成形工場のfactor4を目指して
段取時間の短縮は効率UPのカギ
2022.12.19
射出成形における段取時間とは?
射出成形における段取時間とは、
- 材料を乾燥させる
- 金型を成形機にセットする
- 金型の温度を上げる
- 成形の条件出しをする
といった、生産準備のための時間のことを指します。
プラスチック成形では、材料替えや金型交換の間は成形機が止まっており、生産が停止している状態です。近年は多品種少量生産が進んでおり、多様な製品に対応するために、このような段取時間はさらに増加傾向にあります。
こうした「段取時間(だんどりじかん)」と呼ばれる一連の作業は、効率よく行わなければ生産上のロスにつながります。ロスする時間を極力減らし、リードタイムを短縮するためにも、成形工場における段取時間の短縮は避けることのできない課題となっています。
特に、段取時間の多くを占める工程としては「材料替え」と「金型交換」があげられます。
材料替え
成形中に材料の色を替える、材料を変更するという作業は普段よく起こり得ることかと思います。何色も色替えがある成形品では、段取時間のほうが成形時間より長い場合もあります。また、金型費用を抑えるために、切り替えピンなどをつけて一つの金型で様々なパーツを成形するといった事例も珍しくありません。
材料を変えた際は、少しでも早く切り替えて次の成形を開始したいところですが、材料が適切な乾燥状態になっていなければ成形することはできません。樹脂材料の乾燥は時間がかかるため、事前にしっかりスケジュールを立てて準備しておく必要があります。
さらに、材料替え時にはホース内や供給ラインに残った材料を廃棄し、清掃する手間もあります。スムーズに行わなければ成形機を停止している時間が長くなり、効率悪化の要因となります。
金型交換
多品種少量生産が増えたことで、成形工場における金型交換の手間は増加傾向にあります。金型の付け替えはクレーンなどを使用しなければならず、時間も手間もかかる上に危険も伴う作業です。
成形後の金型は高温になっているため、付け替え作業をするには冷めるまで待たなければなりません。また、金型を付け替えた後も、金型温度が上がらないと成形を開始できないので、温まるまで待機する時間も必要となります。
また、少人数で稼働している成形工場も多く、夜間は特に作業員が少なくなります。複数の金型交換のタイミングが被ってしまうと、交換待ちが発生し、成形機の停止時間が伸びてしまいます。
このように、金型交換はどうしても段取時間が長くなってしまう工程です。
段取時間を短縮することのメリットとは
段取時間を短縮し、成形機の稼働時間が増えれば、その分多く生産することができます。
