成形工場のfactor4を目指して
プラスチック成形工場の環境対応【後編】樹脂のリサイクル
2022.08.30
成形工場が取り組む、樹脂のリサイクル
プラスチック成形工場の環境対応をテーマに、前編ではCO2排出の削減に関するソリューションをご紹介しました。後編では、成形工場では欠かせない「樹脂」について、ムダを削減するためにどのようなアプローチができるかをご紹介いたします。
ご存じのとおり、プラスチック樹脂の原料は石油です。SDGsやカーボンニュートラルというと、プラスチックは悪者にされてしまいがちですが、プラスチックは私たちの生活にとってなくてはならない存在となっています。プラスチック成形工場にできることは、ムダをなくし、リサイクルできるものはリサイクルして、資源を最大限に活用していくことです。
そのためのソリューションをご提案いたします。
項目が多いので、目次を置いてみます…
1. 配合の見直しでムダをカット
- 装置内の混ぜ残り削減
- 色替え工程の見直し
- 材料配合の適正化
2. 取り組みやすい現場改善
- ブリッジの防止
- 再吸湿の防止
- 樹脂使用量の削減
3. 廃棄物のリサイクル率UP
- スプルーやランナーの再利用
- 高価なエンプラのリペレット化
まとめ
それでは進めましょう。
1. 配合の見直しでムダをカット
「まずはどこからリサイクルを始めるべきか?」と悩む方もいらっしゃるかもしれません。実は、成形工程の最も初めの段階となる原材料の配合工程から見直すべきポイントが多数存在しています。
装置内の混ぜ残り削減
近年では、多品種少量生産の傾向が強くなり、材料交換の頻度が高くなってきています。成形材料の切り替えや色替えは手間がかかるだけでなく、装置内に残った材料は次の成形品に混ざらないよう、すべて廃棄となるため、多くのムダが発生してしまいます。
質量式配合装置JCW2-i は、セルフコントロール機能を搭載し装置自体が成形機の樹脂の使用量に合わせて材料供給量を調整します。これにより、装置内に残ってしまっていた残材を最大99%削減できるようになりました。
