成形工場のfactor4を目指して
プラスチック成形工場の環境対応【前編】CO2排出の削減
2022.06.27
- SDGs
- エネルギーのムダを無くす
- 脱炭素
省エネは時代の最先端
成形工場も環境対応が必要な時代に…
近年、SDGsやカーボンニュートラルといった言葉がよく聞かれるようになりました。政府の方針として、持続可能な開発や脱炭素社会が推進されています。この流れに伴い、企業にも責任ある行動が求められています。
中でも SDGs(Sustainable Development Goals)は持続可能な開発目標、つまり環境に配慮しつつ経済的な発展を成立させることを目標としていますが、その中で注目されているのが ESG 投資です。
ESG とは環境(Environment)・社会(Social)・ガバナンス(Governance)要素を考慮した投資のことを指し、すでに投資のトレンドとなりつつあります。すなわち、環境や社会に配慮することがそのまま企業評価や企業価値に直結しているのです。
こうしたテーマは、プラスチック業界においても例外ではありません。 近年プラスチック業界は多くの環境負荷問題に直面しています。例えば廃棄されたプラスチックごみが海洋に流れつくことによる景観破壊や環境汚染、海洋生物の生態系への悪影響が挙げられます。また、5ミリ以下の微細なマイクロプラスチックを飲み込んだこうした魚介類を口にした場合、我々人体への健康に影響を及ぼすのではないかと懸念されています。このような情勢をふまえると、成形工場においてもCO2の削減などの環境対応は必須となっていくでしょう。
