成形工場のfactor4を目指して
成形時の異物(コンタミ)対策を工程別にご提案
2022.10.20
コンタミネーション(汚染)とは、プラスチック成形業界においては成形品に異物やごみが付着、混入することを指し、現場では「コンタミ」と略して言われる事が多いようです。
成形品への異物混入 = コンタミはクレームにつながりやすく、製品の再検品が必要となったり、場合によっては返品となったりと、大きな損害をもたらします。また、コンタミの発生した成形品は粉砕して再利用することも難しく、材料の廃棄にもつながります。
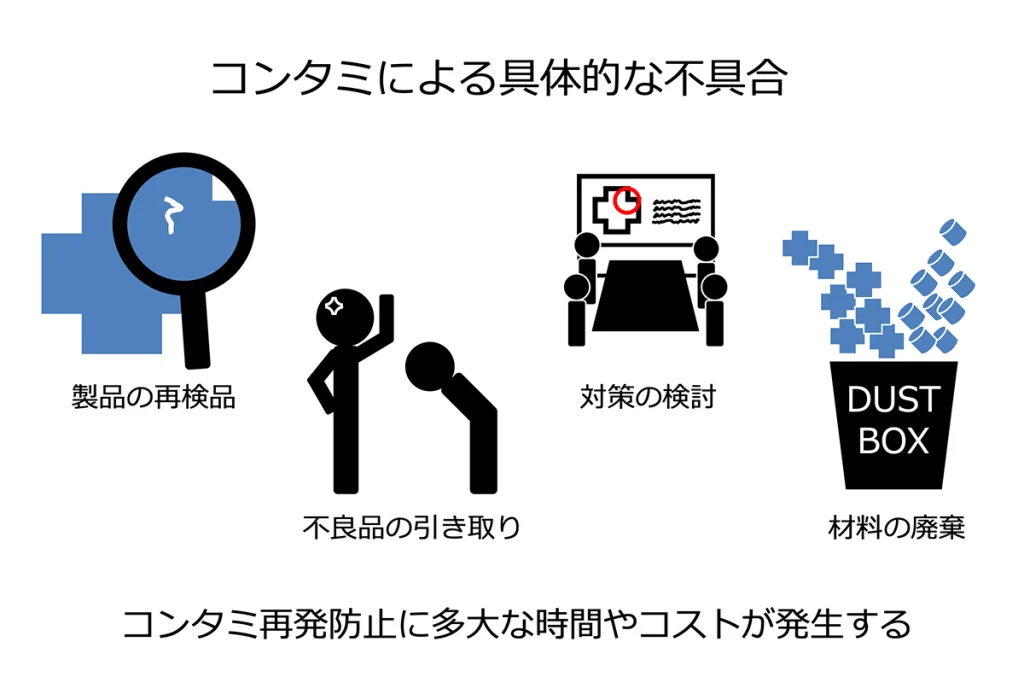
一度コンタミが発生してしまうと、良品が生産できる状態に戻すためには多くの時間とコストがかかりますし、成形不良が多くなれば、成形工場としての信頼を損なうことにもつながってしまいますので、コンタミは未然に防ぐことが重要です。
このコラムでは、以下の目次の内容で、成形の各工程でのコンタミ対策をご紹介いたします。
1. 従来のコンタミ対策
2. コンタミの基準
3. 行程別ソリューションのご紹介
- 材料受け入れ行程
- 材料輸送行程
- 材料乾燥行程
- 成形行程
まとめ
1. 従来のコンタミ対策
コンタミ対策として、よく挙げられる対策の一つは「クリーンルーム」の設置です。
しかしクリーンルームの設置・維持には大きなコストがかかります。例えば、100~200トンの成形機4台向けのクリーンルームでは、およそ4000万円程度かかるという試算があります。クリーンルームを適切に維持するためには費用だけではなく、多くの手間も発生します。
そもそも、大がかりなクリーンルームを設置する必要があるのでしょうか?
