Aiming for factor4 of molding factories
Environmentally friendly plastics factories - The first part
2022.06.27
- SDGs
- Eliminate wasted energy
- Decarbonization
The energy saving is the state-of-the-art of our time
Molding factories also need to be environmentally friendly
In recent years, we often hear terms such as SDGs and carbon neutrality. As a government policy, sustainable development and a decarbonized society are being promoted. Along with this trend, companies are also required to act responsibly.
The SDGs (Sustainable Development Goals) are sustainable development goals, i.e., they aim to establish economic development while taking the environment into consideration. Especially attracting attention is ESG investing.
ESG refers to investment that considers Environment, Social, and Governance factors, and is already becoming an investment trend. In other words, consideration for the environment and society is directly linked to corporate evaluation and corporate value.
These themes are no exception in the plastics industry. In recent years, the plastics industry has faced many environmental load problems. For example, discarded plastic waste flowing into the ocean can cause landscape destruction, environmental pollution, and adverse effects on marine ecosystems. In addition, there are concerns that eating such seafood containing microplastics of 5 mm or less may affect the health of the human body. Given this situation, environmental measures such as CO2 reduction will become essential in molding factory as well.
Therefore, this time, the theme is "environmental measures of plastic molding factory", and the energy conservation activities that molding factory can work on are divided into two parts: The first part and The latter part. In this article, we will focus on CO2 reduction.
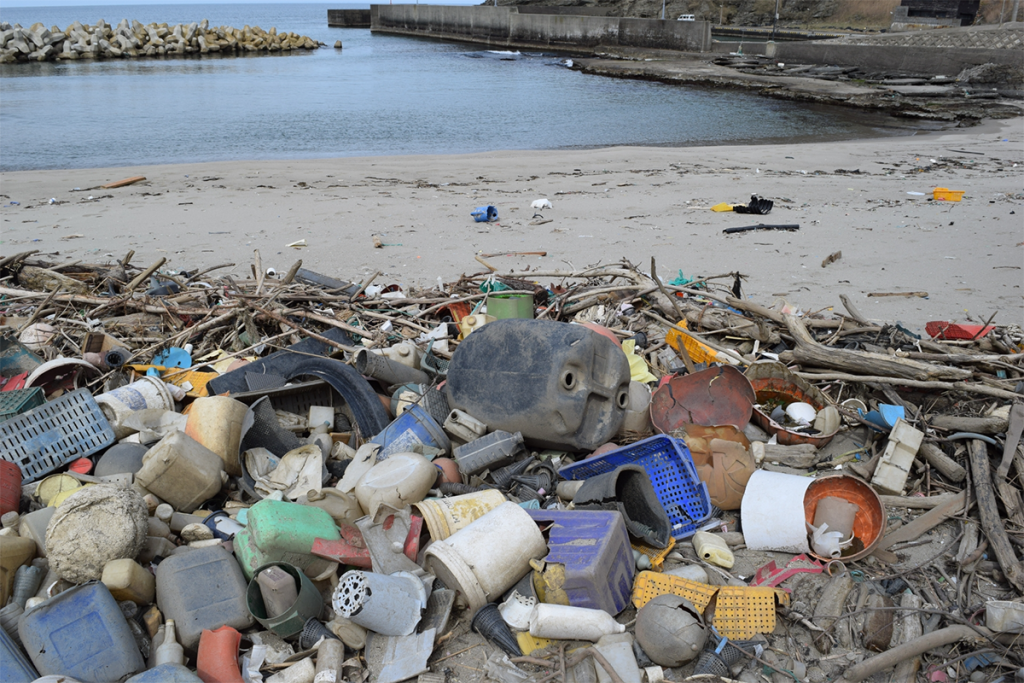
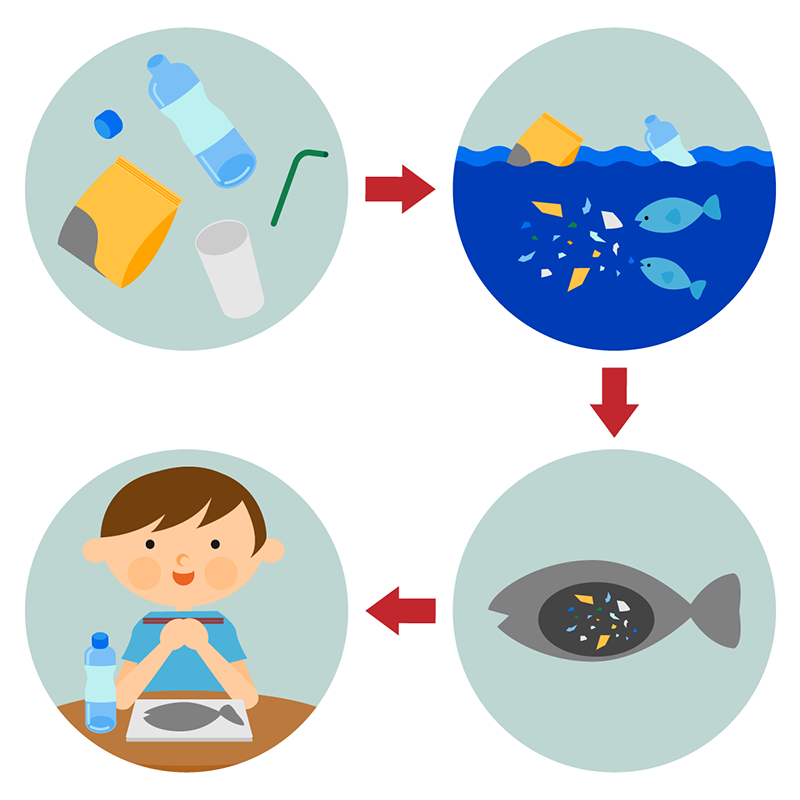
Turn “waste” into “value”