そこで、今回は「プラスチック成形工場の環境対応」をテーマとし、成形工場が取り組める省エネ活動について、前編・後編の二部構成とし、当記事(前編)では「CO2削減」にフォーカスを当ててご紹介いたします。
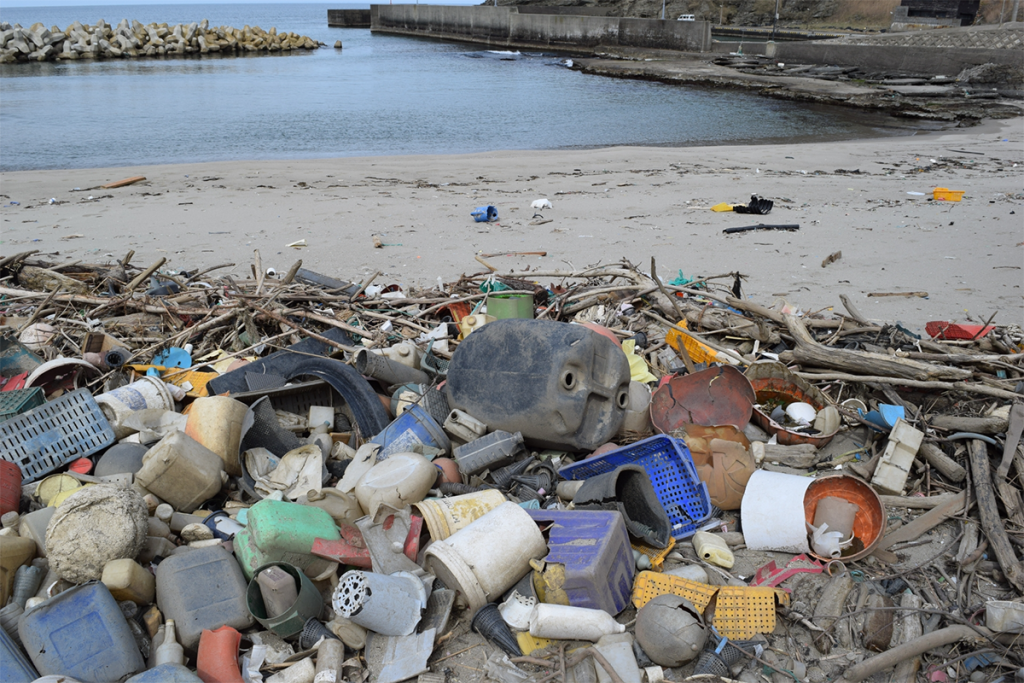
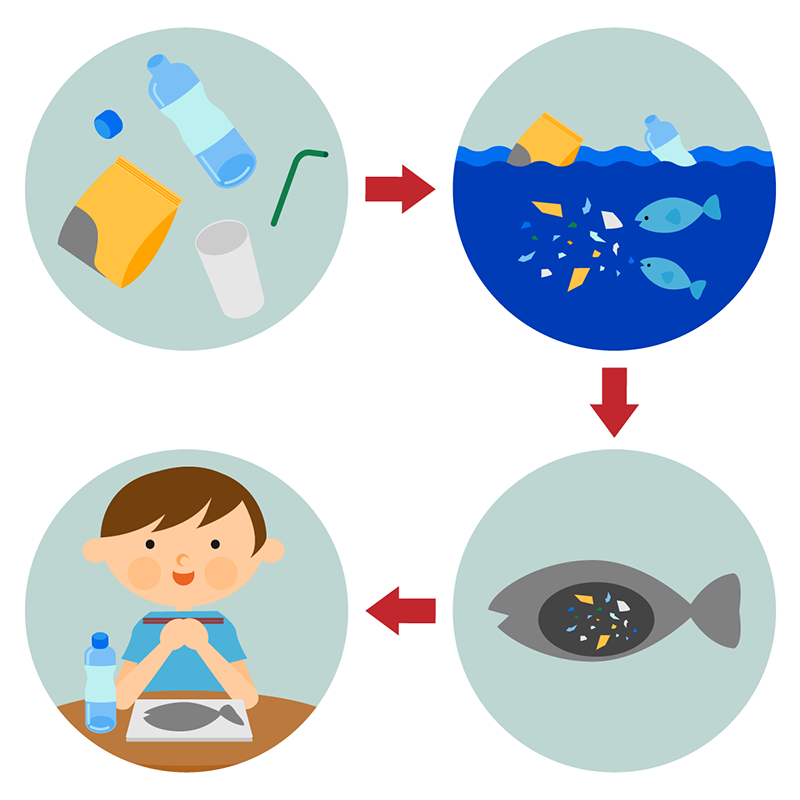
「ムダ」を「価値」にかえる
「環境や社会に配慮」というと、具体的に何をすればよいのか分かりにくいと感じるかもしれませんが、まずは目の前の「ムダ」なエネルギーをなくすことから始めてみるというのはいかがでしょうか。省エネは、自社の電力コスト削減というだけでなく、電気を作り出す工程でのCO2排出の低減を意味します。
では、成形工場にてムダに消費していたエネルギーを「価値」に変えるためにはどのようなソリューションがあるのでしょうか?
成形工場で一番のエネルギー大食らいは?
成形機が電気を食う、は間違い!?
「成形工場は成形機に大きな電力を使用しており、これを止めてしまうと仕事にならない。だから節電はできない。」と考えていませんか?
実は「成形機が一番電気を食う」という認識は、古いものになっているかもしれません。