クリーンルームを設置すれば、異物の混入をすべて防げるわけではありません。コンタミの原因がクリーンルームの外にある場合も多々あります。重要なのは、「適正な対策」を「適正な場所」に実施することです。
2. コンタミの基準
前提として、全ての成形品には異物が混入、または付着していると言えるでしょう。コンタミを完璧に無くす事はとても難しい事です。そこで重要となってくるのが「コンタミ判定となる基準」です。異物の種類や大きさ(小ささ)、混入(付着)の度合いによって、問題とはならない場合があります。つまり、成形品毎の「コンタミ判定となる基準」を理解し、要求されるレベルに合った対策を施す事が重要なのです。
コンタミの種類
では、一体どのようなものが異物として成形品に混入するのでしょうか。
これらは実際に発生したコンタミを顕微鏡で拡大した写真です。
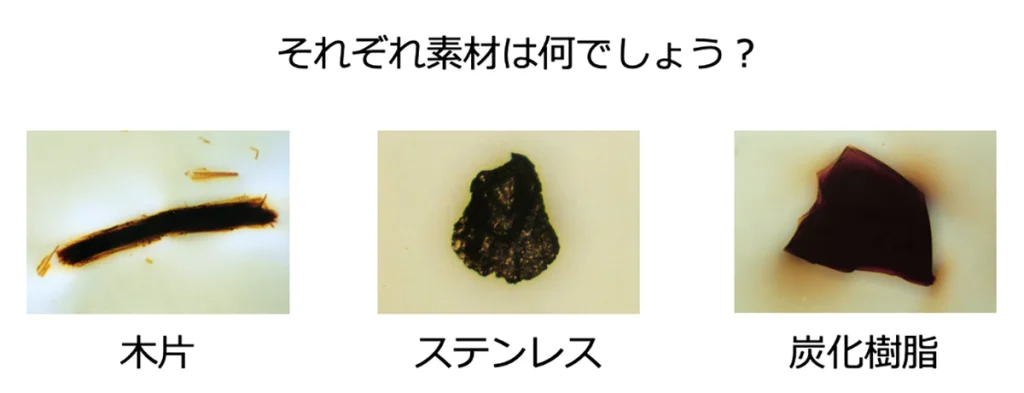
一見するとすべて同じ黒点のように見えますが、実は木片やステンレス、樹脂とそれぞれ素材が異なります。このように異物の材質はさまざまなため、木片であれば現場内で使用している木製パレットをプラスチック製に変更する、金属片であれば金属探知機を使用する… と、それぞれに対応する混入防止対策を施さなければなりません。
また、業界によって混入してはいけない異物の種類が異なります。一例ですが、電子機器業界では繊維くずや金属片、医療機器業界では繊維くずや皮膚片などが挙げられます。製品に求める仕様がそれぞれで異なるため、問題となる異物の種類もまた異なってくるのです。
こうした背景から、コンタミの種類を知ることが対策方法を決める第一歩となることがわかります。
コンタミの大きさ
異物の大きさもまた、混入対策を検討する上での重要な要素の一つです。
