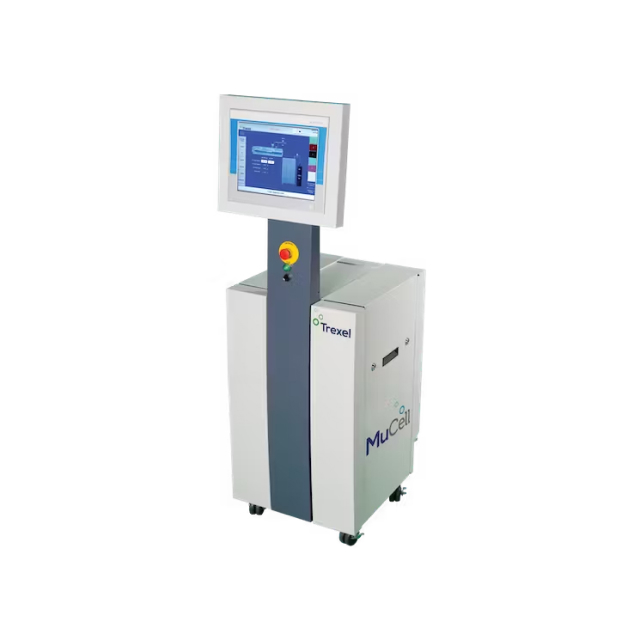
超臨界状態のガスを直接樹脂へ溶け込ませる物理発泡⽅式を採⽤。⾼い発泡性と適応範囲の広い成形法で、軽量かつ⼨法安定性が良好な射出成形品、ブロー成形品の生産を実現します。
MuCell®微細発泡成形とは
MuCell®微細発泡成形について
