成形工場のfactor4を目指して
「生産量UP」不良低減&安定生産、成形サイクルの短縮
2022.01.06
「生産量UP」と言っても、皆さん、通常できうる限りのやり方で、目一杯生産されておられるものと思いますので、「そこから更にどうしろと!?」と思われるかもしれません。
単純に考えますと、成形機が連続して動き続けている状態、100%の稼働率で最も生産量が多くなる状態なわけですが、現実的には、成形品を変える毎に金型を交換したり、材料を変えたりといった、成形機が停止する「段取りの時間」が必要となります。ここまでは生産に必要な時間と言えるでしょう。
ですので、ここでは大きく以下の4つのアプローチによる「生産量UP」を考えていきたいと思います。
1. 成形不良の低減
2. 初期状態の維持
3. 段取時間の短縮
4. サイクルタイムの短縮
1. 成形不良の低減
成形不良と一言で言ってもその症状や原因は多岐に渡ります。現象としては、糸引きや離型不良、ショートショット、ガス焼け、バリ、フローマーク、シルバーストリーク、ウェルドライン、ヒケ、反り、ボイド、黄変、変形… 原因としては、金型形状(設計)や成形条件、樹脂の選定や乾燥状態、環境(気温/湿度)・冷却効率の変化、コンタミやガスの発生などがあげられます。
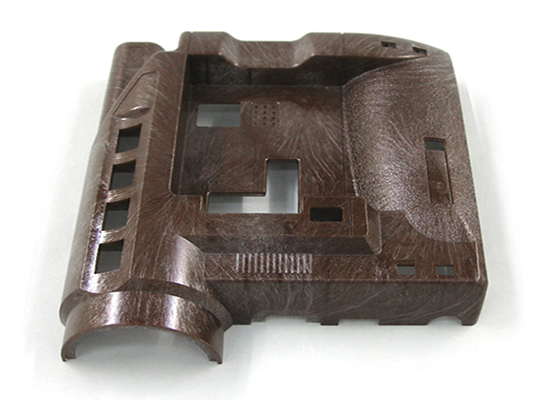
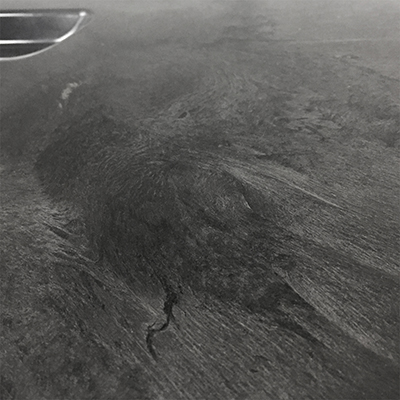

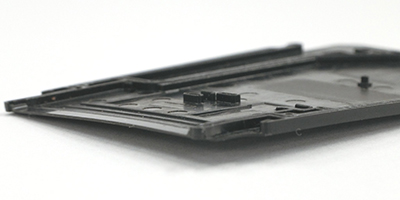