サイズが小さければ、許容される場合もあります。肉眼で確認できなければ OK であれば、10μm のサイズが取り除けるフィルターを設置することで対策可能です。
※人の目に見える大きさは 10μm(0.01mm) からといわれます。
また、コンタミ対策したい金属粉は0.1mmだが、検討している金属検知器はどれも0.3mmまでしか
金属を除去できないというような場合があります。
こういった場合は「そもそも金属粉を発生させない」という対策に切り替える必要があります。
対策方法を決める上でも、異物の許容サイズの基準は確認しておかなくてはなりません。
また、異物の付着箇所が問題となる場合もあります。例えば液晶部や加飾を行う部位、意匠面などへの異物は NG でも、それ以外の場所であれば許容されるといった具合に、製品仕様や業界によって異物の基準は異なります。
これらの事から、異物の種類やサイズを把握し、「コンタミ判定となる基準」と照らし合わせ、異物の除去方法やレベルを決めて、対策を講じる事が大切です。
3. 行程別ソリューションのご紹介
自社にとって混入防止が必要な異物の種類やサイズをおさえた上で、次に考えるべきなのが「いかにして混入を防ぐか」という点です。どのようなコンタミ対策が可能なのか、生産ラインの工程順に具体例を挙げてご紹介いたします。
材料受け入れ工程
材料投入口はどうしても人が関わることが多いため、髪の毛や皮膚片、服の繊維などの異物が多く発生する場所です。床に落ちているごみや、材料袋などに付着しているごみが入りこんでしまう可能性もあります。材料投入の場面ではどのような対策が取れるでしょう。
原料移動の自動化による異物混入対策
フレキシブルコンテナバッグ(フレコン)を使用している成形工場も多いのではないでしょうか。フレコンは便利ですが、吊り下げてタンクに材料を投入する際、外側に付着したごみが混入してしまう可能性があります。