大気から取り出した窒素や二酸化炭素を直接利用し、樹脂を溶け込ませる物理発泡式の成形方法です。化学発泡よりも発泡力が強く環境にやさしいという特徴をもっています。
成形の流れ(仕組み)
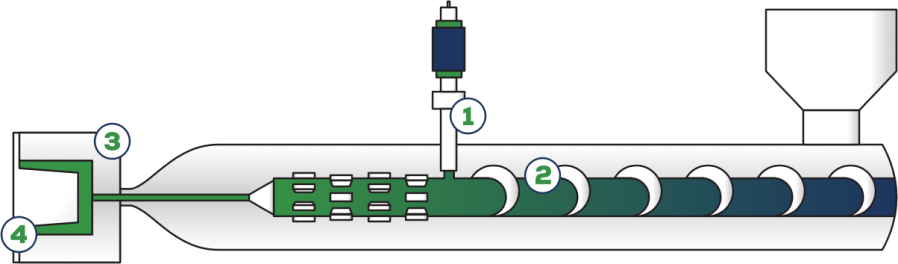
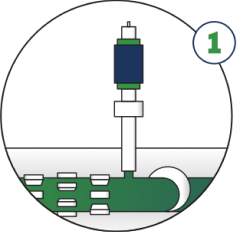
可塑化中に、正確に計量した超臨界状態の窒素や⼆酸化炭素(SCF)を、バレルに取り付けられた専⽤インジェクターを介して樹脂に注⼊する。