段取待ちで成形機が止まっている間にも、待機用の電力は使用している状態のため、待機時間を減らす事は、その分のロスを削減することにもつながります。
成形工場において段取時間を短縮することは、生産性を高め、コストを下げる、つまり売上を上げることに直結します。工場の効率を上げるために大切なことなのです。
ただ、段取時間を含めた成形機全体のスケジュールを手作業で綿密に組むことは難しく、手間のかかる作業です。成形機がトラブルで止まってしまうことも少なくなく、その都度スケジュールを組みなおすことは現実的ではありません。
段取時間を短縮するソリューションを紹介
それでは段取時間短縮のためにはどのような方法があるのでしょうか。
それぞれの行程別に、課題を解決するソリューションを紹介します。
材料替えを効率的に
乾燥機を追加して、樹脂を予備乾燥状態で待機させておくことができれば、樹脂の乾燥待ちという段取時間を削減できます。
また、清掃性の良い機器を使用することによって、作業効率を上げることが可能です。
ホース、シリンダー、ホッパーに残った樹脂を全て抜き取り清掃していると、それだけで時間がかかってしまいます。
そこで解決策として挙げられるのが、吸引式捕集器とプッシュダンパーの組み合わせです。必要最小限の樹脂をバッチ処理で成形機へ送り切ることで廃棄する樹脂量を減らし、材料・色替えの際の段取時間を短縮します。
材料の自動切替え
一台の成形機で複数の材料を切り替えて成形する際や、同じ材料を複数の成形機で使用するような場合、送り込む材料を自動で切り替えることができれば、大幅に手間と時間を削減できます。
そこで活躍するのがユニバーサルヘッダーです。予備乾燥機を複数台準備し、ユニバーサルヘッダーと成形機をつなげば、後は集中コントローラーからの操作で簡単に材料の切り替えが可能となります。乾燥機を動かしたり、中の樹脂を入れ替えたりする手間がありません。原料ホースや空気用ホースの入れ替えも必要なく、乾燥機の稼働状況を把握することもできます。このように作業が効率化されることで、段取時間の短縮が期待できます。 ⇒ CU ⇒ UH
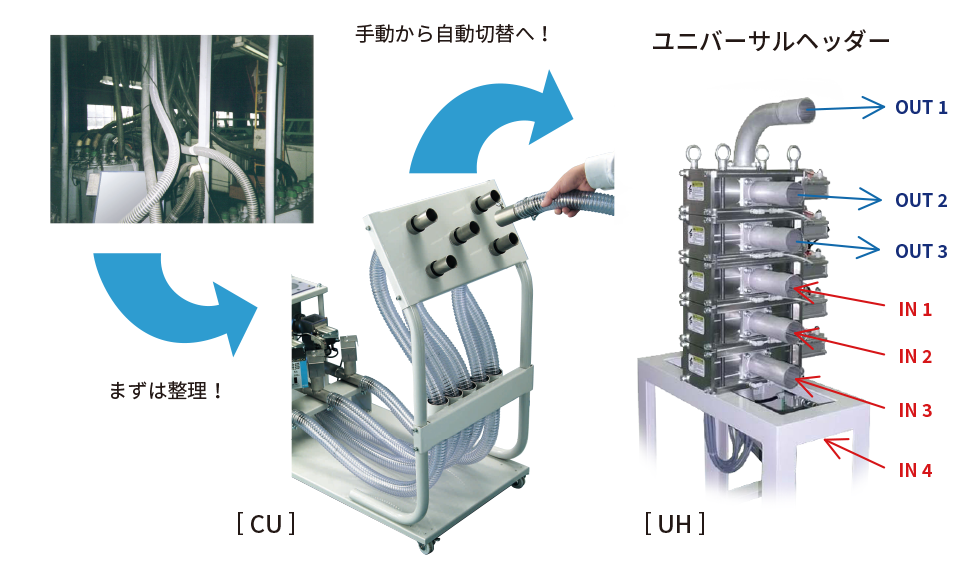
シンプルな構造のため材料の滞留もなく、各現場に合わせて自由に構成できる点が特長の一つです。
金型交換にかかる手間と時間を減らす
通常の段取り作業では、予備温調をしていても、成形機に取り付ける際には一度全ての配管を外してクレーンで成形機に取り付ける必要があり、二度手間になってしまいます。この問題を解決するソリューションを紹介します。
金型の交換を素早く安全に