対策方法としてフレコンを拭く、エアブローをするなどが考えられますが、手作業での除去は作業員の大きな負担となりますし、危険性も伴います。エアブローで除去しても、ごみが舞い上がり、タンクに落ちてしまう可能性も考えられます。そこで、フレコンを吊り下げ、サクションヘッドを中に差し込む方式の自動化装置をご提案します。
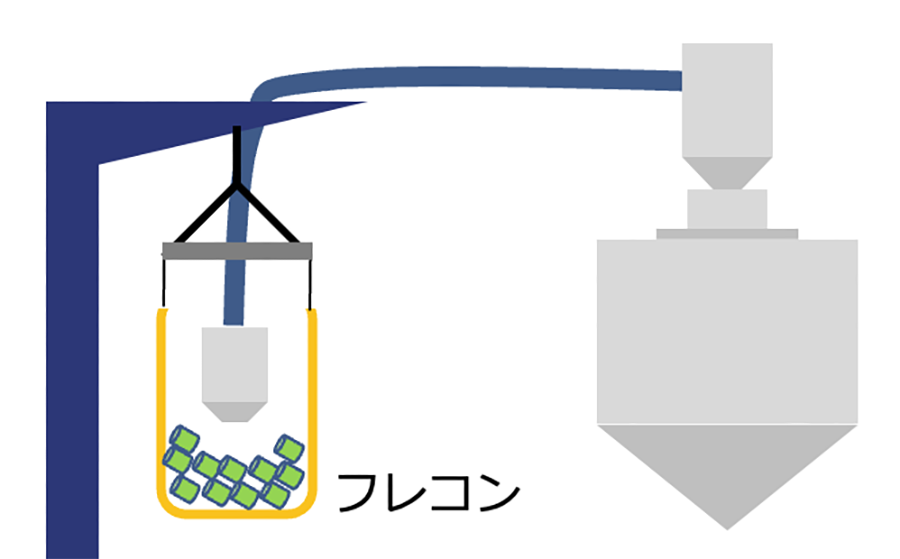
フレコン自体を持ち上げないので、側部や底を拭く必要がなくなります。上側に乗っているごみを除去するだけで済みますので、作業効率がアップし安全性も向上します。また、四隅を吊るすことで、材料を中心に寄せて輸送することができるため、材料残りも極わずかになります。
クリーンブース化による浮遊ゴミの混入対策
材料投入時に浮遊しているごみがタンクに混入してしまうことがあります。
そこで、生産ライン全体のクリーンルーム化は難しいという場合に、材料を投入する空間のみクリーン度を向上するというソリューションをご提案します。
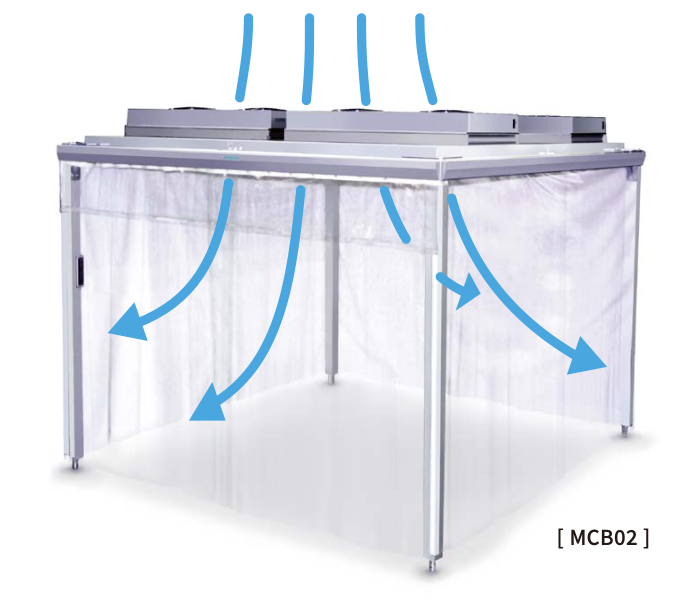
これはクリーン度を向上したい区画のみをクリーンブースとする方法です。
該当区画を囲み、天井にフィルターを設置してファンで上から下へ風を送ることで空間内を陽圧にし、ごみを外部に排出する空気の流れを作り出します。また、ブース内を除電にすることで、材料袋や作業員に付着したごみも排除することができます。用途に合わせ、清浄度を変えることも可能です。
生産工程への供給前の除粉対策
樹脂は運搬時や輸送時の揺れでペレット同士がこすれ、樹脂袋内で樹脂粉が発生してしまいます。こうしたケースには、材料供給前にペレットと粉を分離し、コンタミを抑制する方法があります。
材料袋とタンクの間に分離機を導入することにより、ペレットと樹脂粉を分離します。これによってクリーンなペレットを生産ラインに供給できます。