確かに、従来の油圧式成形機は消費電力量が非常に大きいものでした。油圧式成形機は構造がシンプルで壊れにくく、パワーもあるため、特に大型の成形品には油圧式を使用されている成形工場が多いかと思います。しかし、小物や精密成形品の用途には電動式成形機を採用している工場が増えているのではないでしょうか。
電動式成形機は油圧式成形機と比較して消費電力量が40~50%程度と大幅に少なく、従来よりも圧倒的に消費量が抑えられています。
こうした状況下でポイントとなるのが「周辺機器」の存在です。
消費エネルギーの割合
成形工場で電気を消費する設備は成形機だけではありません。乾燥機、温度調節機、輸送機、そして空調など、大きな電力を必要とする周辺機器が多数使用されています。
ここで、成形工場で使用されるエネルギーの割合を見てみましょう。
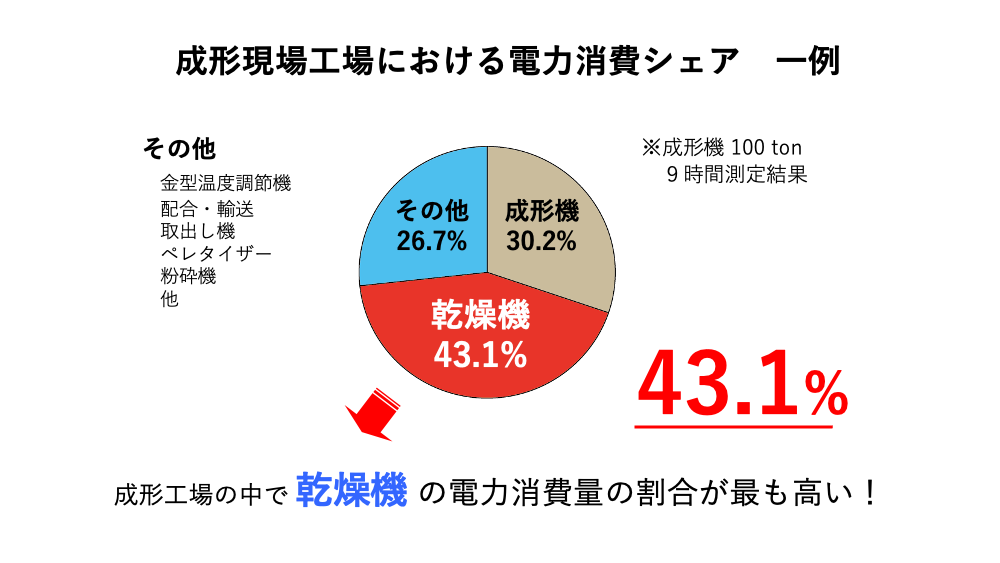
このグラフは、実際に 100ton の電動式成形機を使用して成形し、各々の機器の電力消費量を計測した比率を示しています。グラフが示す通り、電力消費量の割合が最も高いのは、実は成形機ではなく、乾燥機だったのです。
ムダがムダを生む
こうした多様な電力消費がある中で、「ムダ」なエネルギーとはどういうものでしょうか。
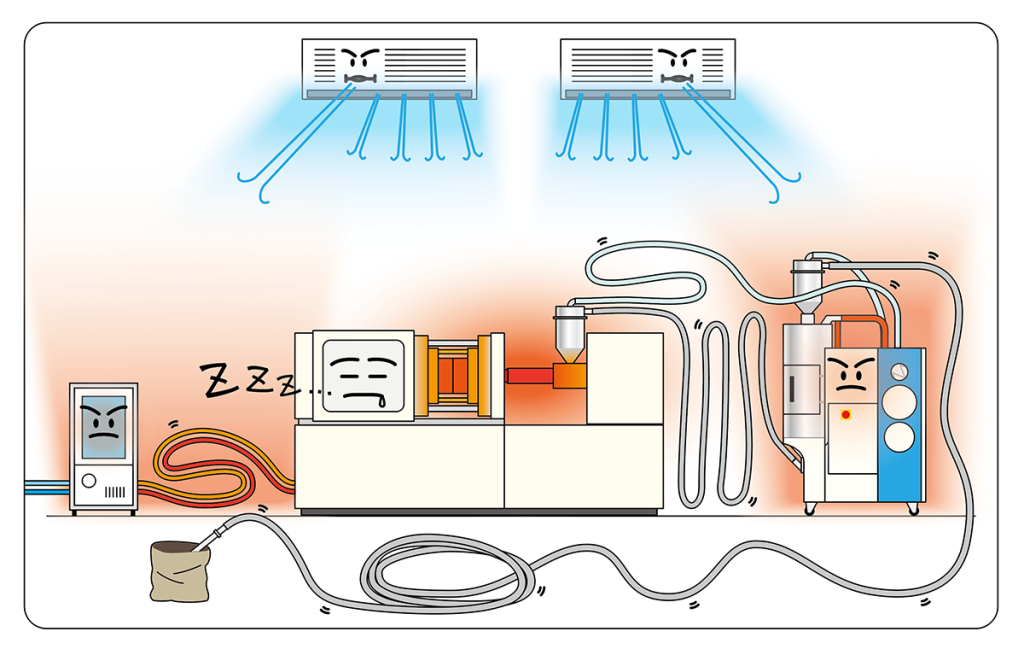
例えば、成形機が動いていない時にも、金型温度調節機や乾燥機などの周辺機器は稼働しており、放熱を続けています。その一方で、現場が暑くなりすぎないようにエアコンを常に稼働させているという事はありませんか?