成形機を止めて金型の交換をする通常の段取りを「内段取り」と言います。
一方で、成形機を止めずに、事前に金型交換の段取りを行っておくことを「外段取り」と言います。次の成形で使う金型の事前準備を「外段取り」化することによって、金型の交換を素早く安全に行うことが可能となります。
外段取りでは、生産中に、金型交換装置にあらかじめ次に使用する金型をセットしておき、配管を接続して予備温調を行った状態でスタンバイさせておきます。前の生産が終われば、配管を接続したまま、昇温された状態で金型を交換できるのです。
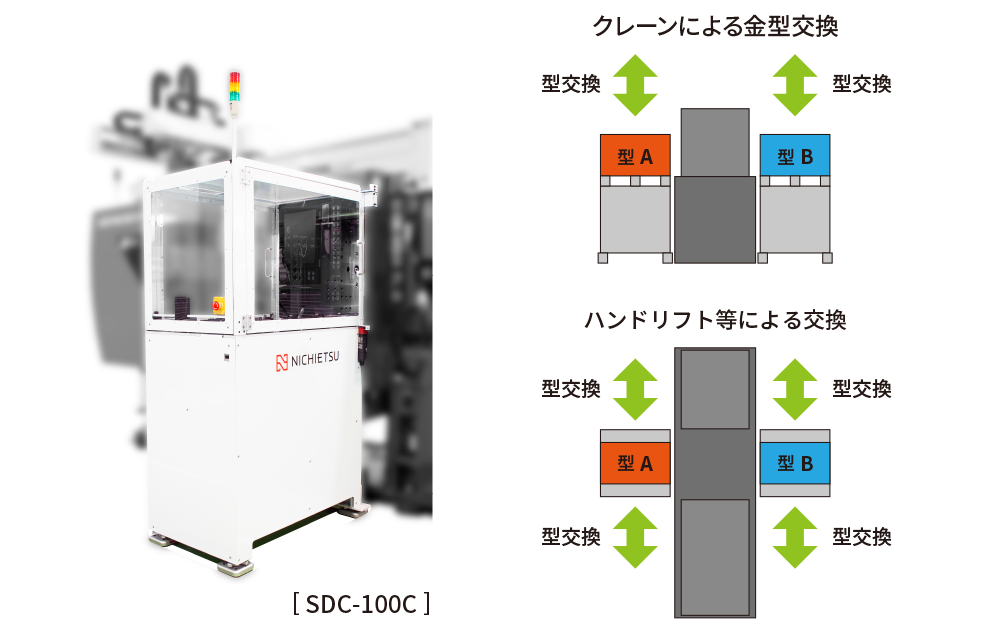
位置決めも精密で、交換後は速やかに生産を開始することが可能です。そのため、金型交換の段取時間を大幅に短縮できます。
手の空いた時間に、クレーンを使用した金型の移動や設置、配管を事前に済ませておけば、金型の段取り待ちも解消できます。焦って作業をする必要がないので、作業員の安全性も向上します。
既設の成形機に取り付けることができ、設置面積は世界最小クラスのため、大がかりな改修や、設備の入れ替えが必要ありません。
詳細はこちら ⇒ 金型交換装置 SDC
金型メンテナンスの時間を減らす
成形品にガス成分が付着してしまった際には、金型の洗浄が必要です。こういったメンテナンス作業の際にも、成形機を止めなくてはならず、大きな時間のロスになります。
特に中重度のガスになると、金型を一度成形機から下ろして洗浄しなくてはならず、金型の付け替え、洗浄などの段取りが必要となります。こうした際にドライアイスブラストを使用すれば、金型を成形機に取り付けたまま金型の洗浄が可能となり、脱着に必要だった手間と時間を減らせ、作業員の安全性も確保できます。
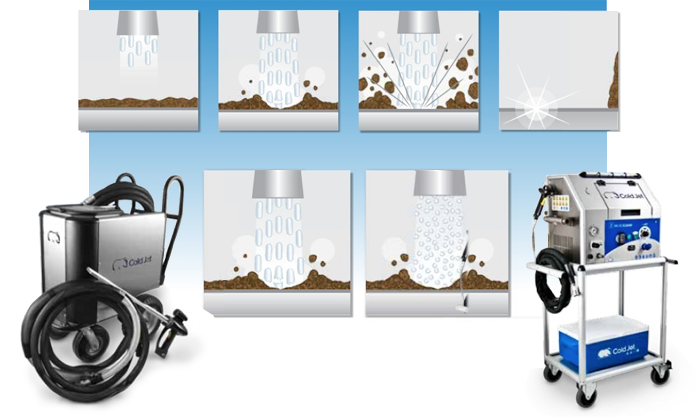
ドライアイスは二酸化炭素そのもので、噴射するとすぐに気化するため、廃棄物は発生しません。洗浄後は速やかに成形を再開でき、作業効率も非常に良くなります。溶剤や研磨剤を使用しないので、人体や環境にやさしい点もメリットの一つです。
まとめ
成形機をなるべく止めずに稼働させることが、成形工場の生産性を上げる一番の近道です。
ムダな時間をなくし、生産量を増加させることで売上げが上がり、短納期化を達成することで工場の評価も向上します。さらに、段取りの手間を減らし、作業を効率的にすることで少人数稼働が可能となり、業務の安全性向上にも貢献します。
松井製作所では、成形工場の生産性を高めるためのさまざまなソリューションを提案しています。ぜひお気軽にご相談ください。
CX デザイン部 飯島 泰彦