材料乾燥工程
黒点などのコンタミは、衛生面や外観基準の厳しい製品ではよく問題になります。この黒点の原因の一つとして、樹脂の炭化や焼けが挙げられます。
樹脂の炭化や焼けが発生する原因として、「樹脂の過乾燥」や「樹脂の冷え」が挙げられます。
樹脂は成形機のスクリューが回転することで、ペレット同士が引きちぎられる摩擦熱によって融解します。これをせん断発熱とよびます。
このとき、樹脂が乾燥しすぎていて内部に水分が残っていない状態となると、発生するせん断熱が高温になりすぎてしまう傾向にあります。これによって炭化や焼けが発生するのです。また樹脂は冷えると固くなるため、これも過剰な抵抗を生み、せん断熱が高くなってしまう原因となります。つまり、炭化や焼けによる黒点を防ぐためには樹脂の過乾燥や冷えを抑えることが有効なのです。
適正乾燥による樹脂の炭化、焼け(黒点)対策
成形機は生産計画や型替え、トラブルの対応などにより小停止を繰り返しますが、乾燥機は常に稼働し続けているということはありませんか。
また、型替えによって樹脂の使用量が少なくなると、乾燥ホッパー内に樹脂が長く滞留することにつながります。これによって、樹脂が過乾燥状態となり、炭化や焼けが発生しやすくなってしまうのです。
かといって、これらの小停止に合わせて乾燥機も停止すると、とても手間がかかります。起動し忘れてしまい、生産が止まってしまうリスクもあり、手動で全て管理することは現実的ではありません。
そこで効果的なのが、適正乾燥機能付きの乾燥機を導入することです。これにより生産に合わせた適正乾燥の自動化が可能となります。

乾燥機が、成形機の稼働状況に合わせ、自動的に熱負荷を軽減する事で、樹脂の適正な乾燥状態を維持します。過乾燥による透明成形品の黄変を防ぐ効果も期待でき、また適正稼働による省エネにもつながります。