It may be difficult to know exactly what to do when it comes to "consideration for the environment and society," but how about starting by eliminating the "waste" energy in front of you? Uka Energy saving means not only reducing our own electricity costs, but also reducing CO2 emissions in the process of generating electricity.
So, what kind of solutions are there to convert the energy wasted in the molding factory into "value"?
What consumes the most electricity in molding factories?
Is it wrong to say that molding machines consume most electricity?
Have you ever thought like this? It is difficult to save energy, because a molding factory is a large factory with a large number of molding machines. Because molding factories use a lot of electricity for the molding machines, and if we shut them down, our work will not get done."
In fact, the perception that "molding machines consume the most electricity" may be out of date.
It is true that conventional hydraulic molding machines consume a lot of electricity. Hydraulic molding factory have a simple structure, are hard to break, and have power. However, it seems that more and more factory are adopting electric molding machines for small items and precision molded products.
Compared to hydraulic molding machines, electric molding machines consume significantly less power, about 40 to 50%, and Power is overwhelmingly lower than before.
The key point under these circumstances is the auxiliary equipment.
Percentage of energy consumption
Molding machines are not the only equipment that consumes electricity in a molding factory. A large number of peripheral devices that require large amounts of power are used, such as dryers, Temperature controllers, Conveyors, and air conditioners.
Now let's look at the percentage of energy used in the molding factory.
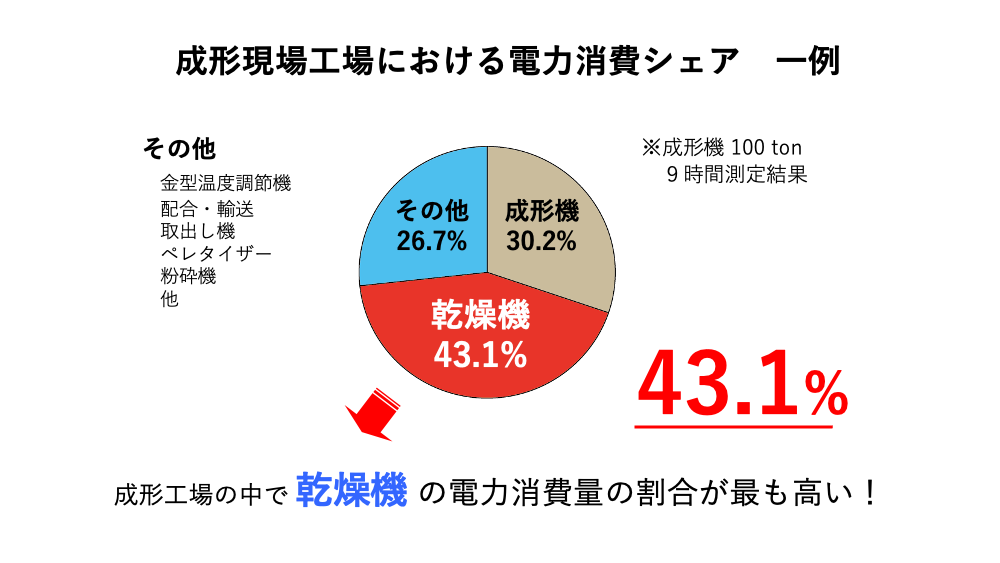
This graph shows the ratio of actual molding using a 100 ton electric molding machine and measuring the Power consumption of each Equipment. As the graph shows, it was actually the dryer, not the molding machine, that had the highest percentage of Power consumption.