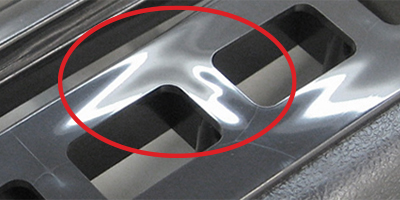
これだけ様々な不良・不具合がありますので、それぞれ個別に解決してゆく必要があります。どれも満遍なくというわけにはいきませんが、弊社は長らく樹脂成形に携わる皆様と共に歩んで参りましたので、金型の樹脂流動解析や樹脂の適正乾燥、ガス取り、コンタミ対策、ウェルドレス成形装置&ノウハウから、IoT を利用した環境や成形状況の監視、工場全体の水質管理まで、お客様の工場での問題・課題に対し、解決しうるソリューションを幅広く取り揃えております。
2. 初期状態の維持(装置不具合の防止)
調整が完了し量産開始から暫くの期間は問題なく良品が取れていたのに、徐々に成形不良が増えてきた、良品を取るために成形機の条件や金型温調の設定温度を変え、結果的にサイクルタイムが伸びてしまった、なんて経験はありませんか? 一つには、季節による温度変化によるものかもしれませんが、見過ごされがちなのが冷却水の水質です。
社として水質維持の重要性を認識されている工場でも、管理を担当されている方の他は、工場巡回水を目にする機会はなかなかないのではないでしょうか。また、貯水槽やクーリングタワーの水を見ても、明らかに汚れていなければ気に止められる事もないでしょう。実は、見た目が綺麗な水でも、装置トラブルや、冷却効率の低下に繋がってしまう場合があります。
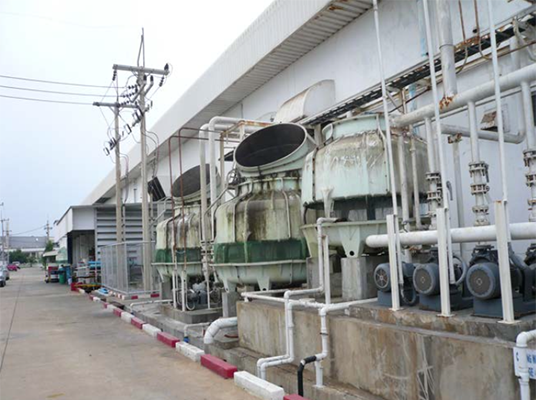
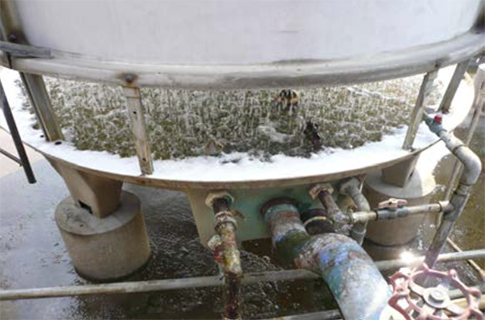
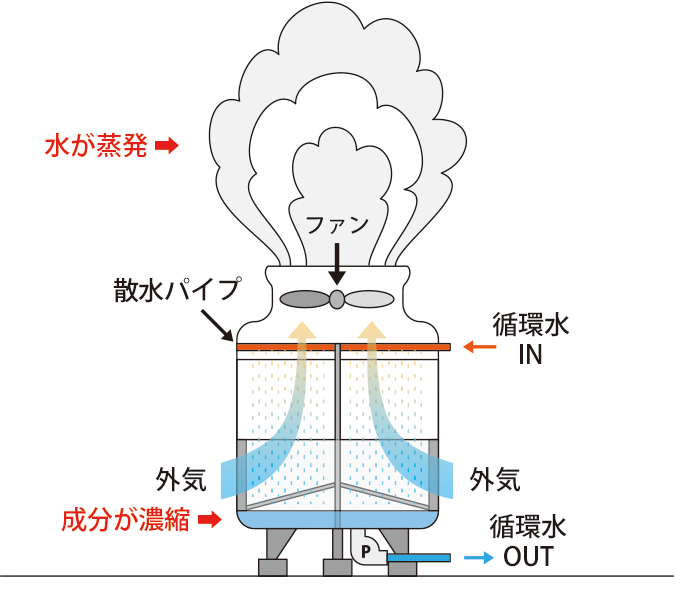
