成形工場のfactor4を目指して
樹脂成形の寸法精度悪化の原因と対策
2023.03.17
樹脂成形品の不良にはさまざまなものがありますが、中でも反りやねじれなど変形は、設計寸法の公差から外れると、それ自体で機能を果たせなくなるという事もありますし、後工程の組み立てで悪影響を及ぼし、製品の不具合につながる恐れがあります。
どうしてこのような変形による寸法不良が起きてしまうのでしょうか?本記事では、成形品の寸法精度悪化の原因と対策についてご紹介します。
なぜ成形品の寸法問題が起こるのか
まずは、成形後の寸法不良の原因を見ていきましょう。
材料特性
樹脂は加熱して溶解させると膨張し、冷却して固化する際には収縮する性質があります。その収縮率を考慮して金型を設計し、諸条件を決めて成形する必要があります。
樹脂は結晶性樹脂と非結晶性樹脂に大別できますが、それぞれ収縮率は大きく異なります。結晶性樹脂は、分子が規則正しく並んだ状態で固化(結晶化)するのに対し、非結晶性樹脂は分子がバラバラのままで固化(結晶化しない)するという性質があります。
結晶性樹脂は耐薬品性や耐疲労性は高くなりますが、成形での収縮率が高いため精密な寸法精度が要求される製品では、設計の段階から、より配慮が必要となります。このように樹脂材料自体の特性によって寸法精度が出にくい場合もあります。
不均一な冷却
結晶性樹脂において、冷却速度を速くすると結晶化度は低下するという性質があります。例えば成形品の肉厚な部分と薄い部分、金型の形状や水管の位置などによって、成形品全体が均一に冷却されない場合があります。冷却が不均一になると成形品の部分ごとの結晶化度に差が出るため、反りや歪みなどの寸法不良が発生してしまうのです。