詳細はこちら ⇒ セルフコントロール機能搭載 除湿熱風乾燥機 MJ6-i
材料輸送工程
ホースや配管などの材料輸送経路は、ホースの破損による混入や、ガラス繊維が配管を削ってしまうことで起こる金属コンタミ、穴が開いて異物が入り込んでしまうなどのリスクがあります。
今回は別の視点からの具体例をご紹介いたします。
配管接続部のヘルール配管化によるパッキン磨耗対策
光学系や医療系製品の生産ラインなどでは一般的にIDFヘルールという配管が利用されています。この配管は、組み付け方が悪いとパッキンが配管の中にはみ出してしまうことがあります。
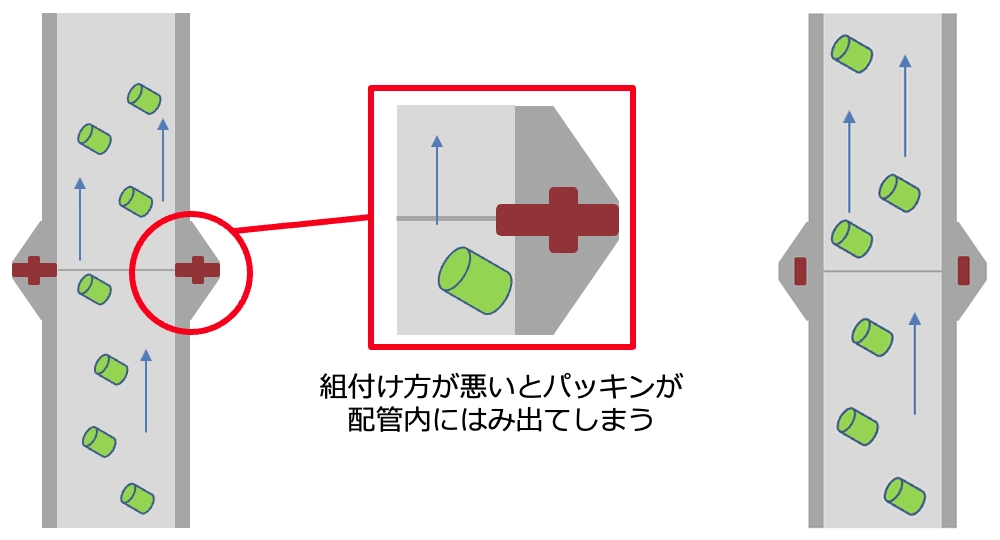
パッキンが配管内にはみ出していると、樹脂が当たってちぎれ、コンタミの原因になってしまいます。
これを防ぐためには、パッキンがはみ出ない構造のヘルールへ交換することが有効です。こうしたヘルールであれば組み付けのよしあしに左右されることはありません。
配管、輸送方法の見直しによる材料の滞留対策
輸送ホースの途中にできてしまったくびれや、配管の立ち上がり部分で、樹脂が滞留してしまっている事があります。これもまた、樹脂温度のバラつきを発生させ、炭化や焼けの原因となりえます。
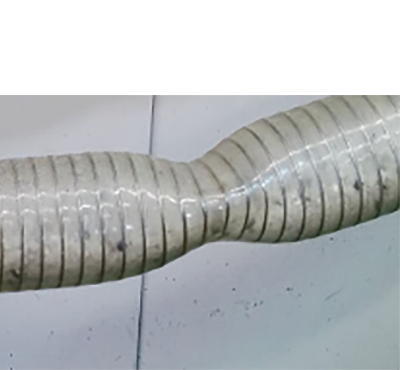
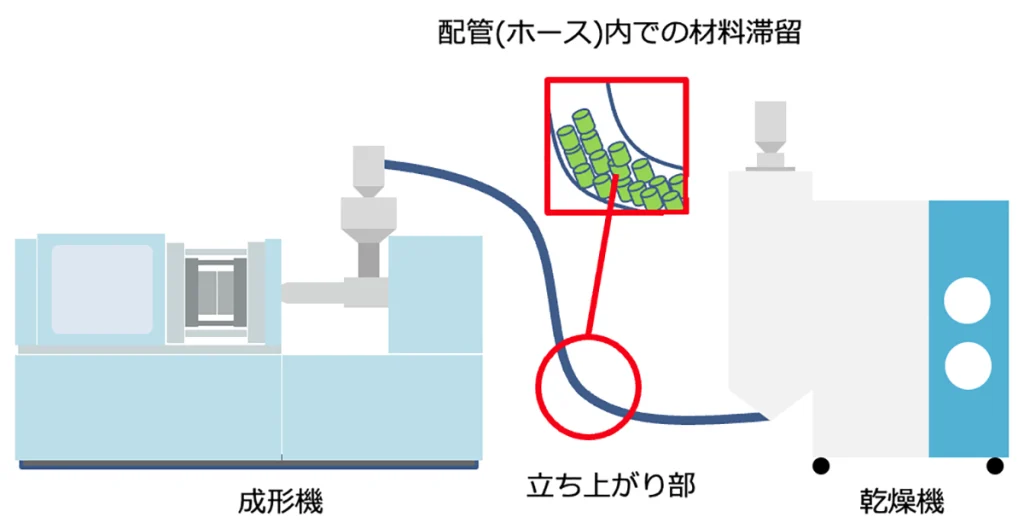
輸送経路での滞留を防ぐため、変形の無いホースを使う事は勿論ですが、配管の高低差や取り回しで滞留が発生しているような場合は、材料を送りきる機構を追加することで対策可能です。
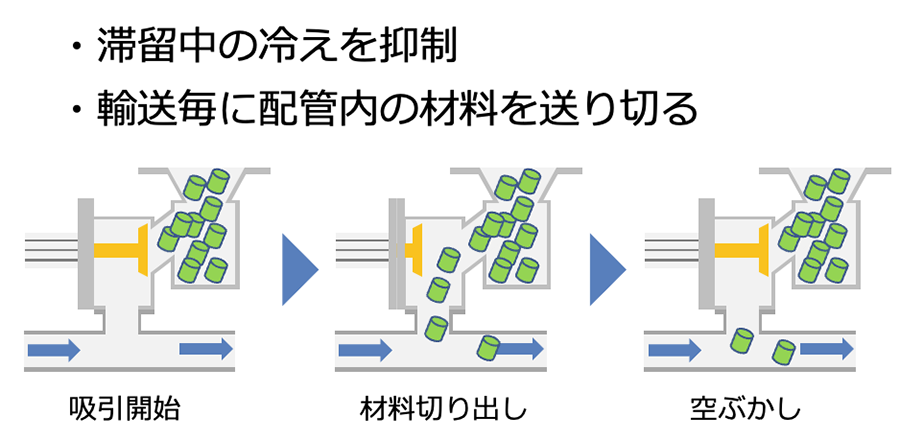
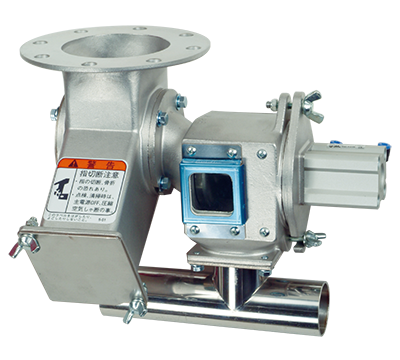