Waste leads to more wastes
What is wasted energy in the context of diverse power consumption?
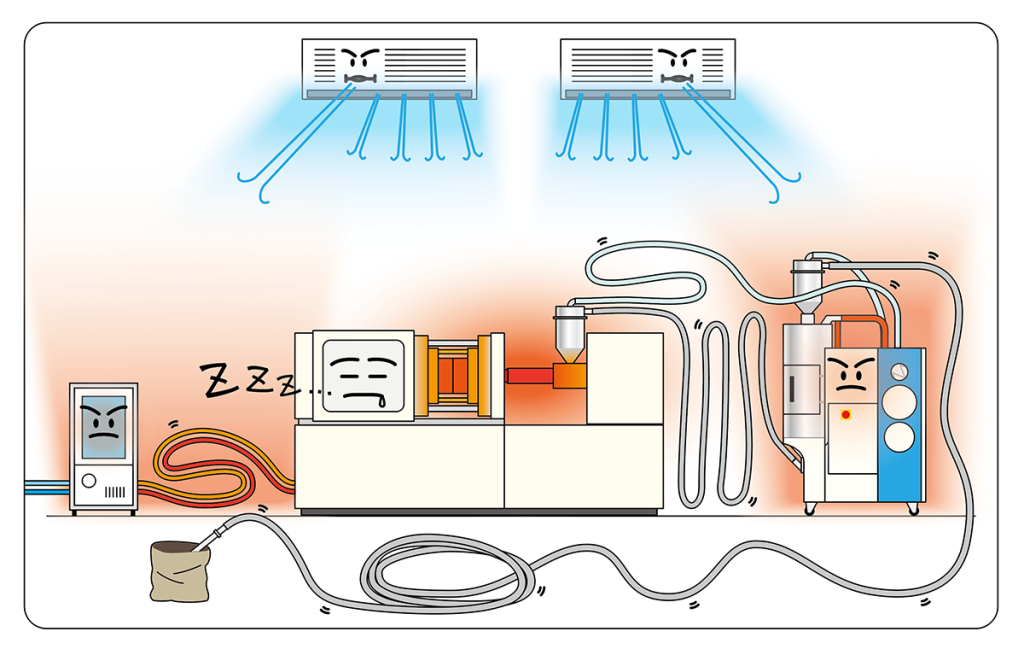
For example, even when the molding machine is not running, peripheral devices such as Mold Temperature Controller and dryers are in operation and continue to dissipate heat. On the other hand, don't you always run the air conditioner so that the site doesn't get too hot?
Using electricity to generate heat and electricity to cool it down. In a sense, this is a situation where waste is leading to more waste.
To reduce such wasted energy, it is necessary to take measures for each equipment.
In this column, we introduce three of them: dryers, chillers, and molding machines.
How to improve energy efficiency
Dryers
In the previous section, as a result of actual measurement in the test environment, we showed the data that it was the dryer that used the most energy in molding. In other words, the most effective way to save energy is to reduce the Power consumption of the dryer.
iplas dehumidifying dryer
Dehumidifying dryer equipped with a self-control function monitors the drying condition of the resin and controls Drying air flow rate and regenerated Air flow rate to maintain the optimal drying condition. Furthermore, the "Dehumidifying dryer MJ6-i" achieves significant energy savings by operating with the minimum necessary energy according to the amount of resin and the operating status of the molding machine.