残留応力
特に注意しなければならないことに、残留応力があります。一般的には、物体に対し外部から力が加えられたり、加工や熱処理、冷却などを行った際に、物体の内部に力が残っている状態を指し「残留応力」と呼ばれています。
樹脂の射出成形では、金型内へ樹脂を射出した際、温度の変化と合わせて大きな圧力がかかり、これが成形品内に残ります。時間が経過したり、温度が変化したりすると残留応力は徐々に開放され、成形品の変形や反り、歪みなどを引き起こします。
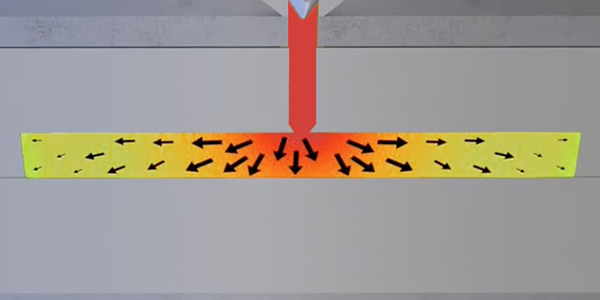
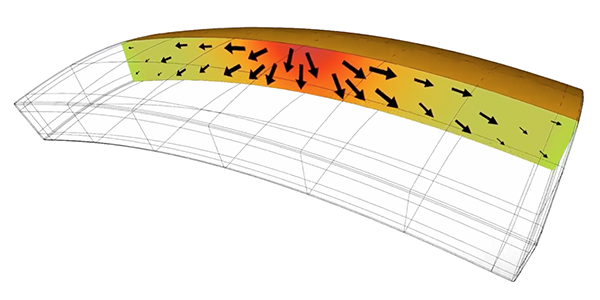
残留応力の原因
残留応力の原因は複雑で、複数の要因が積み重なることで生じると考えられています。
1) 不均一な外力
樹脂成形品は複雑な形状をしているものも多く、部位による厚みの差や、ゲート位置により、射出時に圧力のかかり易い部分とそうではない部分があります。
その他にも、成形品を金型から取り外す際にアンダーカットがあって金型に食いついてしまったり、突き出しピンが不適切な配置になっていたりするなどの原因によって、成形品に不均一に外力がかかってしまう場合があります。
2) 不均一な冷却
成形品の形状と、金型の冷却水管の位置や形状によっては、冷却速度にもバラつきが発生します。
通常の金型では、冷却するための水管はドリルで開けられており、冷却水の経路は直線的に構成されているため、どうしても場所によって冷却に差が出てしまいます。また、厚肉部位と薄肉部位でも冷却速度が異なります。