吸引がかかっている間に送り切れるだけの材料を配管に供給する事で、輸送経路内での滞留を無くします。また、スライドダンパーのような機構が無いため、ダンパー摺動による樹脂粉の発生もありません。
輸送時に発生する樹脂粉の除粉対策
樹脂粉は材料袋内だけでなく、配管内でも発生する可能性があります。
ペレットが配管内のベンド部などに衝突することで割れ、樹脂粉が発生してしまうのです。
これにはいくつかの対策方法があります。
樹脂粉がペレットに付着していない場合は、「遠心分離」が効果的です。 ⇒ ARV
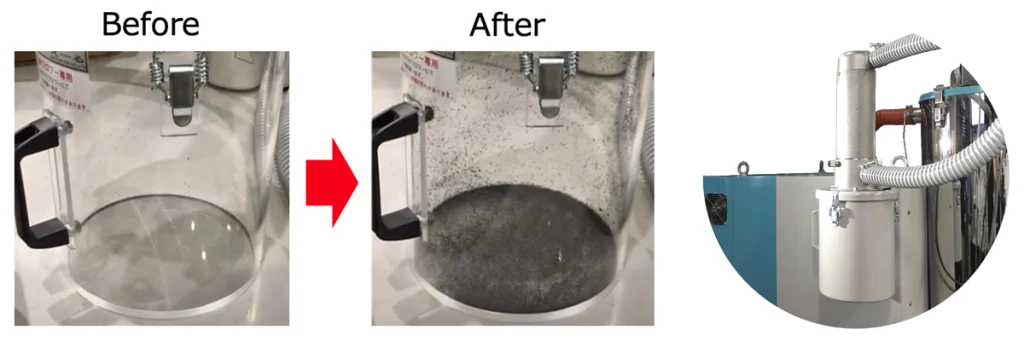
乾燥機などの輸送ラインに取り付けることで、配管内の樹脂粉を取り除くことができます。
樹脂粉がペレットに付着してしまっている場合は、「気流混合」という方法があります。
「気流混合捕集器」を取り付けることで、樹脂同士をぶつけてペレットから樹脂粉を剥離させます。樹脂粉は吸引によって取り除かれるため、クリーンなペレットを送ることができるのです。
詳細はこちら ⇒ 混合粉取捕集器 APH
また、「除電機能」によって樹脂粉を除去する方法もあります。
樹脂粉は静電気によってペレットに付着しているため、除電エアを吹き付けることでペレットから粉を剥離し、粉はエアの流れにのって廃棄チューブへ回収されるという仕組みです。
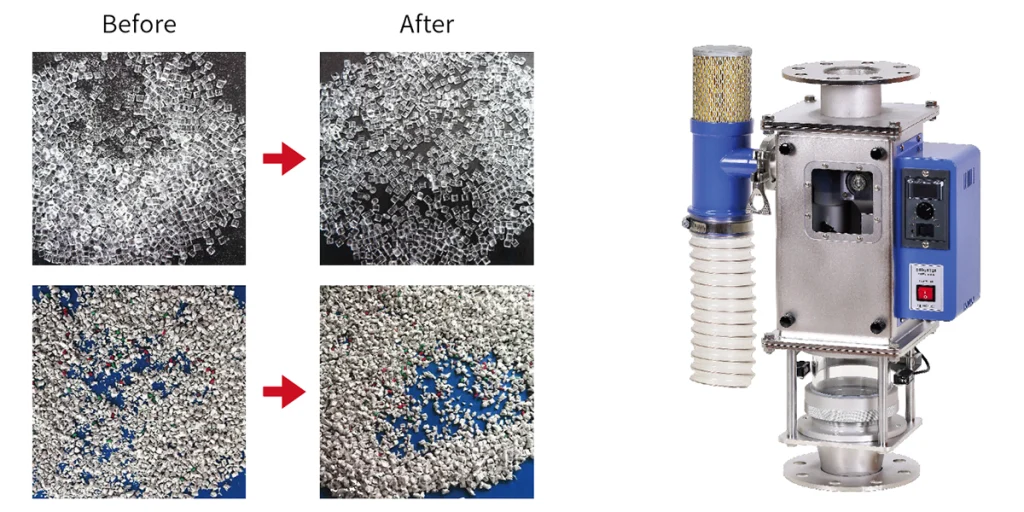
「気流混合捕集器」よりも処理量が多いため、樹脂の使用量によって使い分けることができます。
成形工程
材料に異物が混入しないよう留意しても、成形品に異物が付着してしまうことがあります。成形品の表面についた異物は、塗装するパーツなどは塗装不良となりますし、電子部品関連では通電の原因となってしまいます。