電気を使って熱を発生させ、電気を使って冷やしている。ある意味で「ムダ」が「ムダ」を生んでいる状況です。
このようなムダなエネルギーを減らすためには、各機器への対策が必要です。
今回は、乾燥機、チラー、成形機の3つに絞ってご紹介します。
エネルギー効率改善の方法
乾燥機
前項にて、テスト環境での実測の結果、成形で最もエネルギーを使用しているのは乾燥機だったというデータを示しました。つまり、省エネに最も効果的なのは、乾燥機の消費電力を抑えることとなりそうです。
iplas除湿熱風乾燥機
セルフコントロール機能を搭載した除湿熱風乾燥機では、樹脂の乾燥状態を監視して乾燥風量・再生風量をコントロールし、最適な乾燥状態を維持します。さらに樹脂量や成形機の稼働状況に合わせて必要最小限のエネルギーで稼働するため「除湿熱風乾燥機 MJ6-i」では大幅な省エネルギー化を実現しました。
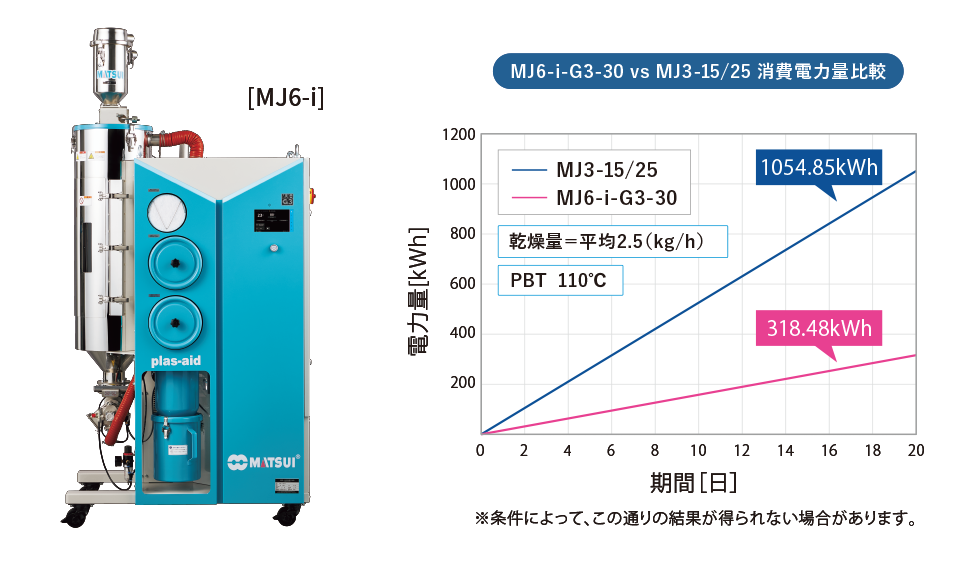
また、既存の設備に取り付け可能なオプションもあります。
バルブ式乾燥適性化システム