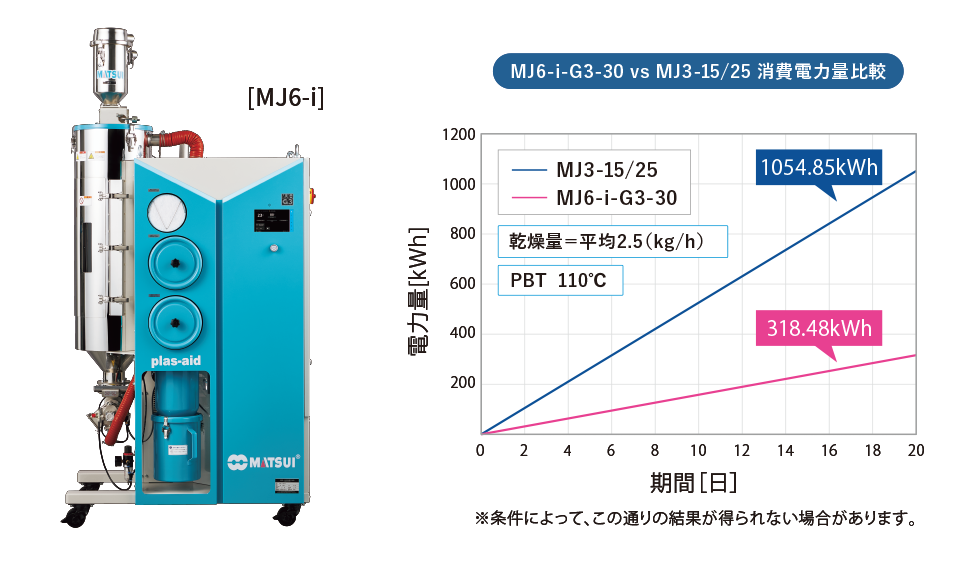
There are also options that can be installed in existing equipment.
Valve-type drying optimization system
By adding a valve-type drying optimization system to the existing Dehumidifying Dryer (MJ3), the sensor monitors the temperature of the drying hopper and controls the Air flow rate, minimizing the power used by the heater. can be suppressed.
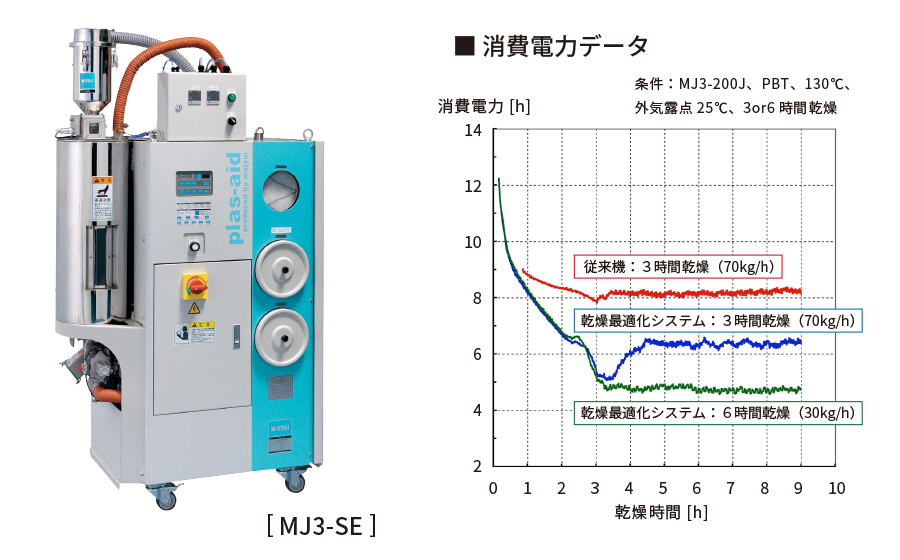
Exhaust heat recovery unit
By attaching the waste heat recovery unit to the existing hot air dryer (HD2) and reusing the waste heat, the electricity consumption of the Main body can be saved by up to 33%. As a result, it leads to reduction of waste heat to the work environment.
