代表のEcoコラム
17. 成形工場の factor4 実現への提案例1
2009.10.08
前回のコラムでは、「松井製作所とfactor4」ということで、松井製作所が会社の使命として成形工場のfactor 4の実現を目指していること、そして、そのための活動の方向性を説明しました。
今回より数回に渡って、松井製作所が現在行っている成形工場のfactor 4実現ための提案メニューの中の提案をいくつか取り上げたいと思います。
● 成形工場のfactor 4実現のための提案メニュー
成形工場のfactor 4実現ための提案メニューを分類すると以下のようになります。
- 1.エネルギーのムダをなくす。
- 2.樹脂のムダをなくす。
- 3.水のムダをなくす。
- 4.時間当たりの生産量を増やす。
これらの提案を実施することにより、プラスチックの成形における「エネルギー・樹脂・水の消費量を半分」にし、しかも「時間当たりの生産量を2倍」にすることを目指しています。今回のコラムでは、この中で「エネルギーのムダをなくす」を取り上げます。
● エネルギーのムダをなくす
成形工程でのエネルギーの消費量をおおざっぱに大きいものから捉えると、
- 1.成形機にて、樹脂を溶融し射出するためのエネルギー
- 2.乾燥機にて、成形前に樹脂を乾燥させるためのエネルギー
- 3.溶融した樹脂を適切に冷却するためのエネルギー
- 4.樹脂原料を自動輸送するためのエネルギー
などのようになります。
どの工程もまだまだエネルギーのムダがありますが、今回のコラムでは、特に乾燥機にて、成形前に樹脂を乾燥させるためのエネルギーのムダをなくすための提案を取り上げます。
● 樹脂乾燥でどれほどのエネルギーのムダがあるか?
プラスチックの成形においては、成形機で樹脂を溶融して射出する前に、樹脂原料の中に含まれる水分をある量まで落とす必要があるものが多くあります。そこで、成形機とは別途に乾燥機を設備することになります。この設備を選定については、例えば、次のように行われます。
ある成形ラインにおいて、最適な成形条件下で、(例えば)最大1時間当たり9kgの樹脂を使用する。
↓
ある程度余裕を見て10kg/hrの樹脂を乾燥できる乾燥機を要求する。
↓
我々のような乾燥機の設備業者は、マージンを見て、12kg/hrの乾燥能力が発揮できる機種を選定しようとする。
↓
ちょうど12kg/hrの能力に相当する機種がない場合、たとえば、15kg/hrの能力に相当する機種をお客様に選定することとなる。
この結果、次のようなことが起こります。
- 最大9kg/hrの樹脂を使用するラインに15kg/hrの能力の乾燥機が設置されることになる。
- また、9kg/hrという数字は、最適な条件下での数字で、通常はここまで能力が出ていない場合がほとんど。
- しかも、成形はずっとフルに連続で行われるわけではなく、金型交換やメンテなどのときに止まっていることもある。
- このような条件下で、乾燥機は、ずっと15kg/hrの能力でフル運転してしまう。
細かい点を省いておおざっぱにいうと、通常のケースでは、消費されるエネルギーの半分程度が、ムダに捨てられる ことになります。しかも、このムダなエネルギーは、かなりの部分が工場内の大気中に放熱され、空調をされている工場では、その放熱分を冷却するために、さらに余分な電力が使われてしまいます。
● どのようにしてこのようなムダを防ぐか?
どうしてこのようなエネルギーのムダが起こってしまうかというと、それは、これまでのほとんどの乾燥機は、どんな条件下でもフル運転するような設計になっているからです。
そこで、ムダを防ぐには、実際の樹脂の使用量に応じて、乾燥に問題がない範囲で、乾燥の能力を変化させることが必要 です。
では、どのようにすれば、実際の樹脂の使用量に応じて、乾燥に問題がない範囲で、乾燥の能力を変化させることができるでしょうか?
例えば、次のようなことが考えられます。
- 乾燥機の中の樹脂の水分値を計測し、それがある基準値を下回るぎりぎりのところになるように、乾燥能力を変化させる。
- 乾燥機から消費される樹脂の質量を計測し、時間平均あたりの消費量に合わせて、乾燥能力を変化させる。
どちらの方法も、計測に時間が掛かりすぎたり、コストがかなり高くなってしまうなどの問題があり、実用的ではありません。
● 樹脂のムダな乾燥を防ぐ「乾燥風量適正化システム」
松井では、つぎのような対策をとることにしました。乾燥ホッパーからの戻りエアーの温度がある一定温度になるように、乾燥風量をコントロールする。
乾燥機では、通常、乾燥機から材料が消費されると、それを補う分の材料が新たに上部から補給されます。その材料は、通常、周囲雰囲気の温度に近い低い温度です。そのため、材料の消費量が多いほど、頻繁に上部に冷たい材料が補給されるために、乾燥ホッパーからの戻りエアーの温度は、平均して低温になります。一方、材料の消費が少ない場合には、、新たな冷たい材料が上部から供給されませんので、乾燥ホッパーからの戻りエアーの温度は、どんどん高くなっていきます。
このように乾燥ホッパーからの戻りエアーの温度は、乾燥機からの材料消費量と相関している わけです。
この特徴を利用して、乾燥ホッパーからの戻りエアーの温度計測という簡単で低コストに計測できる値を利用し、この値に連動して、乾燥風量をコントロールすることにより、ムダな乾燥エネルギーを防ぐことができます。
さらに除湿乾燥機においては、上記の対策に追加して、水分の吸着剤の再生工程での省エネも、上記と似た考え方で実現する方法を提案しています。
またこれらの省エネ機能は、すでに使われている既存装置に改造で追加できるオプション になっています。
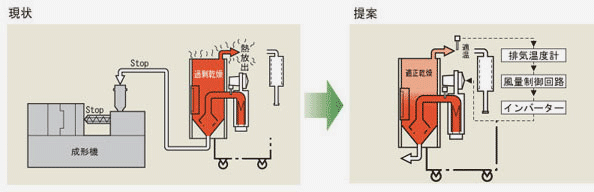
これらの改造により、実際のほとんどのケースにおいて、30~40%程度あるいはそれ以上の省エネ効果が見られます。 しかも、省エネの実現方法が、温度計測のための熱電対の出力によって、モーター回転数やバルブ開閉度を制御して風量をコントロールするという、単純な仕掛けであるために、改造コストも比較的低コストに抑えられます。
このことにより、改造費用の回収については、乾燥機の電気代の節約分のみで、だいたい3年以内にはできる場合が多い という結果になっています。空調関係の負荷の軽減も考慮に入れるとより短い期間に投資を回収できる計算となります。
● エネルギーのムダをなくすその他の提案
その他にエネルギーのムダをなくすための提案としては、成形機のシリンダー部分、乾燥ホッパー、金型、金型温度調節機と金型をつなぐホースなどの断熱を行う方法や、また金型の冷却のためのエネルギーのムダを無くすためのフリークーリングの提案などを行っています。
次回は、「水のムダをなくす」の提案の一例を取り上げます。
2009年10月08日 松井 宏信