バルブ式乾燥適正化システムを既存の除湿乾燥機(MJ3)に追加する事で、乾燥ホッパーの温度をセンサーが監視し、風量をコントロールできるようになるため、ヒーターが使用する電力を必要最小限に抑えることができます。
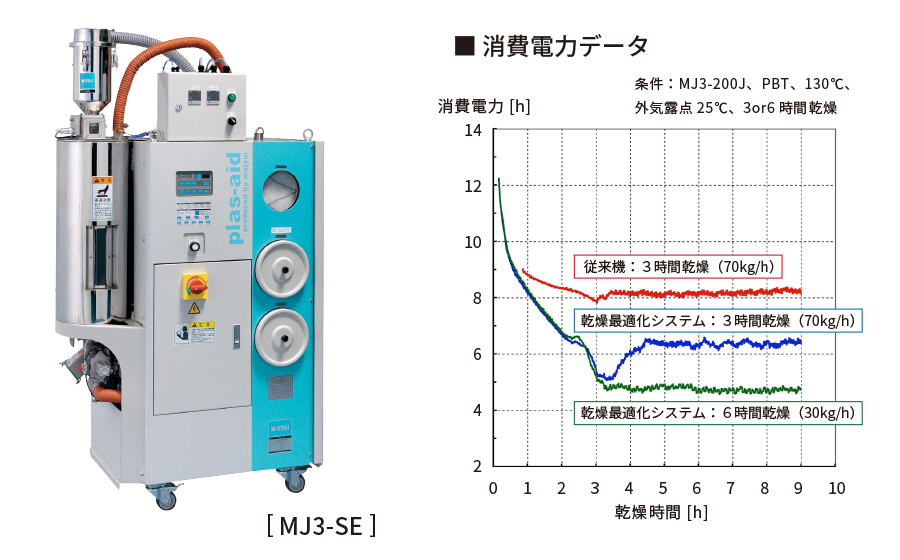
排熱回収ユニット
排熱回収ユニットは、既存の熱風式乾燥機(HD2)に取り付けて、排熱を再利用する事で、本体の電気使用量が最大 33% も省エネ可能です。また結果的に、作業環境への排熱の軽減につながります。
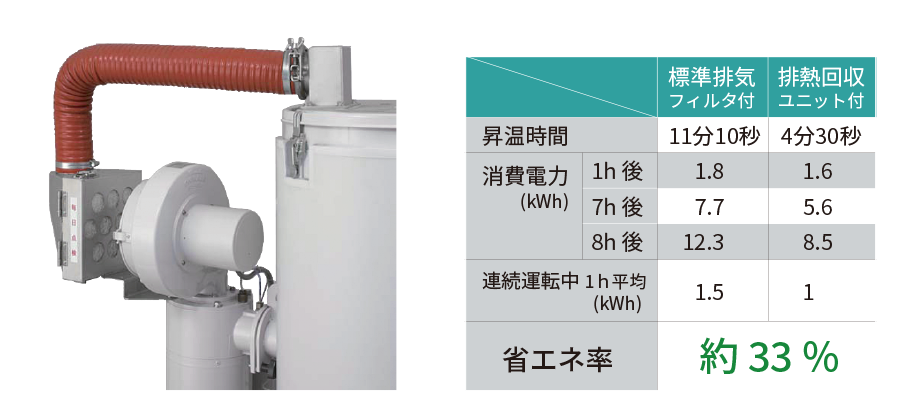
これらのソリューションは比較的低コストで、かつ省エネ効果を実感しやすいというメリットがあります。
ホッパー断熱カバー
ホッパーに断熱カバーを巻くことで、放熱を防ぎ、ホッパーまわりの温度を10度以上下げることができます。これによって温度が安定し、エネルギーの節約にもなりますし、作業員の安全性も向上します。
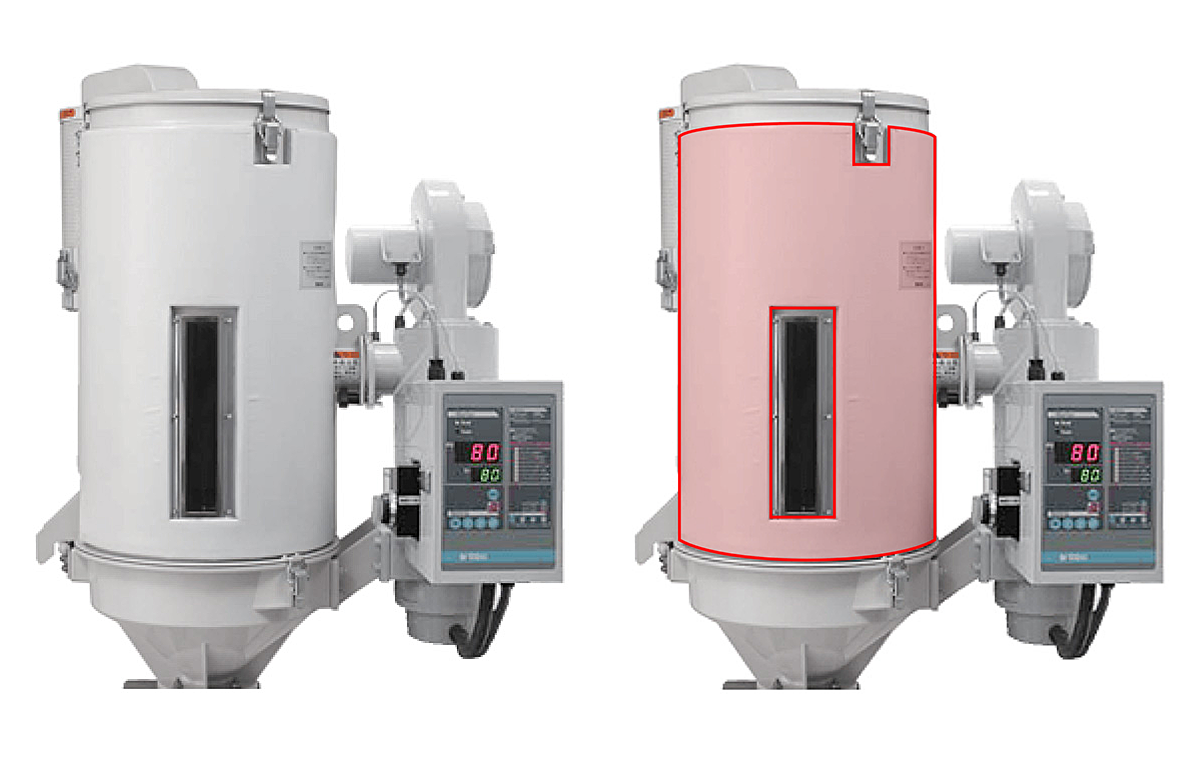