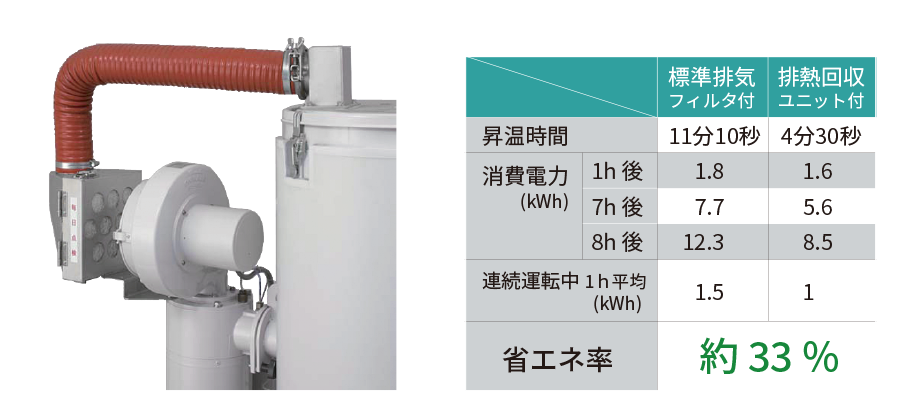
These solutions have the advantage of being relatively low cost and easy to realize the energy saving effect.
Hopper insulation cover
Wrapping the hopper with a heat insulating cover prevents heat dissipation and reduces the temperature around the hopper by 10 degrees or more. This stabilizes temperatures, saves energy and improves worker safety.
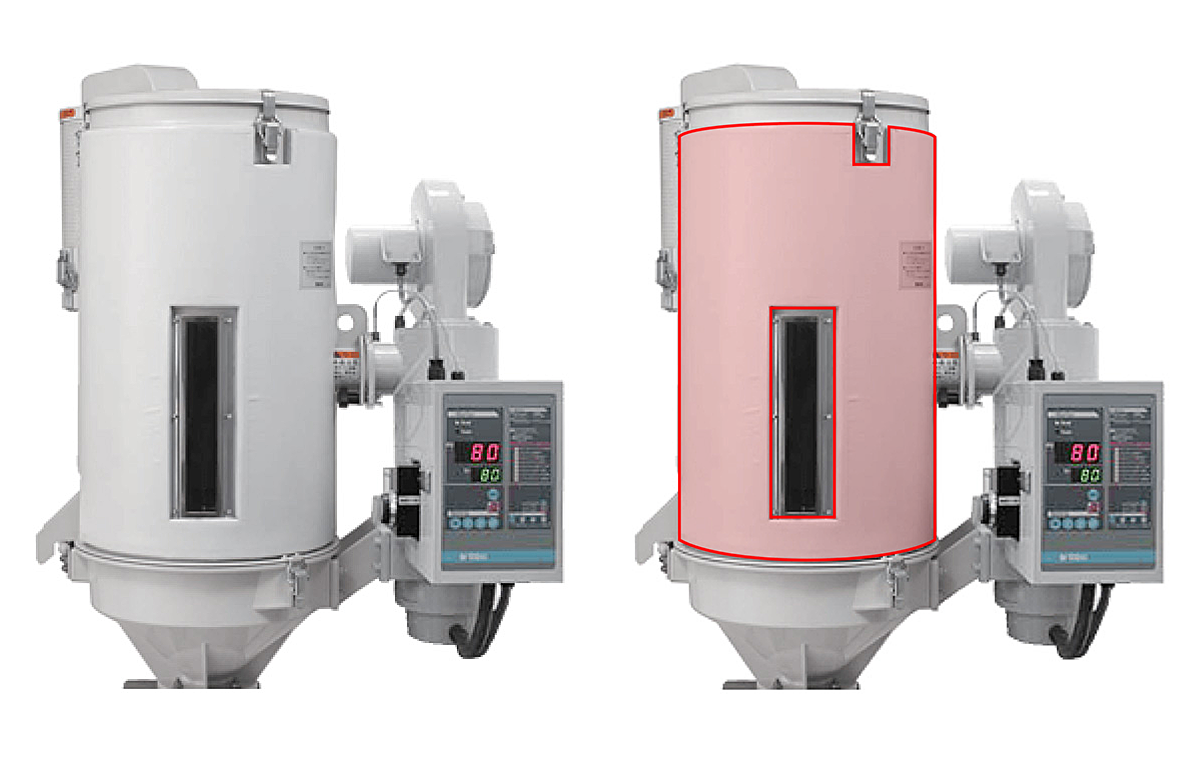
All of the energy-saving solutions related to dryers up to this point not only save energy in the equipment, but also reduce heat radiation to the work environment, which reduces the air conditioning load and makes it possible to use it with an air conditioner. It also reduces the amount of electricity consumed, which leads to improvement of the situation where "waste" produces "waste".
