概要
金属光造形複合加工とは?
粉末状の金属材料をレーザーで選択的に焼結し、積層することで高精度な形状を成形。各造形ステップでは必要に応じて切削加工も加えることで、寸法精度と表面品質をさらに高めます。
これにより、従来の加工では実現困難であった自由曲面の冷却回路やポーラス(多孔質)構造の形状が可能となり、成形品の品質向上やサイクルタイムの短縮、ガス焼け防止などの多くのメリットを実現します。
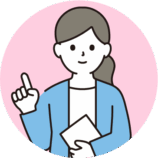
金型部品への採用が可能です。
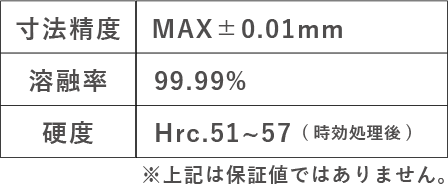
加工の流れ
リコーターによって金属粉末を0.05mmの厚さで均一に敷き詰め、その層を高出力レーザーで選択的に溶融凝固します。この工程を10層分繰り返した後、積層面を高速ミーリング加工によって精密に仕上げます。その後、再びリコーティングからのサイクルに入り、これを繰り返すことで、高精度な3D形状と優れた表面品質を同時に実現します。
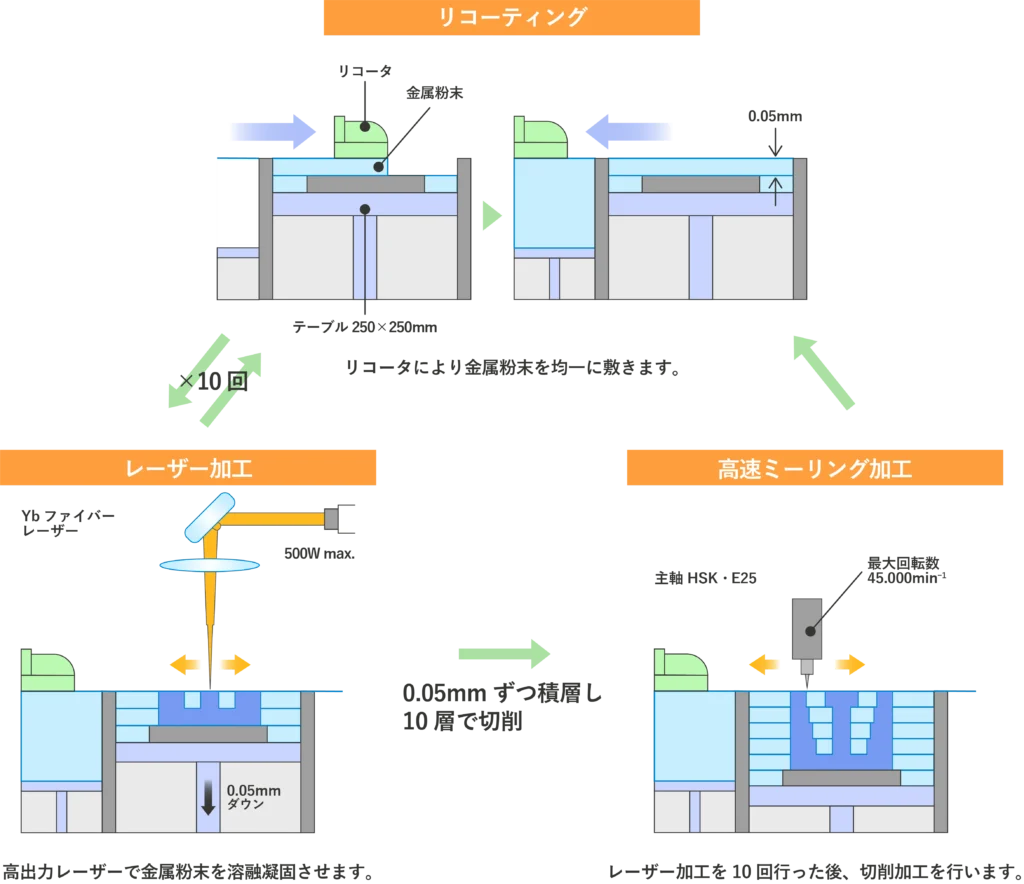
特長
1.3次元冷却水管による高効率冷却で成形サイクルを短縮
3D造形技術により、金型内部に3次元形状の冷却回路を形成します。成形品の最適な部位に沿った冷却水管の配置が可能になることで、冷却効率が大幅に向上し、成形サイクルの短縮と生産性の向上を実現します。
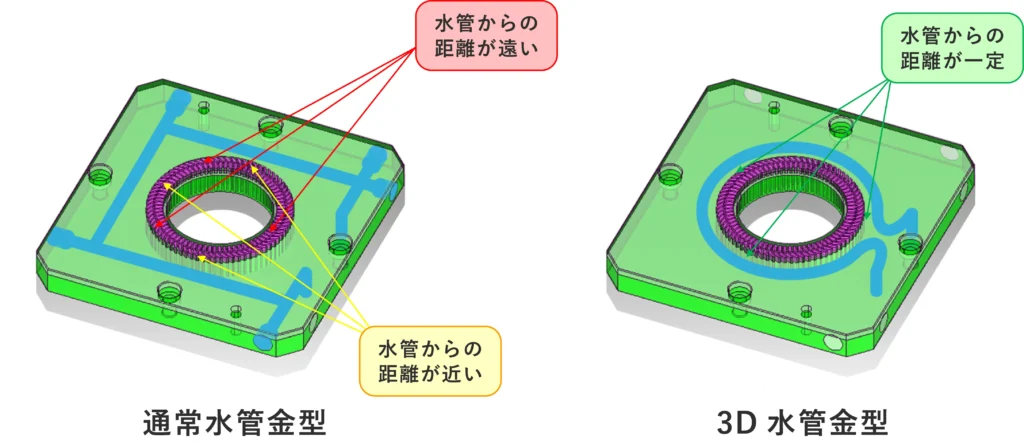
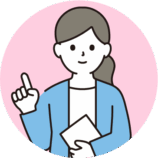
3D金型は、成形品と水管の距離を一定に保つことができ、均一な冷却が可能なため、サイクルタイムの短縮や金型の立ち上げを素早く行うことに貢献します。
2.分割不要の一体構造で高精度な成形を実現