冷却効率が落ちる原因は、外から入ってきた粉塵や植物の胞子、冷却系で発生するバクテリアや錆、水分中に含まれていたカルシウムやマグネシウムが化合した石灰などで、これらが冷却水経路の内壁に付着していく事で、温調対象物と十分な熱交換ができなくなるのです。詰まってくると装置の不具合、故障にもつながります。
工場立ち上げ時やライン新設時から、水質維持を考慮した仕組みを導入できる事が理想ですが、皆様の環境は様々ですので、状況に合わせ、フィルターなどで冷却系の浮遊物・不純物を取り除く、スケールを分解して回収する、水管洗浄、イオン化、防錆剤、殺菌剤、水質改質剤など、様々なソリューションの中から最適な手法・方法、ステップアップをご提案いたします。
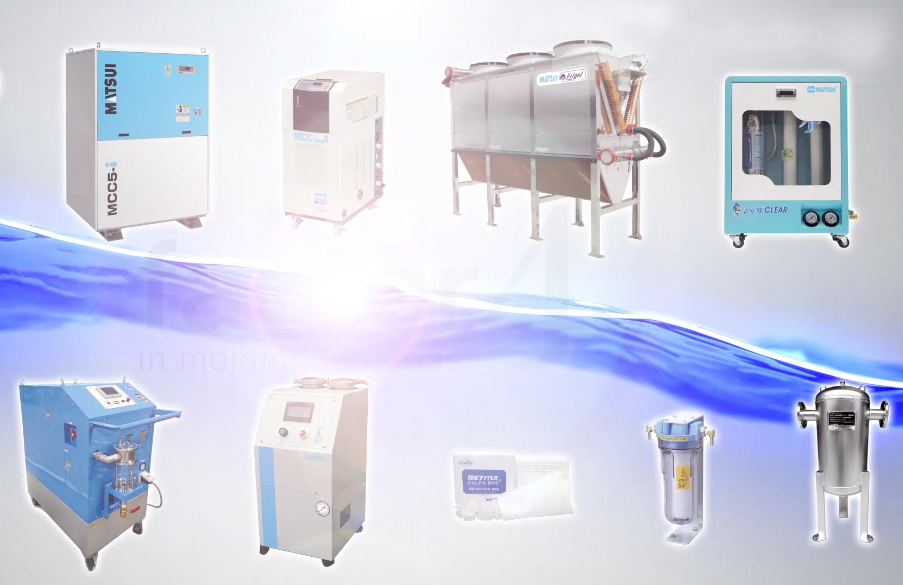
3. 段取時間の短縮
段取りで手間と時間がかかるのは、材料替えと金型交換でしょう。材料替えでは、輸送経路、配合装置、成形機上捕集器、シリンダー、スクリューと多くの部位の材料をすっかり入れ替えなければなりませんし、前の材料が残って混ざり込まないよう清掃も必要です。
工程順に、例えば次の材料は予備乾燥をかけておく、輸送ラインを簡単確実に切り替える、生産状況に合わせ配合材をピッタリ使い切る、滞留を無くし短時間で材料を置き換えるなど、対象となるパートが多いからこそ、手を入れられる、時間の短縮しろがあります。
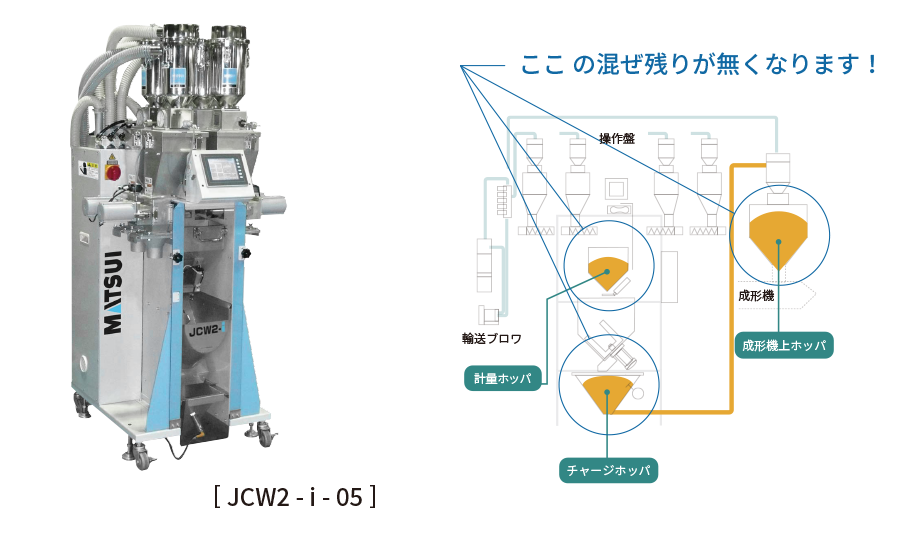
詳細はこちら ⇒ インテリジェンス機能付き質量式配合装置 JCW2-i