ここまでの乾燥機に関連した省エネのソリューションは、いずれも装置が省エネ化されるだけでなく、作業環境への放熱を抑えられるようになる事から、空調負荷が軽減され、エアコンで使用している電気消費量も減らせるため、「ムダ」が「ムダ」を生んでいるという状況を改善する事につながります。
チラー
フリークーリングシステム
フリークーリングシステムは、外気温を利用することで省エネを実現するソリューションです。冬など外気温が低い時期にチラーをストップし、クーリングタワーからの水を直接冷却水として利用します。通常の連続運転のチラーと比較して最大54%の電力を節約することができます。
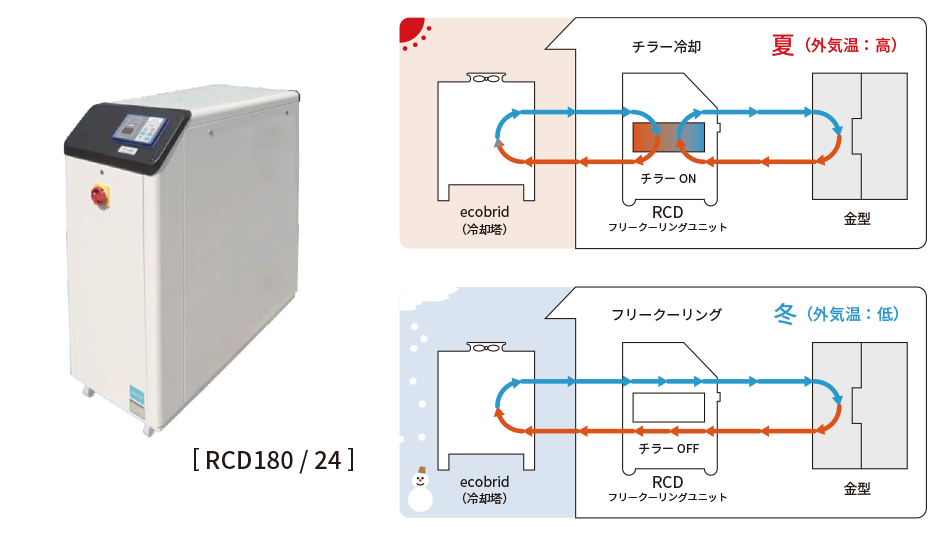
水冷式金型冷却機
弊社のセルフコントロール機能を搭載したチラーでは、熱負荷状況に合わせて稼働をインバータ制御することによって、大幅な省エネが可能となります。
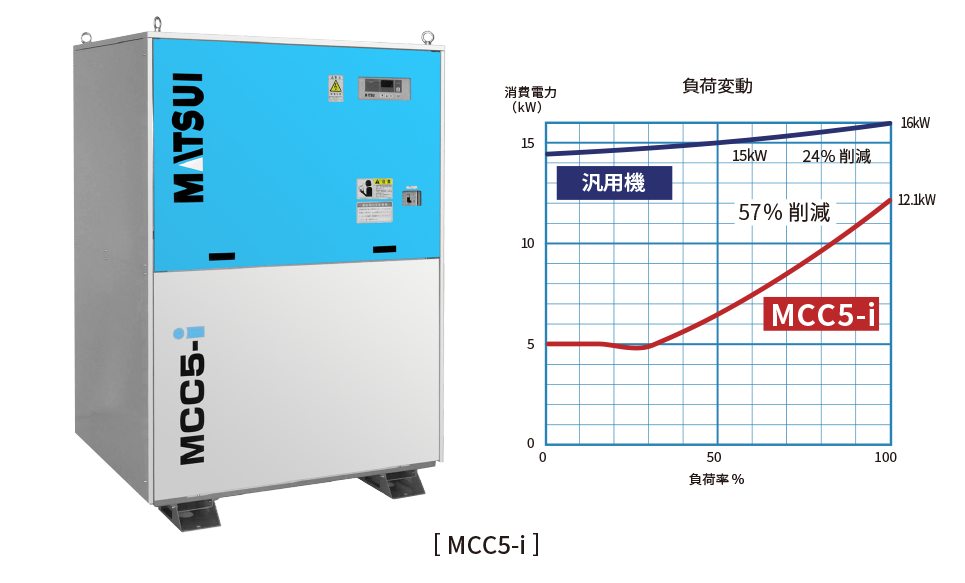
詳細はこちら ⇒ 水冷式金型冷却機 インバータ制御 MCC5-i
成形機
成形機本体は、稼働部分に手を加えてエネルギーの消費量を減らす事は難しい設備です。しかし、成形時に加熱筒(シリンダー)や金型から発生する、放熱、伝熱を抑制する事で昇温に必要となるエネルギーを抑える事が可能です。