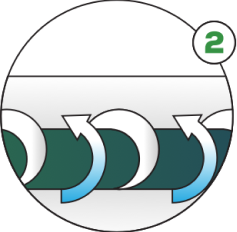
可塑化バレルにある、特別設計の混合部を持つスクリューにより、溶融樹脂にSCFを均一に分散・混合し溶解させた、単一相溶融物が形成される。
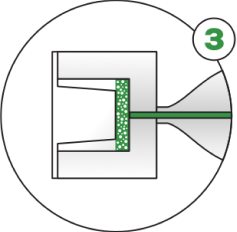
⾦型キャビティ内に溶融樹脂が射出されると、⾦型キャビティ内での圧⼒降下により、発泡セルの核が形成される。分⼦内に分散しているSCFにより、ソリッドスキン層を持つ均質な独⽴発泡構造が形成される。
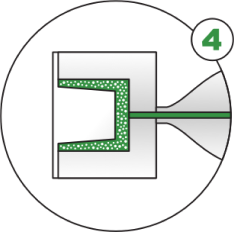
制御された発泡セルの成⻑により、保圧⼯程が代替され、⾦型キャビティ全体に均⼀で低圧な充填圧⼒がかかる。⾦型キャビティが充填されるとセルの成⻑は停⽌する。
MuCell®の特長
樹脂使用量の削減
樹脂が発泡することにより、軽量化、樹脂使⽤量の削減をする事ができます。また、発泡によりヒケを防⽌できる事から、今までにないデザインが可能となり、成形品の体積を減らすことで更なる樹脂使⽤量の削減ができます。
ソリ・ヒケの改善
樹脂の発泡が保圧を代替えするため、ヒケの発⽣を防⽌することができます。