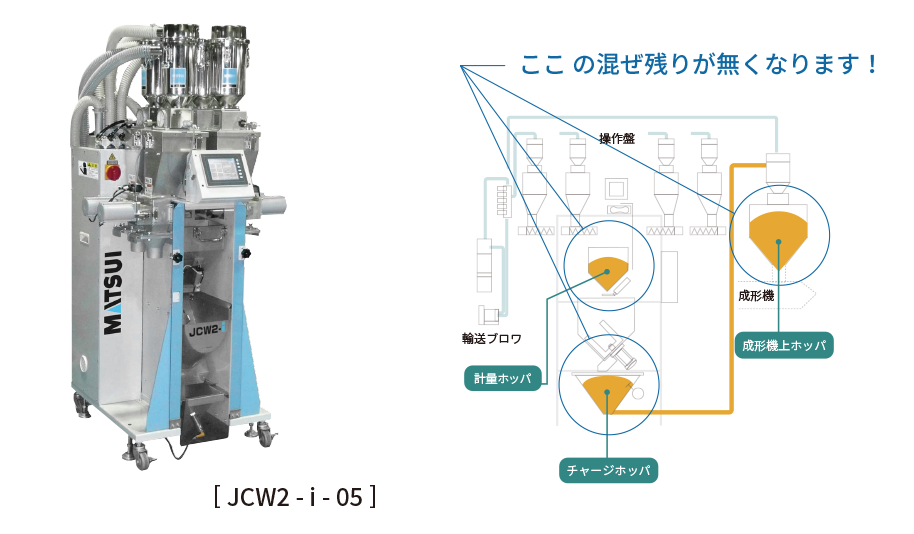
トレーサビリティシステムと併せて使用することで、樹脂の使用量を見える化し、ムダのない原材料管理が可能となります。
色替え工程の見直し
色替えで発生してしまうムダを減らす方法はさまざまです。
一般的に、ミキシングノズルには材料分布の均一性や効率的な材料替え性能が求められます。既に、市場にはさまざまなミキシングノズルがありますが、どちらか一方に優れているノズルはあっても、両方を兼ね備えているものはなかなか存在しません。
もし、今お使いのミキシングノズルにご不満をお持ちでしたら、こちらのスタティックミキサーと入れ替えていただくことで、より大きな効果が得られる可能性があります。
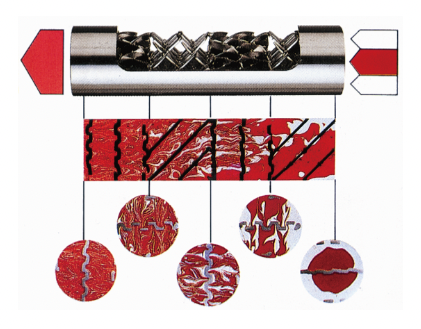
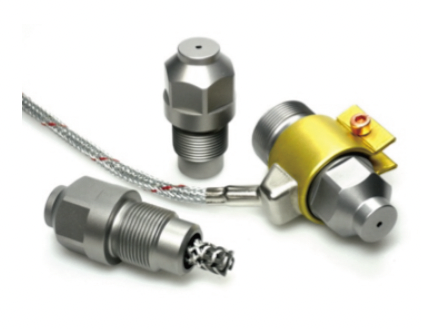
スタティックミキサーは可動部が無く、エレメントを複数組み合わせることで、効率的に着色剤の均一分散を実現し、カラーストリークの発生を抑えます。
滞留レス構造によりわずか3〜5ショットで色替えが完了しますので、材料替え時の樹脂のムダを大幅に減らせます。材料、及び温度分布の均一性やスムーズな材料替えを実現している点に定評があります。
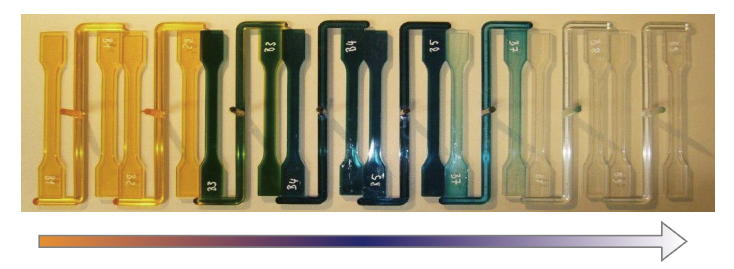
温度分布の均一性が向上するため成形品質のばらつき防止にもなります。また、電源が不要なため、短期間で投資回収が可能です。
材料配合の適正化
樹脂の着色にはマスターバッチを使用している成形工場も多いかと思います。このマスターバッチは高価なだけでなく、ペレットとサイズや比重が異なっており材料が片寄ることによって色ムラが起こってしまうリスクがあります。
質量式配合装置 JCLW は、成形機上に設置して計量・配合できるため、輸送による材料の分離がなくなるだけでなく、マスターバッチを一粒ずつ等間隔で供給するため混ぜ合わせる必要がなく、高精度に適量を配合できるので、色ムラを気にして多めに配合していたマスターバッチの使用量を必要最小限に抑えられます。