シリンダー保温カバー
加熱筒(シリンダー)に保温カバーを巻く事で、放熱が抑えられ、ヒーターの加熱効率も上がりますので、省エネと作業環境への負荷軽減を同時に実現し、作業員のやけど防止にも繋がります。配線は必要ですが、巻くだけで装着できるお手軽さも魅了です。
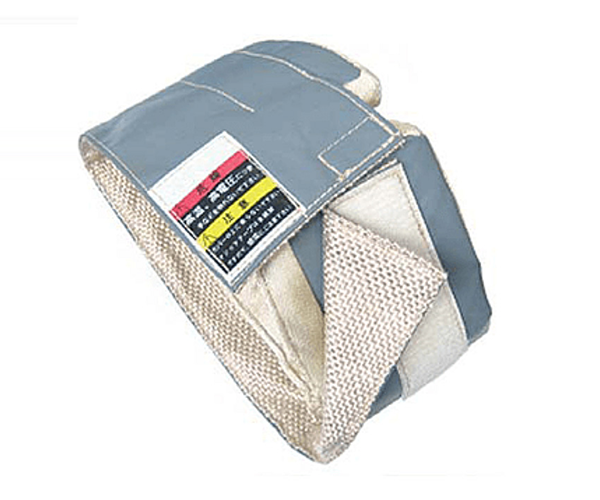
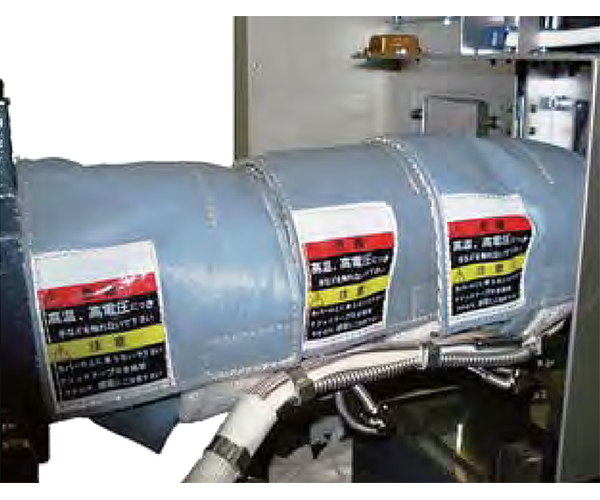
金型断熱板
金型は温度調節機で温調されていますが、そのままですと、同じ金属同士で、取り付け部位から熱が逃げていってしまいます。この金型と取り付け板(プラテン)の間に、断熱板を挟む事により、不要な伝熱を抑える事で、温調負荷を低減、省エネ化を実現します。また、金型の温度分布が一定になるので、安定成形が実現でき、成形品の寸法精度や外観品質の向上にも繋がります。
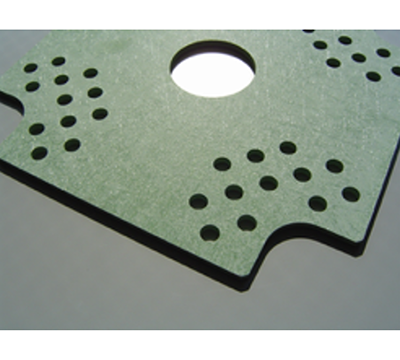
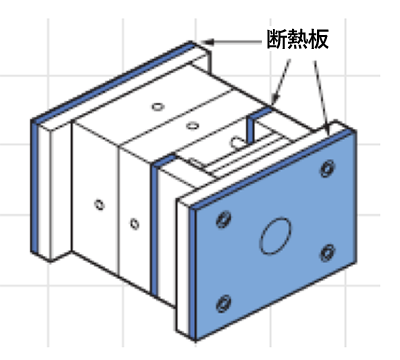
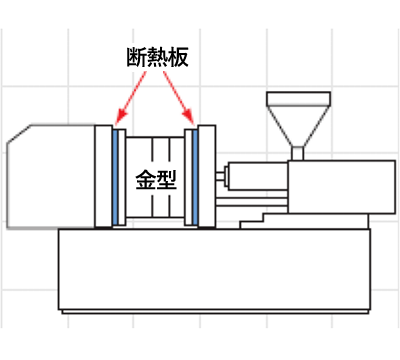