ほとんどの場合、基本⾁厚と同じ厚みのリブを設定しても成形品にヒケを発⽣させません。
また、保圧が不要になるため、保圧によるソリが改善できます。
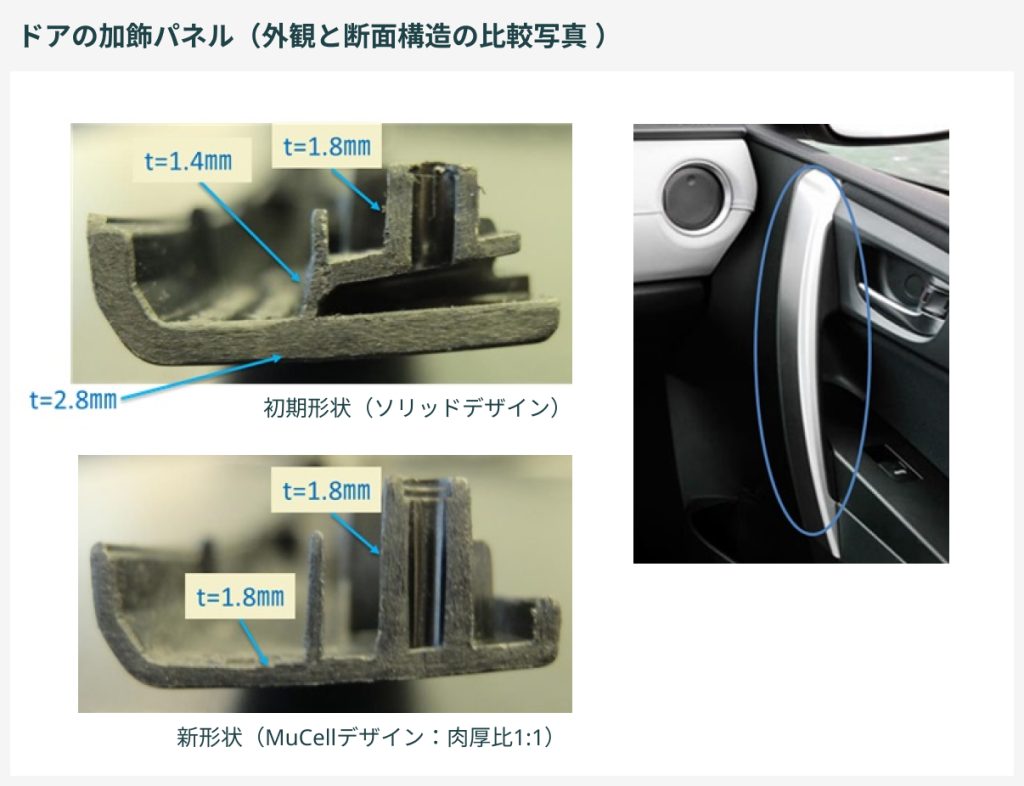
生産性の向上
発泡によりヒケが防⽌できるため保圧を使⽤しない成形⽅法となります。これにより、型締め⼒を約50%(重量軽減率10%時)低減できるため、成形機の型締めトン数を下げることができます。