成形機周辺に浮遊しているごみが静電気によって製品に付着してしまうという問題には、どのような対策をすれば良いのでしょうか。
除電による成形品への浮遊粉塵着対策
一般的に考えられる静電気対策としては、イオナイザーによる除電ブローです。しかし除電エアがパーツに当たらなければ除電効果がありませんし、エアを吹き付けることで金型温度が下がってしまう恐れがあります。金型温度が下がることによって成形不良の原因となってしまう可能性があります
そこで、効果的なのが電気力線放射式です。電気力線を用いて型開き空間を集中的に除電するという方法です。
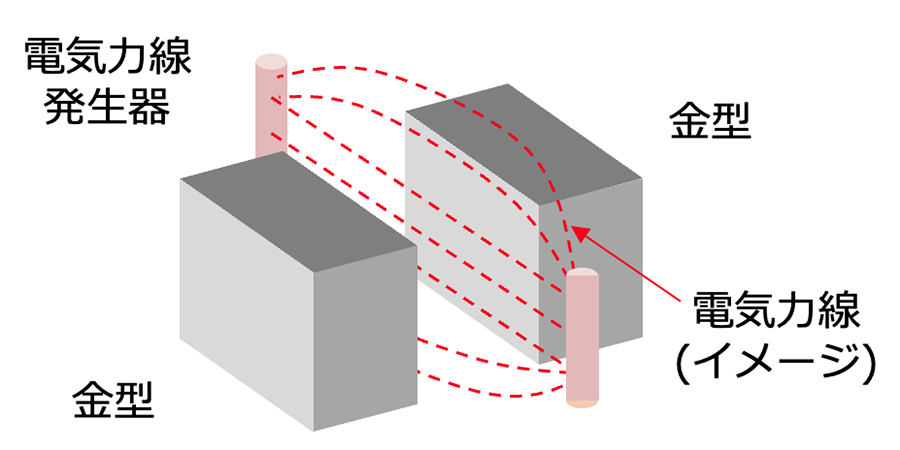
プラスの電極とマイナスの電極を金型の両サイドに取り付けることで、電気力線を形成して除電します。無風で対策可能なため、金型温度が下がるリスクはありません。
加湿(調湿)による帯電圧の低減
より広い空間全体を除電したいという場合には、加湿が有効です。
加湿することで帯電圧を下げると同時に、浮遊ごみを沈下させることができます。
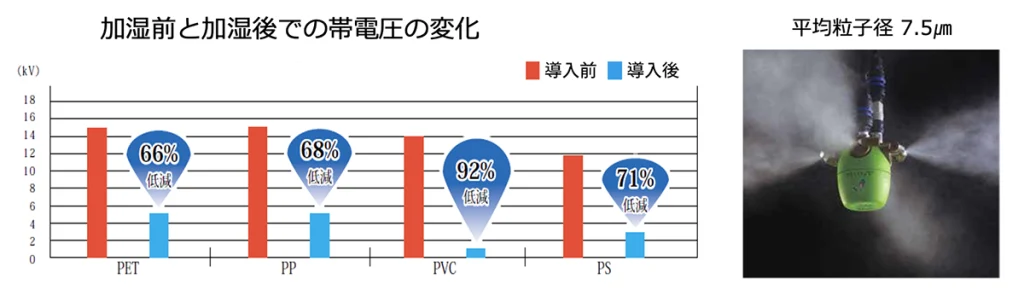
静電気対策には加湿が効果的ということは、よく知られているとは思いますが、機器が濡れることや金型の温度が下がる懸念がありますが、安定して微細な水滴を発生させることで、機器が濡れる事を防ぎながら、広範囲を除電することができます。
まとめ
成形品におけるコンタミの基準は、業界や製品毎に異なっており、またその発生原因も、成形環境により様々です。コンタミとなる基準を把握し、発生場所やその原因を特定した上で、適切な対策を施す事が大切です。
松井製作所では「豊かさ2倍、資源消費半分」というfactor4の考え方に基づき、成形工場の環境配慮、ひいては資源生産性向上のご提案を積極的に行ってまいります。お困りの方はお気軽にご相談ください。
営業技術部 八木 悠樹