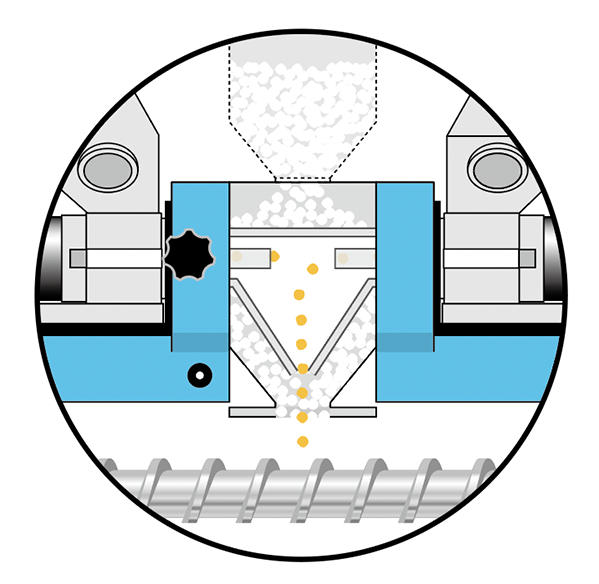
2. 取り組みやすい現場改善
配合以外にも目を向けるべき工程は多く存在します。その中でも取り組みやすい改善の例をご紹介いたします。
ブリッジの防止
リサイクル材や軟質性の材料などを使用した際に、乾燥ホッパーのコニカル部でブリッジが発生して詰まってしまうことはありませんか? 一度詰まってしまうと、成形機を止めてスクリュー内に残留した樹脂をパージする必要があるため、ムダな樹脂の廃棄が生じるだけでなく、その都度手作業で取り除くなどの手間が発生し、生産計画にも支障が出てしまいます。
このブリッジ防止装置は、乾燥ホッパーのコニカル部に沿って羽根を回転させ、樹脂を動かし続けることでブリッジを防止します。標準品に後付けで取り付けることが可能です。
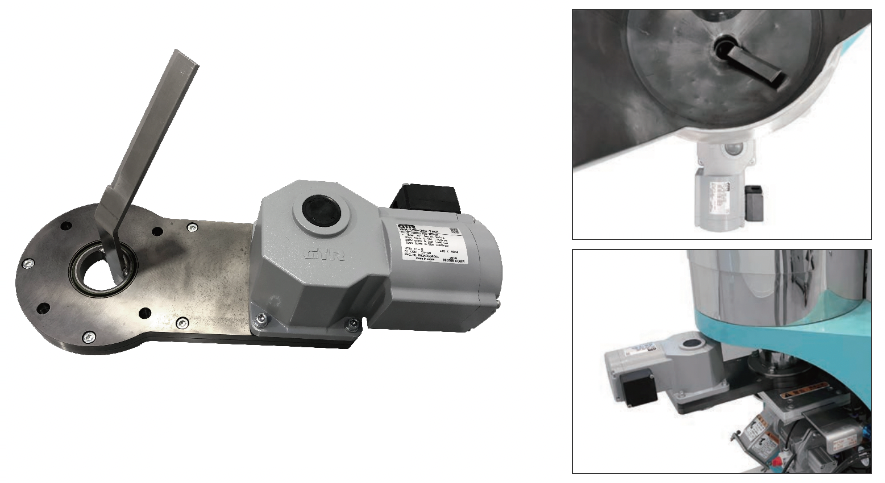
再吸湿の防止
樹脂のムダをなくすために最も効果的な対策は成形不良を削減することです。成形不良の原因はさまざまですが、もしかしたら配管内に残留している樹脂の吸湿が原因かもしれません。ホッパーの下部に プッシュダンパ を取り付けるだけで材料の残留を防止し、既存のローダーを利用したバッチ輸送システムを構築できます。
樹脂使用量の削減
樹脂のムダを無くす取り組みとして、廃材をリサイクルする、材料使用量の見える化や適正配合で樹脂使用量を必要最小限に抑える、効率的な色替えにより樹脂の廃棄量を減らす、配合ムラやブロッキングを防止して成形不良を発生させない、という方法をご紹介してきましたが、成形に使用する樹脂そのものを減らす、発泡成形という成形方法があります。