また、同じ成形機であれば、2倍の取り数を実現できます。その他、保圧⼯程の削減時間分サイクルタイムを短縮する事ができます。
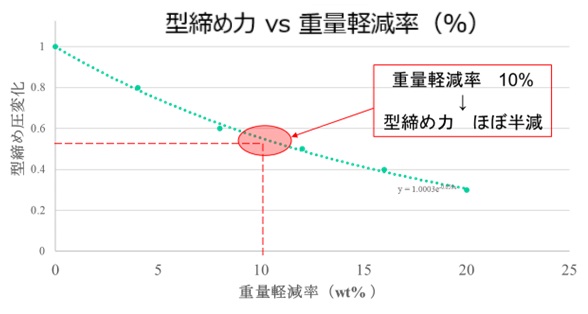
成形事例
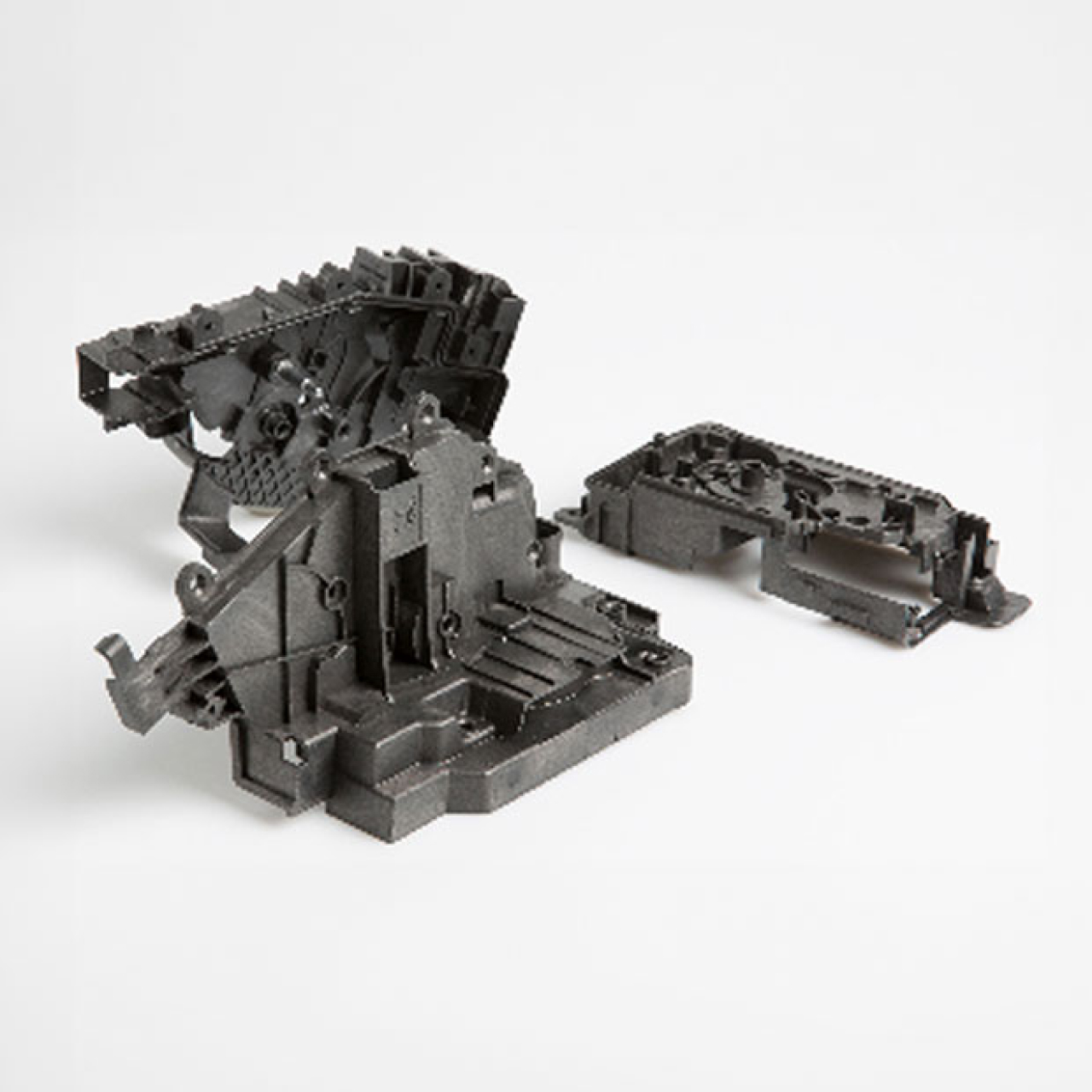