金型交換では、金型の温度が下がるのを待ち、人手を使って成形機から下ろす、次の金型を載せ、配管をつなぎ、昇温するまで待って成形条件の調整に取り掛かる。これらの作業を成形機を止めた状態で行うことを「内段取り」と言い、成形をしながら次の準備をする事を外段取りと呼びますが、この外段取りをどれだけ進めておけるかが、段取時間短縮のポイントとなります。
次の金型を近くで待機させ、予備温調まで済ませておき、簡単に載せ替えができる仕組みがあれば、短時間に効率よく段取りを行えるようになります。
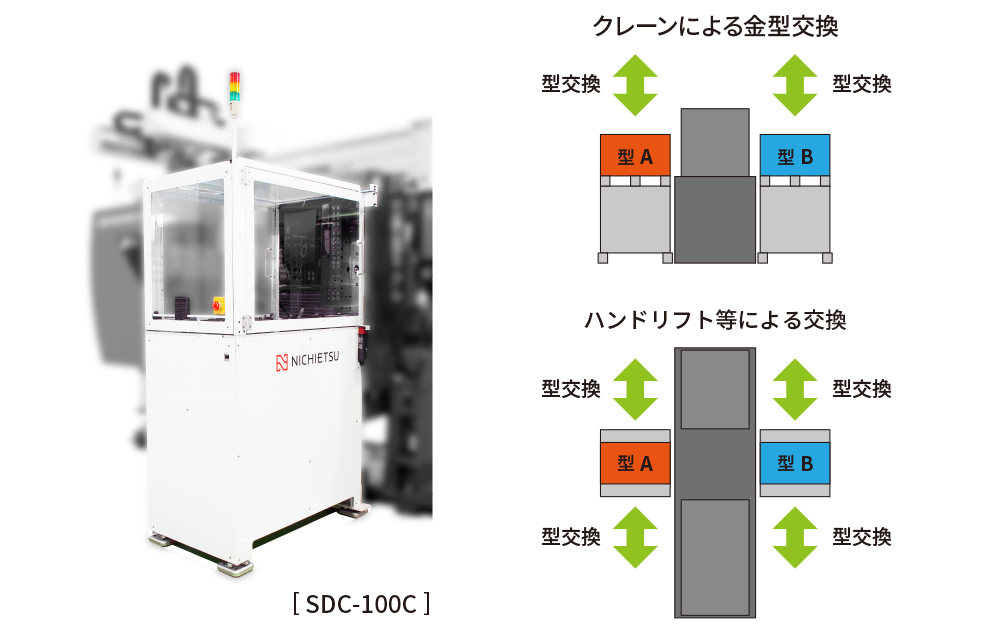
詳細はこちら ⇒ 金型交換装置 SDC
4. サイクルタイムの短縮
成形におけるサイクルタイムの各工程の時間の取り分を図に表してみますと、例えばこのような感じになるかと思います。
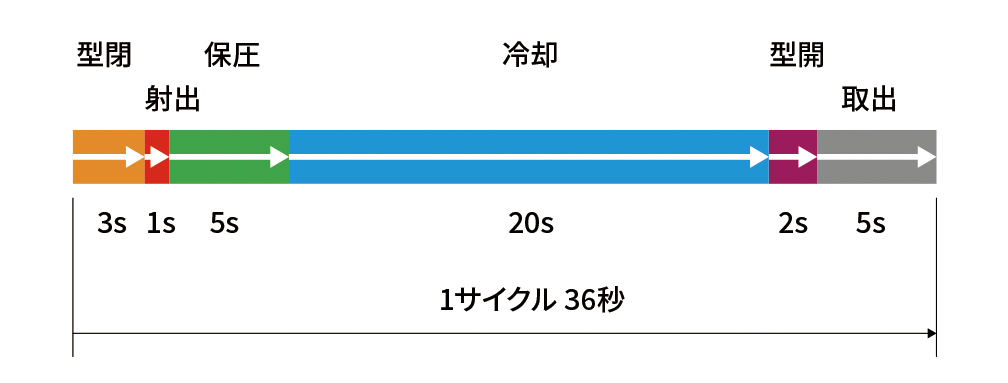
一番時間がかかっているこの冷却工程の時間を、如何に短くできるかがポイントとなるかと思います。その方法としては大きくは二つ、一つは冷却時間を短くしていった時の不具合の発生を抑える、もう一つは冷却効率そのものを上げる。マツイには、糸引きの、反りやヒケなどの不具合を抑えるアイテム、効率的な冷却には成形品の形状に合わせた水管の見直しや熱交換効率を維持するソリューションを揃えています。
それぞれ、具体的な手法・方法、ソリューションアイテムについては、12あるソリューションテーマ別のコラムにてご紹介いたします。
グローバルソリューション推進部 飯島 泰彦