Chillers
Free-cooling system
Free-cooling system is a solution that saves energy by using the outside air temperature. The chiller is stopped when the outside temperature is low, such as in winter, and the water from the cooling tower is used directly as cooling water. It can save up to 54% of power compared to a normal continuous chiller.
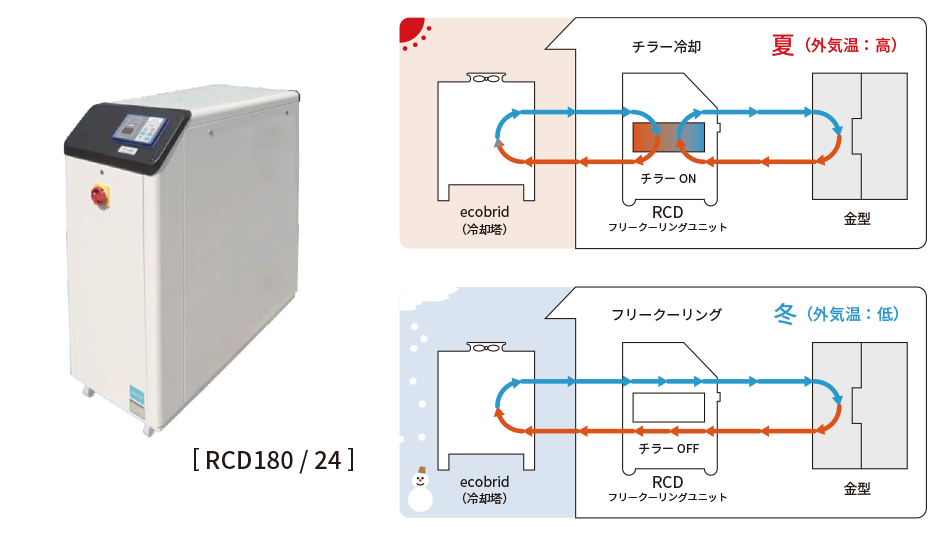
Water cooling chiller
Our chillers equipped with self-control function enable significant energy savings by using an inverter to control operation according to the heat load situation.
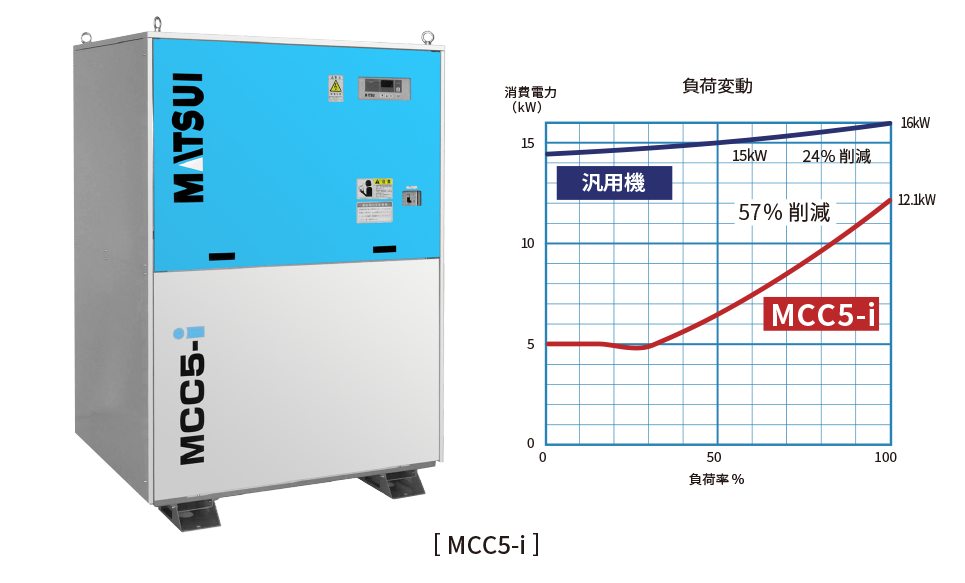
Click here for details ⇒ Water-Water cooling Chiller inverter control MCC5-i
Molding machines
The main body of molding machine is difficult to reduce energy consumption by modifying the moving parts. However, it is possible to suppress the energy required for temperature rise by suppressing heat dissipation and heat transfer generated from the heating cylinder and mold during molding.