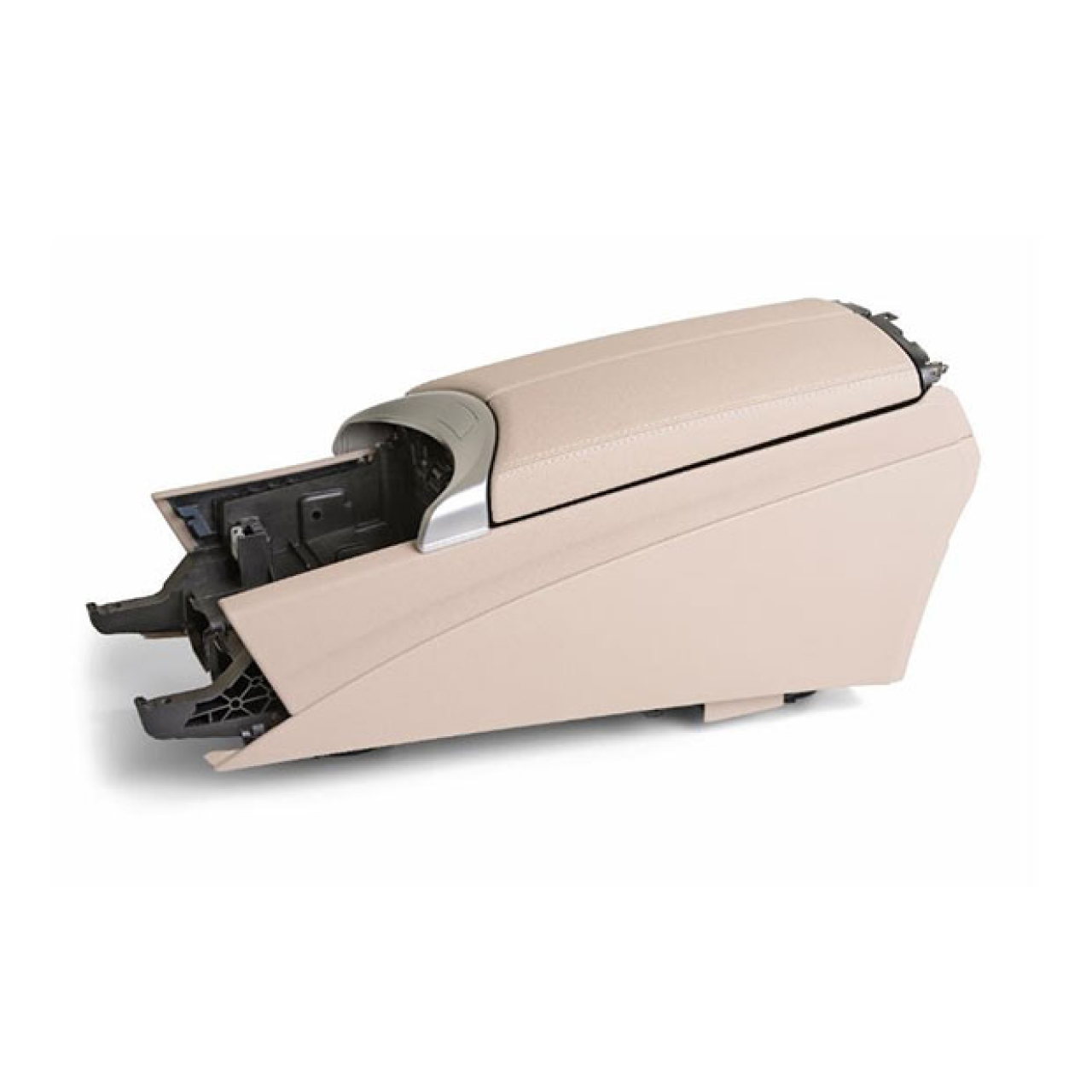
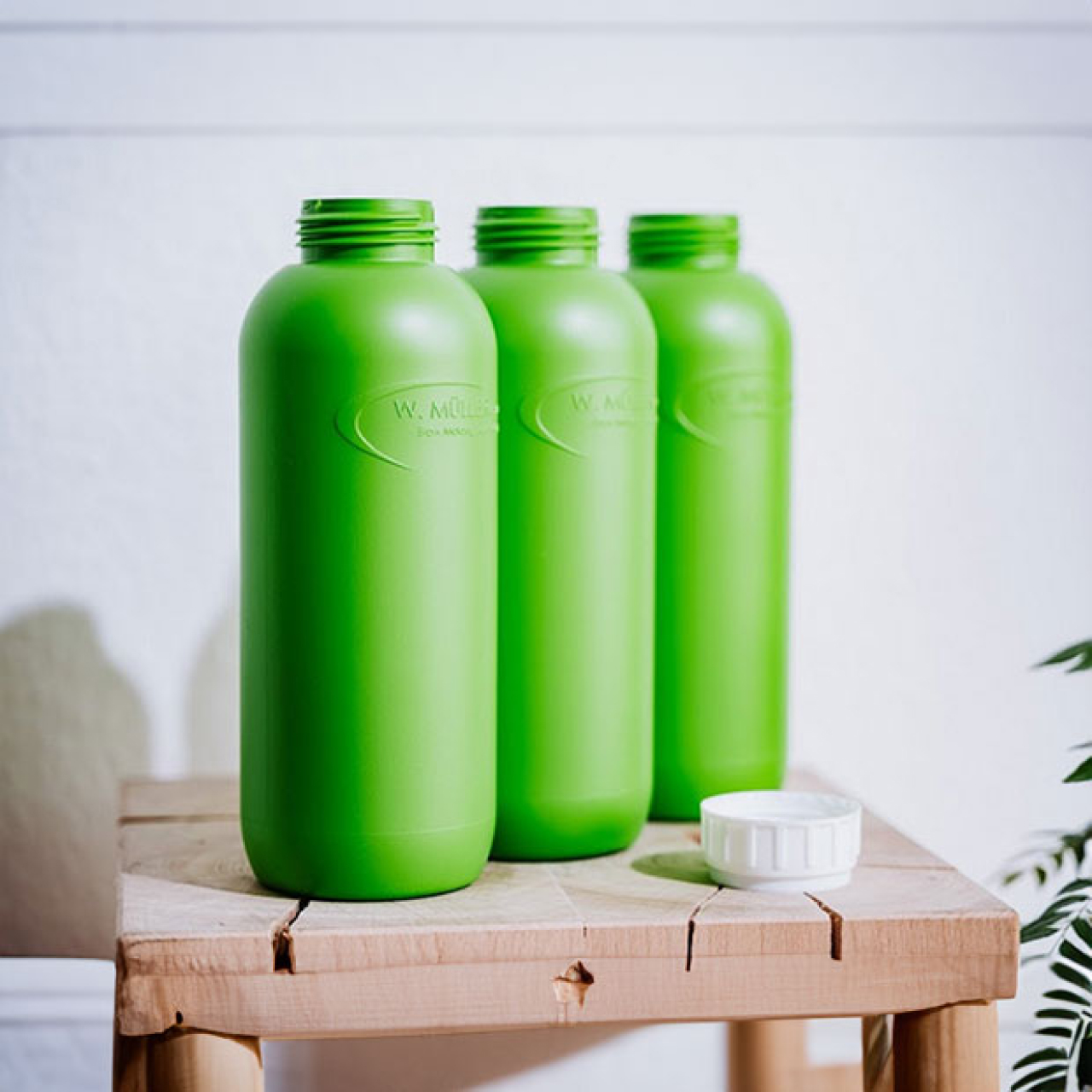
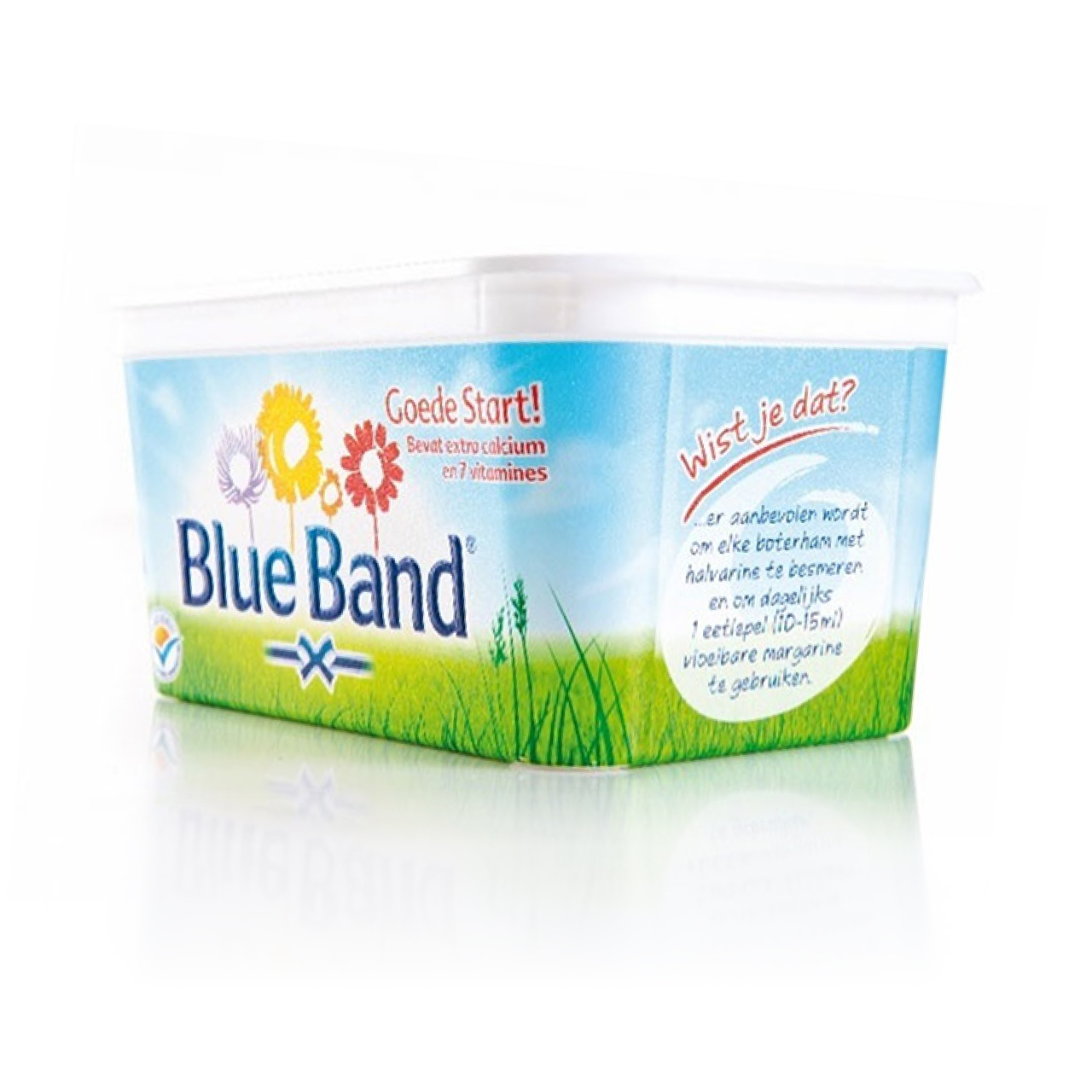
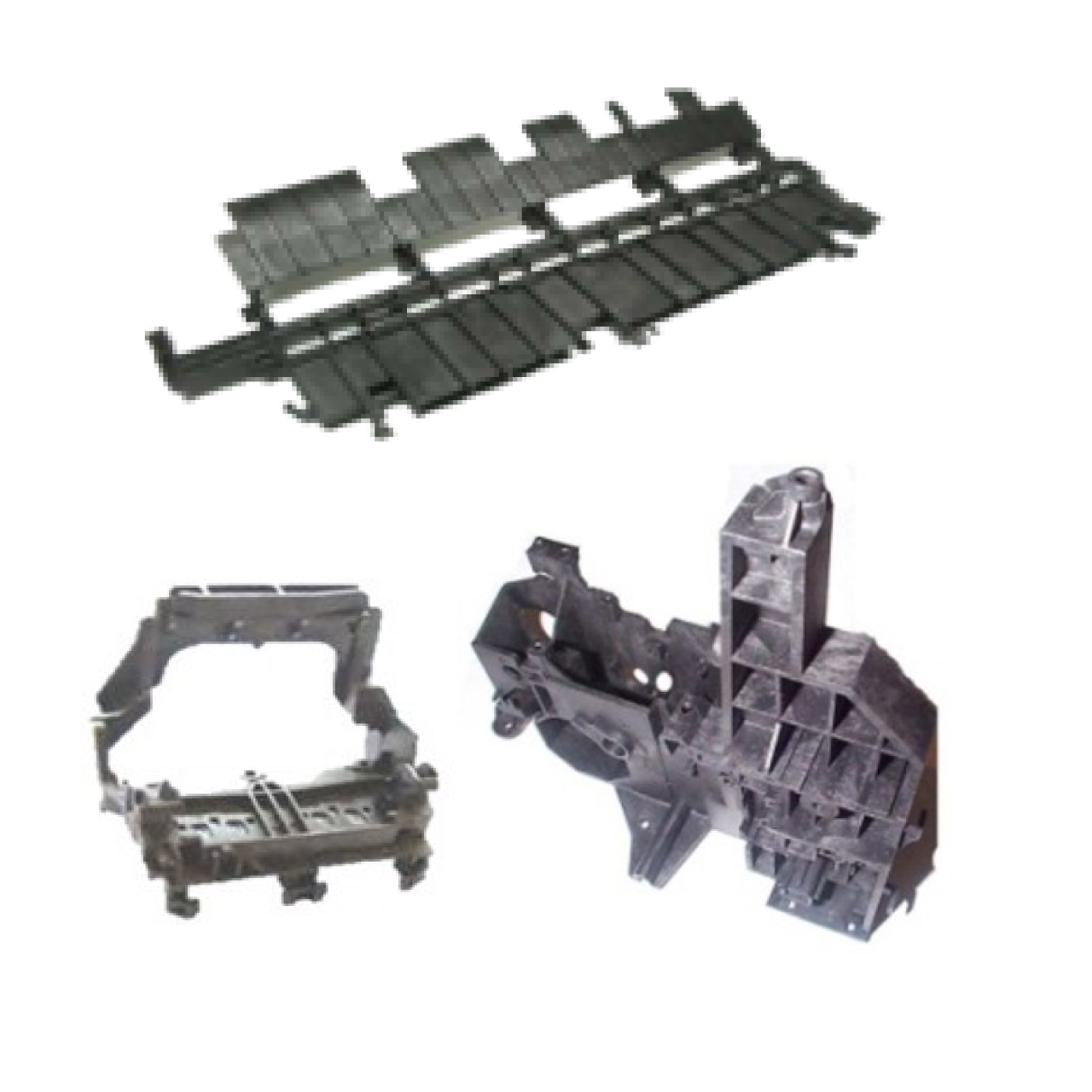
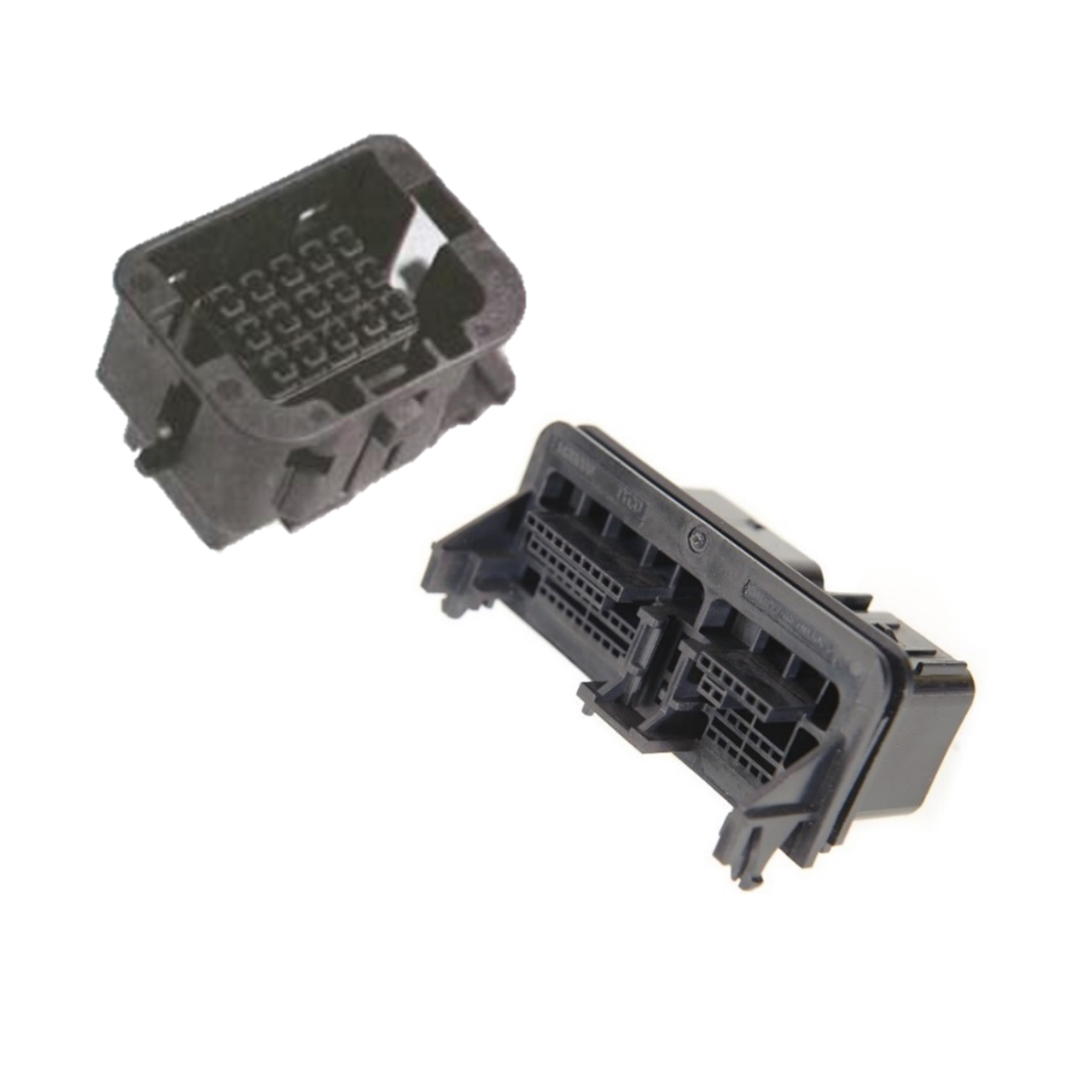