弊社がお勧めする微細発泡成形技術MuCell®️は、ガスを溶解ポリマー内に均一に拡散・溶解させることで、樹脂内に微細なセル構造を形成します。この成形方法を使う事を前提に、成形品を設計から見直す事で、機械的強度や寸法精度を損なわず、〜20%の重量低減が実現可能となります。また、発泡剤などを使う方法と異なり、ガスのみを使用するため、廃材のリサイクルも可能となりますので、この点においても樹脂使用量の削減につながります。
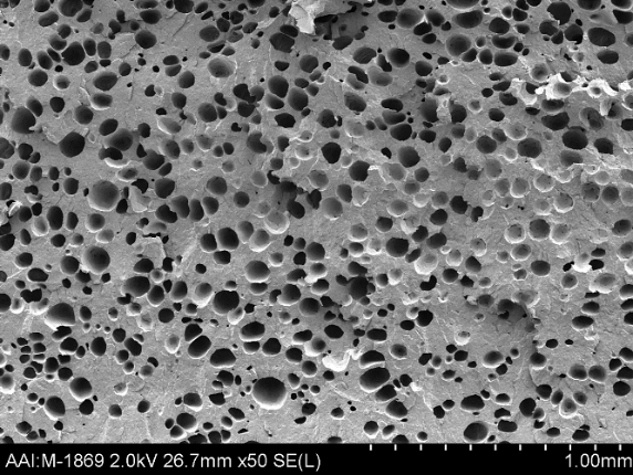
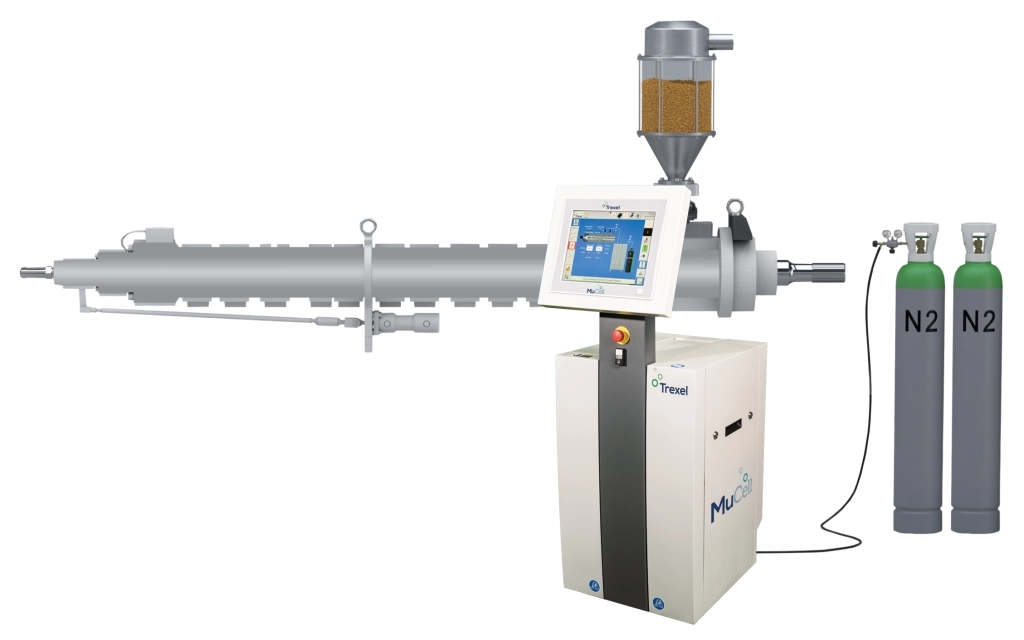
この技術は、軽量化が望まれる自動車部品成形などで広く活用されていますが、サステナビリティが注目されている昨今にあっては、今後より多くの成形品でも採用が進むものと思われます。
3. 廃棄物のリサイクル率UP
そして、最後に忘れてはならないのが、成形時に発生する廃棄物のリサイクルです。
スプルーやランナーの再利用
廃棄物のリサイクルを考えた際、真っ先に思い浮かべられるのは、スプルーやランナーのリサイクルではないでしょうか。
小型精密成形品では、製品よりもスプルー・ランナーの方が大きいという事が多々ありますし、これをすべて廃棄してしまうのはもったいないことです。
従来の粉砕機では、ミスカットや粉立ちの多さから、粉砕材をリサイクルに使用すると成形不良につながってしまう問題がありました。また、粉砕機は成形品の色や、樹脂の種類を変えるごとに清掃をしなくてはならず、こうした手間も大きな負担となっています。
そのため、粉砕してリサイクルした方が良いことは分かっていても、成形不良の懸念や、清掃の煩雑さからスプルーやランナーを廃棄しているという成形工場も多いのではないでしょうか。
マツイが提案する 低速粉砕機SMGL3-G3/G1 や エラストマー専用の粉砕機 MGL2-TPE は、新設計のカッターとスクリーンレス構造によりミスカットや粉の発生を抑制します。SMGL3では、清掃箇所が大きく開き、前面から作業が行えるため、成形機にセットしたまま短時間で、簡単・確実な清掃が可能ですし、MGL2もまた清掃箇所を工具なしでフルオープンにできるため、作業に手間を取らせません。