Cylinder heat insulation cover
By wrapping the heating cylinder with a heat-retaining cover, heat radiation is suppressed and the heating efficiency of the heater is improved, which simultaneously saves energy and reduces the burden on the work environment, and also helps prevent workers from getting burned. Although wiring is required, the ease of installation, which can be done simply by wrapping it around the heater, is also appealing.
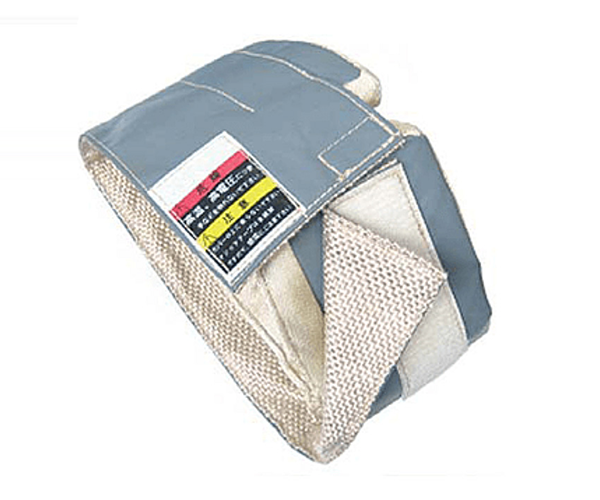
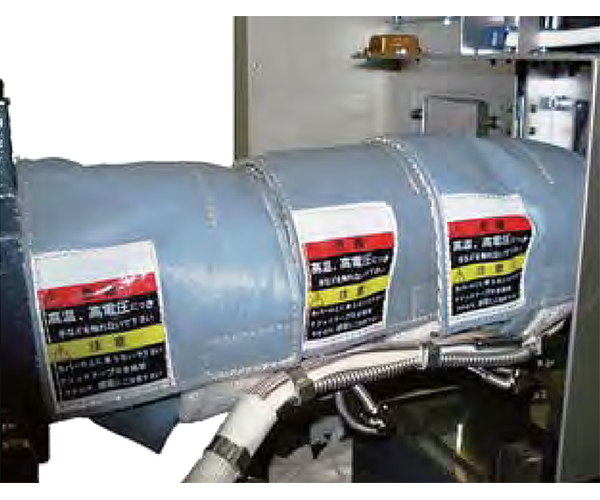
Mold insulation board
The temperature of the mold is controlled by Temperature controllers, but if left as is, heat will escape from the attachment points between the same metals. By placing an insulating plate between the mold and the attachment plate (platen), unnecessary heat transfer is suppressed, reducing the temperature control load and achieving energy savings. In addition, the temperature distribution of the mold becomes constant, allowing for stable molding, which also leads to improved dimensional accuracy and appearance quality of the molded product.
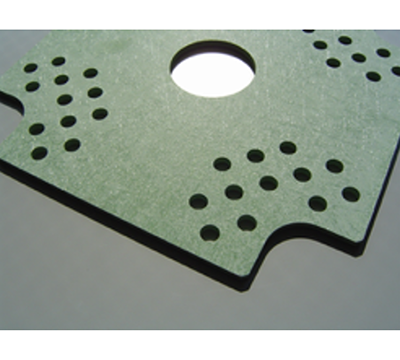
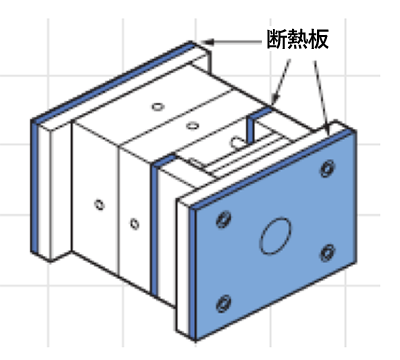
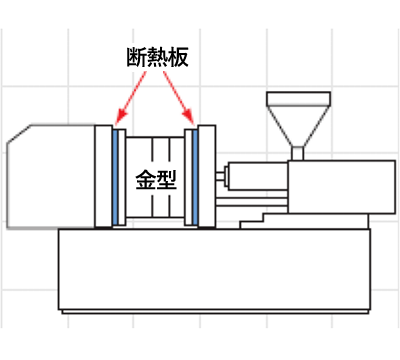
In addition to the solutions introduced above, we offer a wide variety of methods and items. We will work with you to realize an energy-efficient and comfortable molding factory that meets your factory facilities, budget, and initiatives.