3) 素材特性による不均一な収縮率
強度や耐久性を上げるために強化繊維を配合した樹脂を使用することがあります。強化繊維を配合すると、一般に成形収縮率は小さくなりますが、繊維は流動方向に配向しやすいため異方性が生まれ、向きにより収縮率に差異が発生し、結果として応力が残ってしまう場合があります。
このように、成形品に不均一にかかる外力や、成形品内部の冷却速度、収縮率の差が残留応力の原因になると考えられています。
成形品の寸法精度を向上させる方法とは
「成形品の寸法精度を向上させる」とは、金型設計時に狙った寸法精度以上に向上させるという事ではなく、成形後の形をそのままに維持する(変形させない)、寸法を安定させる方向のお話しです。成形後の変形を抑えるためには、成形時に発生する応力を軽減する、残留応力を逃がす、の大きく2つの方法に分けられます。
まずは、昔から鉄製品の熱処理加工で使われてきた、残留応力を逃がす手法「焼きなまし」=「アニール処理」からご紹介しましょう。
アニール処理
成形後の樹脂成形品の残留応力を低減させるためには、熱処理を加える方法があります。これをアニール処理といいます。
結晶性樹脂の場合は実使用温度より10~30℃高い温度下に一定時間置き、その後ゆっくりと冷却することで結晶化度を上げます。これによって耐熱性や剛性を上げることができ、変形を防ぎます。
また、非結晶性樹脂では、荷重たわみ温度より少し低い温度に一定時間置くことで、樹脂内の分子が動けるようになるため、残留応力を開放させることができます。その状態でゆっくり冷ますことによって変形が起きにくなります。