ここまででご紹介したソリューションの他にも、様々な手法・方法、アイテムを取り揃えていますので、お客様の工場設備やご予算、取り組みに合わせ、省エネでしかも快適な成形工場の実現を、共に目指します。
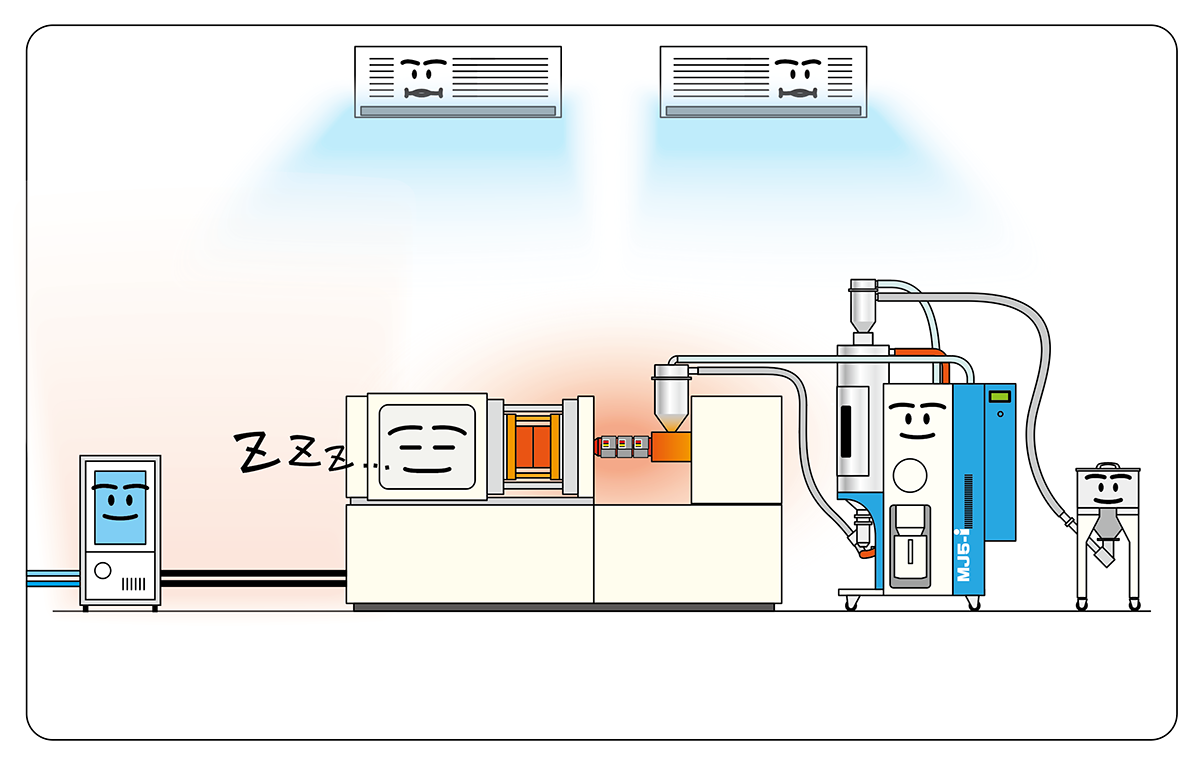
まとめ
CO2削減やサステナビリティなどというと、どこか遠い世界の話のように捉えがちですが、工場内のムダなエネルギーを削減することから始めると、身近に感じられるのではないでしょうか。
工場内の省エネは、まずは整理整頓や、使用していない機器の電源を落とすといった手軽なところから始めることができますし、新しいソリューションを導入することでより高い効果が期待できます。電気料金が高騰している今は、まさに投資の好機と言えるでしょう。
電気料金を節約することがそのままCO2を削減することにもなり、さらにそれが企業価値を高めることにつながります。松井製作所では、消費資源を削減し、企業価値を高めるソリューションを提案します。環境対応や、省エネに関してお困りの方はお気軽にご相談ください。
CX デザイン部 飯島 泰彦