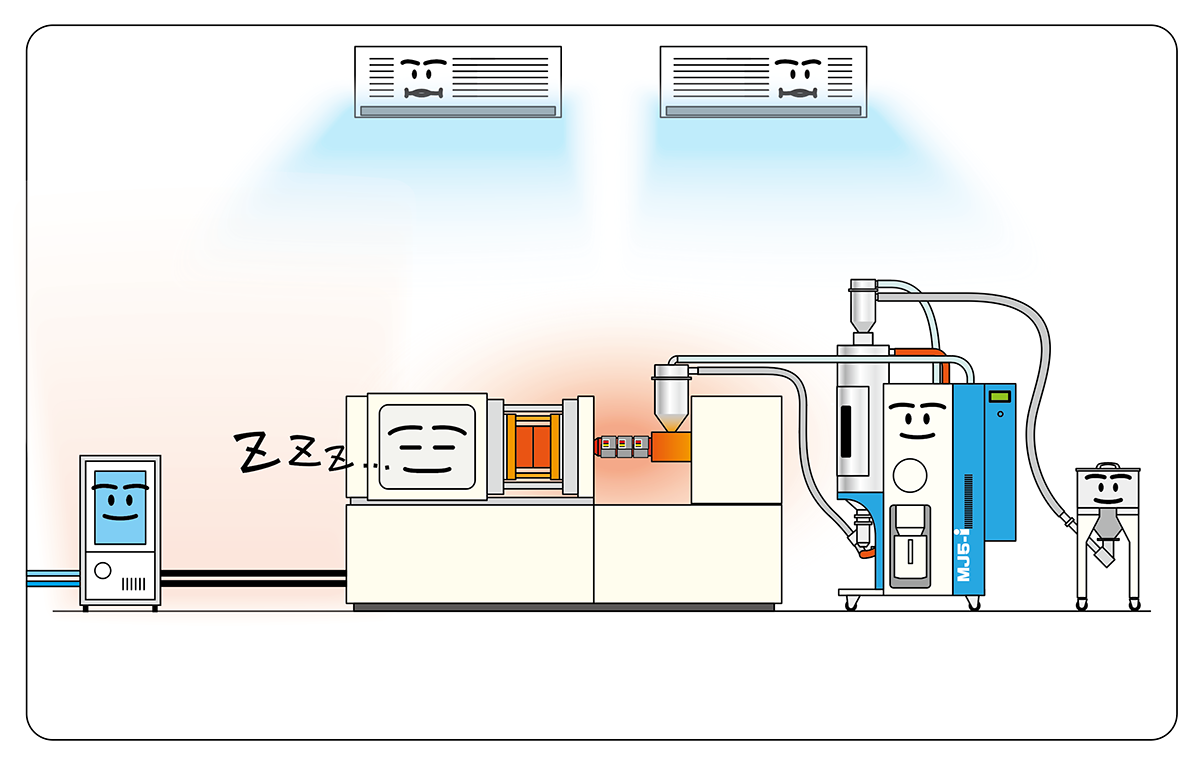
Summary
When we talk about CO2 reduction and sustainability, we tend to see it as a topic in the distant world, but if we start by reducing wasted energy in our factories, the topic becomes more familiar.
Saving energy in a factory can start with simple things such as keeping things tidy and turning off equipment that is not in use. Then, new solutions can be introduced to achieve higher effects. This is a good time to invest in this area, as the cost of power is skyrocketing.
Savings on power costs will directly reduce CO2 emissions, which increases the value of your company. We, Matsui, offer solutions to reduce resource consumption and increase corporate value. Please feel free to contact us if you have any questions about environmental measures or energy saving in plastic molding.
CX Design Department Yasuhiko Iijima