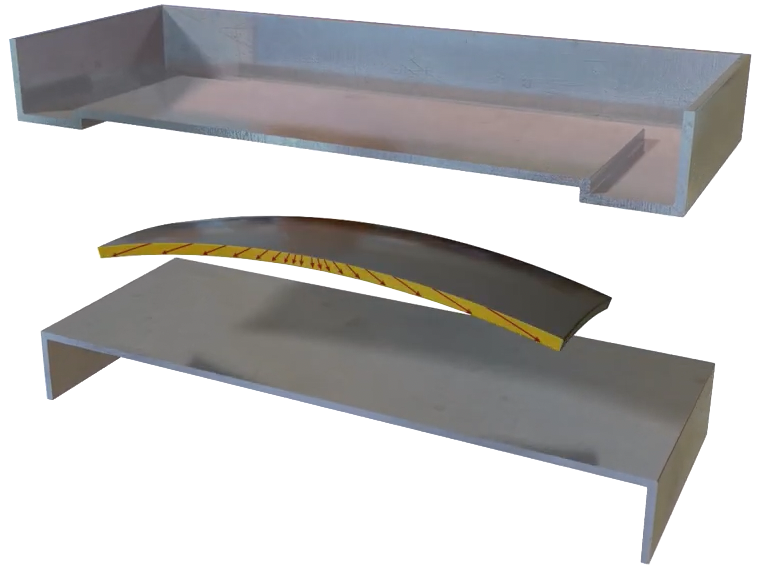
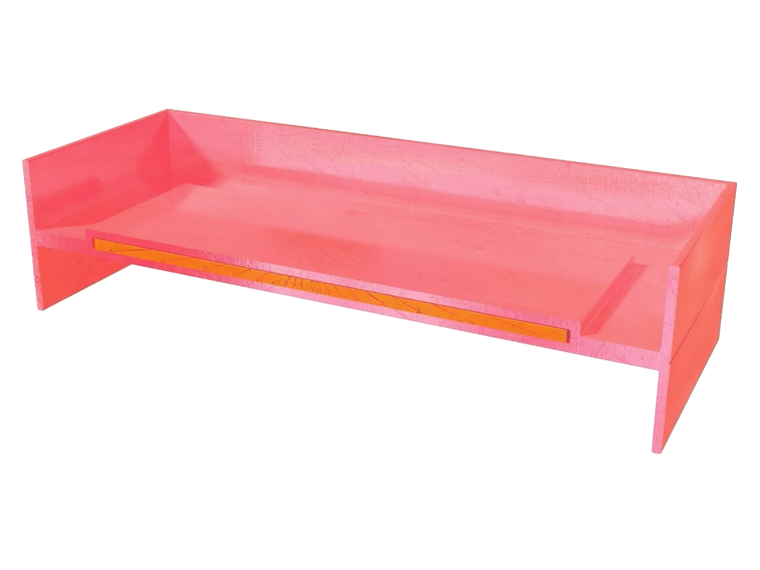
専用のアニール炉を用意するのは大掛かりでなかなか大変だと思われるかもしれませんが、マツイの箱型乾燥機 POは、アニール炉としても長年多くのお客様にご利用いただいております。然程場所も取りませんし、導入コストも抑えられます。
多ゾーン温調
成形品の形状が原因で冷却速度に差が出てしまう場合には、多ゾーン温調という方法が有効です。
通常の成形では、1台の金型温度調節器を使用して金型を冷却しています。そのため立体的な成形品では、部位毎で成形面と冷却水管との距離に差があり、冷めやすい部分と冷めにくい部分ができてしまいます。この問題に対して、複数の金型温度調節機を使った多ゾーン温調では、部分によって異なる温度に設定できるため、異なる部位による冷却速度のバラつきを抑えられます。
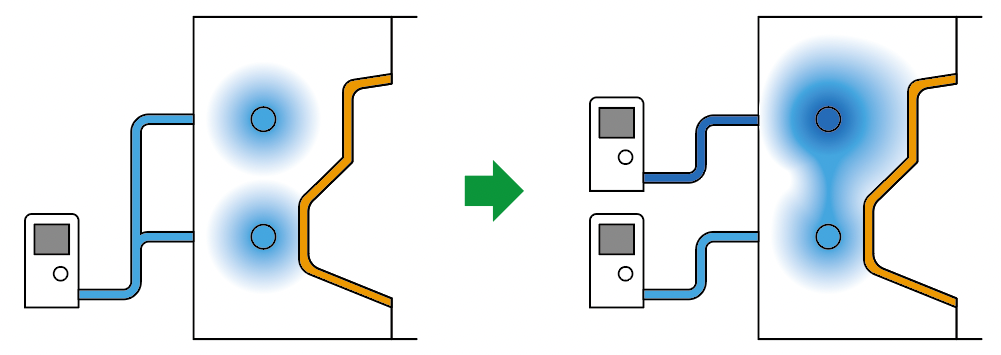
3D水管
これまでの通常の金型水管は、ドリルで穴を開け直線で繋ぎ、不要部分を埋める手法で作られてきたため、直線的な経路しか設けられませんでしたが、3Dメタルプリンターを使えば、立体的な成形品でも成形面に沿わせて自由な形に冷却水管を通すことができます。これによって、複雑な形状の成形品でも、均一な冷却が可能となります。⇒ 3D 水管金型入子
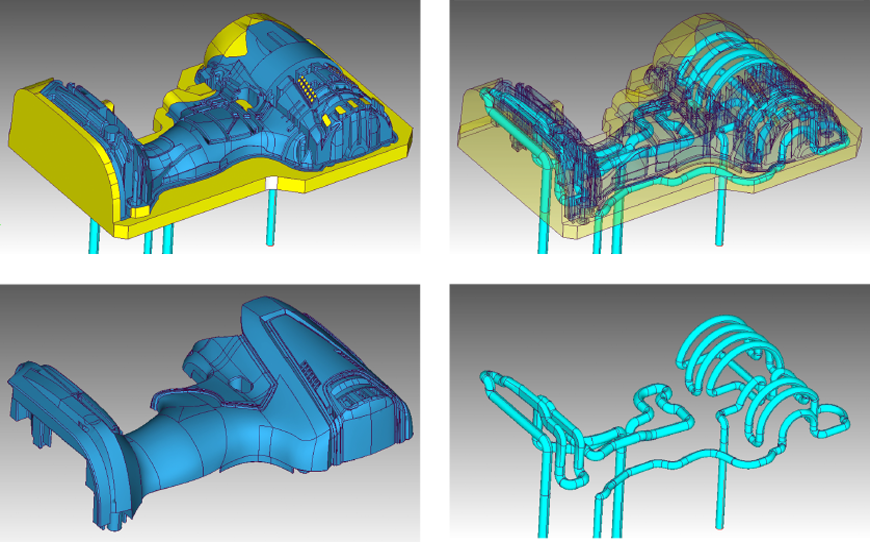