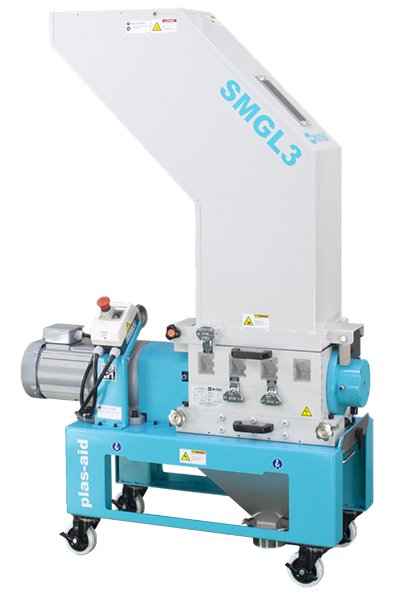
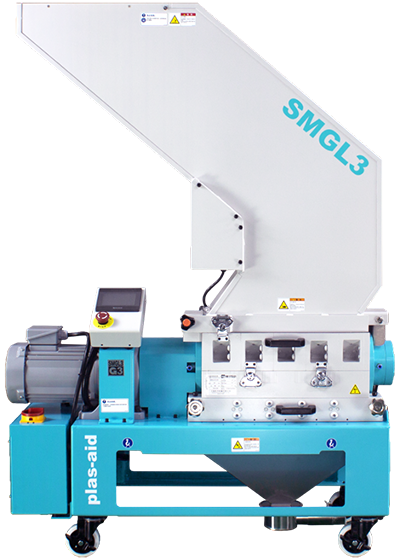
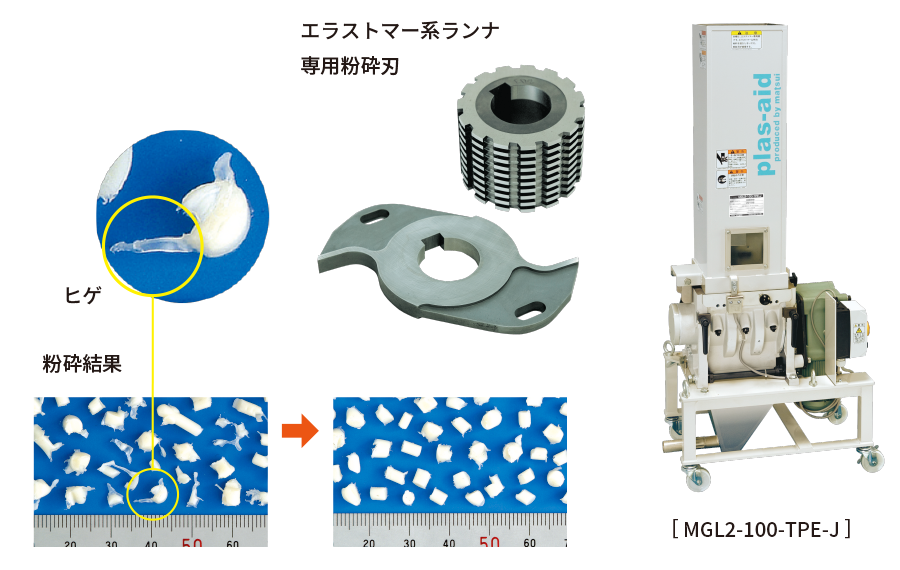
これらの粉砕機をご使用いただく事で、成形不良発生の可能性と、材料替え時の清掃の手間が低減されますので、スプルー・ランナーのリサイクルに取り組んでみてはいかがでしょうか。
高価なエンプラのリペレット化
高機能なエンジニアプラスチック(エンプラ)の使用量は年々増えています。これまで、エンプラはリサイクルが難しく、スプルーやランナーは廃棄せざるを得ませんでした。そこで活躍するのが エンプラ専用のペレタイザ です。無剪断可塑化スクリュアッシィ「SPIRAL LOGIC」を搭載し、炭化によるコンタミや黒点などの発生を無くし、安定した射出を実現する事で、従来では難しいとされていた エンプラのリペレット化に成功しました。
微細ミストと空冷の組み合わせでコールドカットするため水槽は不要、ペレットの黄変を防ぎます。PAやPC、LCPなどでの実績があります。
エンプラは材料自体が高価なため、リサイクルすることができれば大きなコスト削減にも繋がります。
まとめ
SDGs、カーボンニュートラルと、プラスチック業界にとっては厳しい状況が今後も続いていくことが予想されます。しかしこうした潮流に対する新しい技術は日進月歩で開発されており、これらを効果的に取り入れていくことで、環境的課題をクリアするだけでなく、企業価値の向上にも繋がります。
大がかりな装置や機器を導入する以外にも、取り組みやすい方法で樹脂のムダを防ぐソリューションがあります。環境にやさしいだけでなく、生産性を維持し、作業員の負担軽減、現場環境の改善につながります。
松井製作所では「豊かさ2倍、資源消費半分」という factor4 の考え方に基づき、成形工場の環境対応、資源生産性向上のご提案を積極的に行ってまいります。お困りの方はお気軽にご相談ください。
CX デザイン部 飯島 泰彦