一体で造形することで、部品間の組付け誤差が発生しません。そのため、寸法精度や同軸度、面精度が向上し、成形品のバラつき低減につながります。これは、精度が求められる製品や高機能樹脂成形において特に有効です。
3.ガス抜き用ポーラス構造を自在に設計・設置
造形過程でポーラス(多孔質)構造を形成できるため、金型内のガスベントを自由に設計できます。これにより、ガス焼け・ショートショットといった成形不良を防止し、品質の安定化に貢献します。
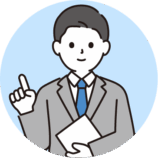
金属3Dプリンタは、ポーラス構造(低密度造形)の製作が可能です。部分的にポーラス構造でガスベントを設けた入子やガス抜きピンが製作でき、成形不良を解消します。
4.複雑形状も一括製造、後工程の削減でスピード納品
従来は複数部品に分割していた複雑な金型構造も、3D造形では一体型で一括成形が可能です。そのため、部品ごとの加工や組付けの工程が不要となり、大幅な納期短縮とコスト低減が図れます。
5.流動解析・冷却解析による設計段階での効果検証
金型設計時に、成形時の樹脂流動や温度分布の事前シミュレーションが可能です。これにより、冷却効率やガス抜き効果の“見える化”ができ、品質改善や設計の最適化をサポートします。
※3Dプリンターによる金型パーツ製作依頼は、問い合わせフォームより受け付けております。
効果事例
下の図は温度レンジ90~97℃の成形品をサーモグラフ化したものです。
左の通常水管は、温度差5℃以上の温度ムラが発生しており、成形品の全体温度が高めの状態です。また、このような温度差は、成形開始時から徐々に大きくなり、連続成形を行うにつれ、より差が広がるため、品質がバラつく原因となります。対して右の3D金型の温度差は、ほとんどありません。
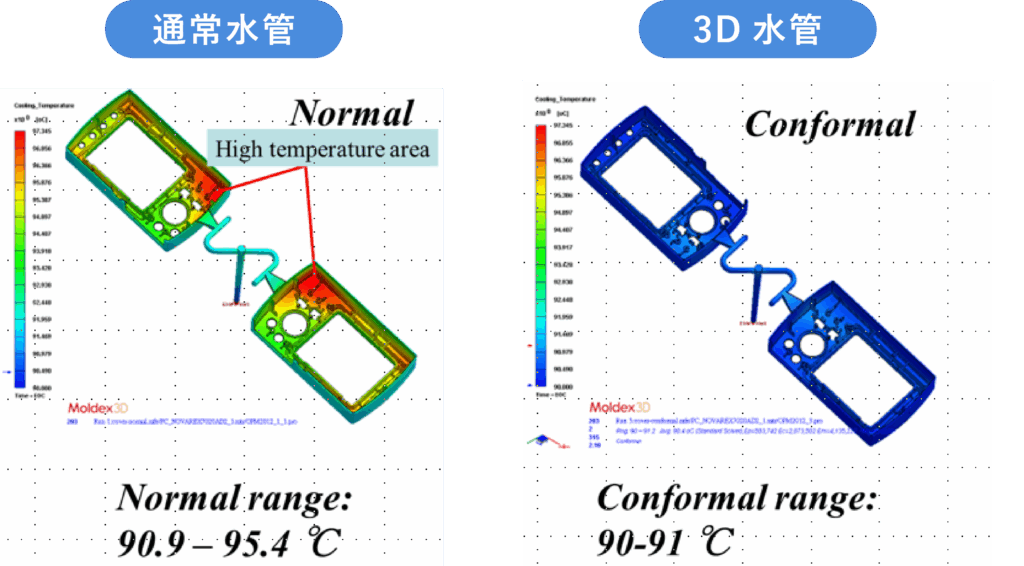