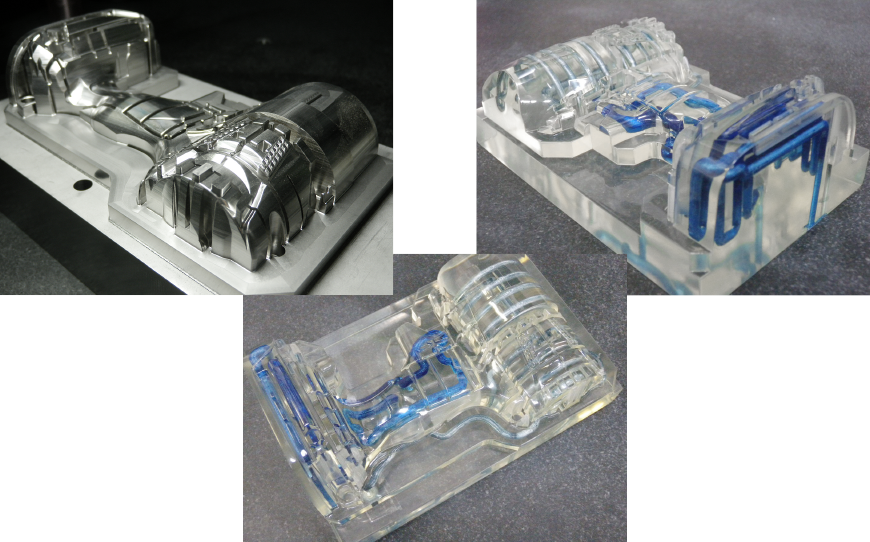
ヒート&クール成形
樹脂を金型に充填する際に、金型温度を高くして、その後急冷却する、この動作を繰り返して成形を行う技術です。ウェルドラインを見えなくするなど外観品質向上に効果があるだけでなく、樹脂を注入する際の流動性が向上するので、薄肉、厚肉といった樹脂が流れにくい成形品でも充填しやすくなります。流動性が上がる = 少しの力で充填できるため、残留応力の影響が抑えられ、寸法精度が向上します。⇒ヒート&クール成形
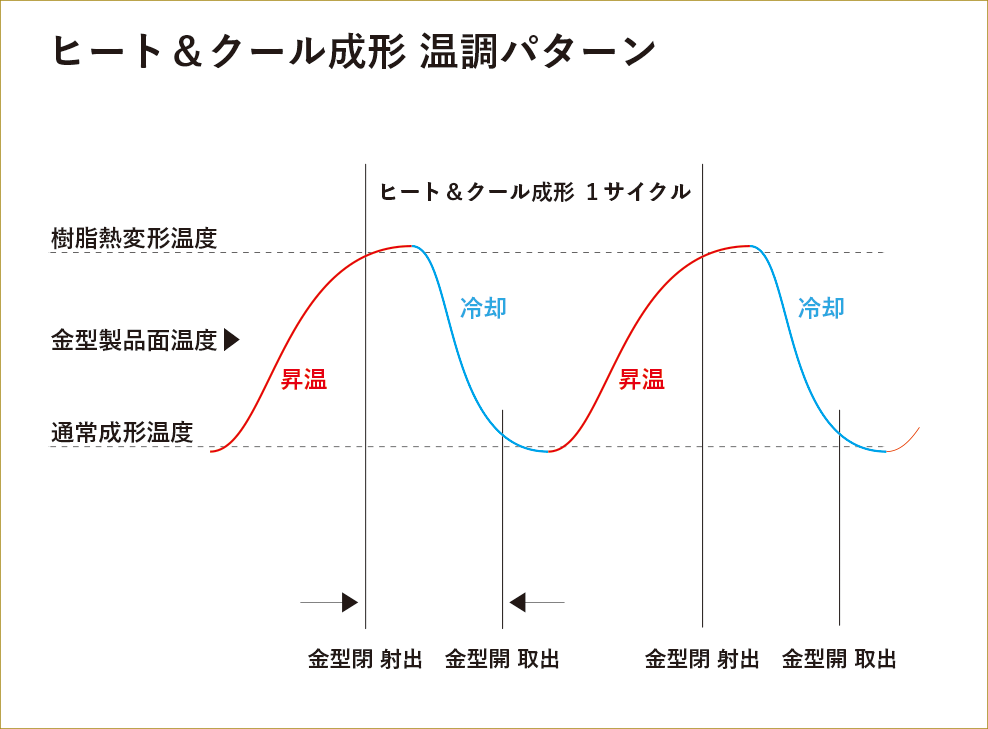
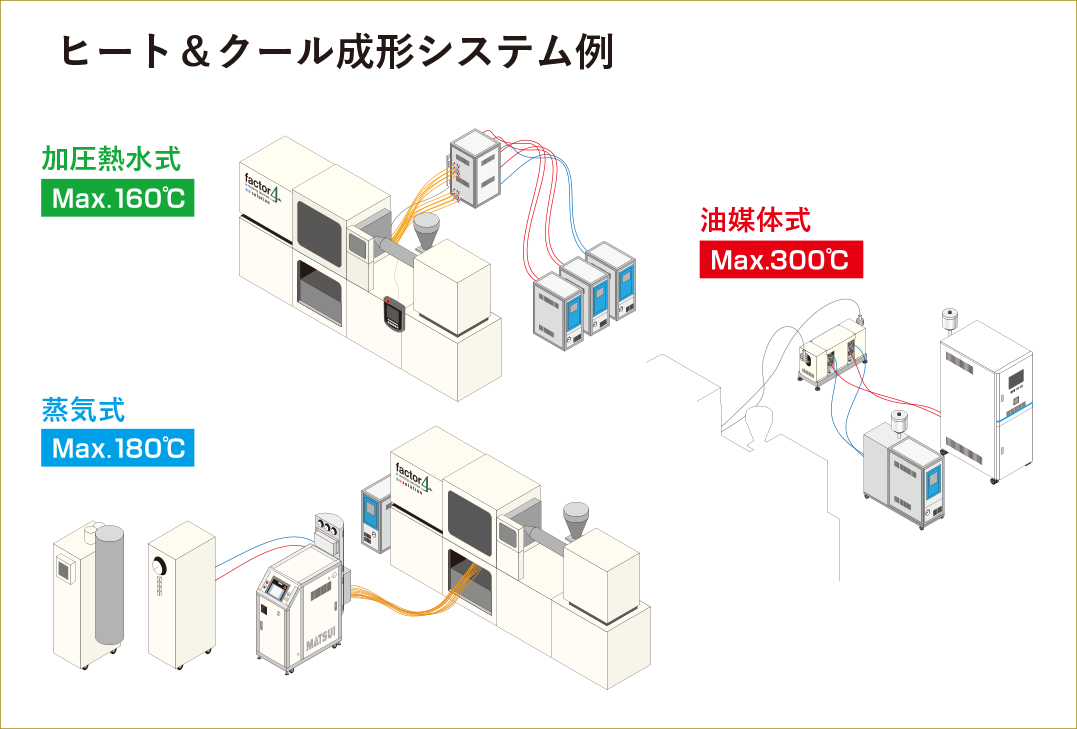
発泡成形
樹脂に発泡剤を混ぜる、または超臨界流体を発泡剤として樹脂に溶かし込み、金型に充填した後の圧力低下によって成形品内部で発泡を起こさせるという成形方法です。樹脂内部で気泡が発生することにより、圧力が均等にかかるため、1方向の応力が残らず、反りやヒケなどの変形不良が抑えられます。
⇒ MuCell®微細発泡成形システム
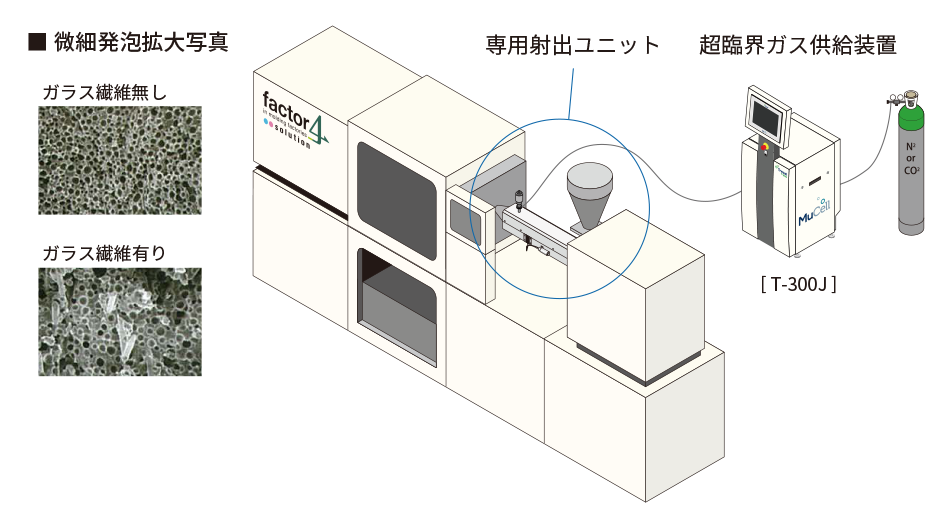
まとめ
樹脂成形品の寸法問題は、樹脂の特性や冷却方法、残留応力が大きく影響しています。これらは樹脂の性質を知り、技術を活用することで対策できます。成形品の寸法精度を上げることは、成形工場の技術力を示すことにもつながり、価値向上に寄与します。
松井製作所では、成形品の寸法精度向上のためのご提案を用意し、新しい設備や技術の導入をサポートいたします。ぜひお気軽にご相談ください。