Aiming for factor4 of molding factories
Cooling is a key to shortening molding cycle!
2022.03.23
What Is a Molding Cycle?
A molding cycle refers to the complete sequence of operations from the start to the end of a molding process or the time it takes to complete one full cycle.
Example:
Mold Close (3 sec) + Injection (1 sec) + Holding Pressure (5 sec) + Cooling (20 sec) + Mold Open (2 sec) + Part Ejection (5 sec) = Total Cycle Time: 36 seconds
Each molding cycle involves multiple stages. Improving molding efficiency means reducing the time spent on each step while maintaining product quality. This leads to a shorter overall cycle time.
Why Does the Molding Cycle Get Longer?
Reducing the molding cycle time is essential for increasing production profitability. However, depending on the shape of the molded part, it is not always easy. You may have tried to shorten the cycle but ended up with defects, and eventually had to abandon the attempt. This is a common experience in molding operations.
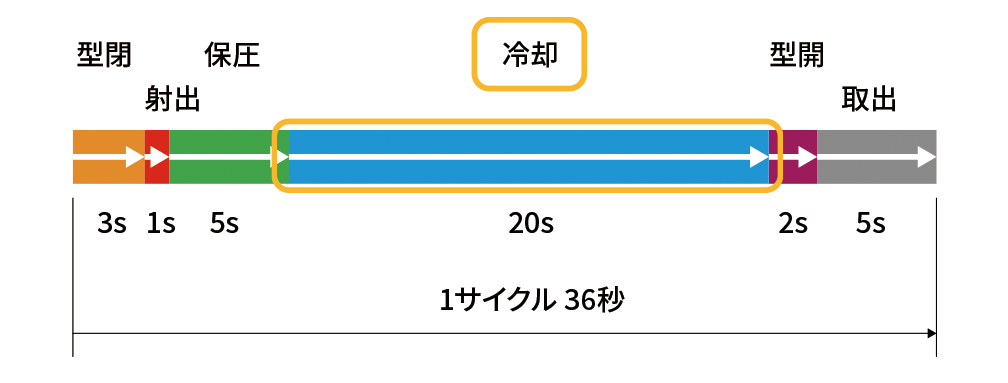
Among all the steps in a molding cycle, cooling often takes up the largest portion of the time. That is why focusing on this stage can be one of the most effective strategies for reducing the total cycle time. What are some practical methods to shorten the cooling time?
We offer a variety of solutions based on different approaches to help you maintain your initial cycle times and achieve further reductions.
How to Reduce Cooling Time
Improving Stringing Issues
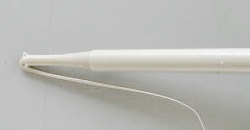
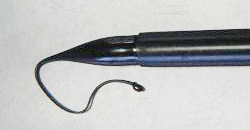
Stringing on molded parts often occurs when the nozzle temperature of the injection molding machine is too high.
One way to address this issue is by extending the cooling time. However, this leads to longer cycle times. A more effective solution is to use a heat insulated sprue bush.
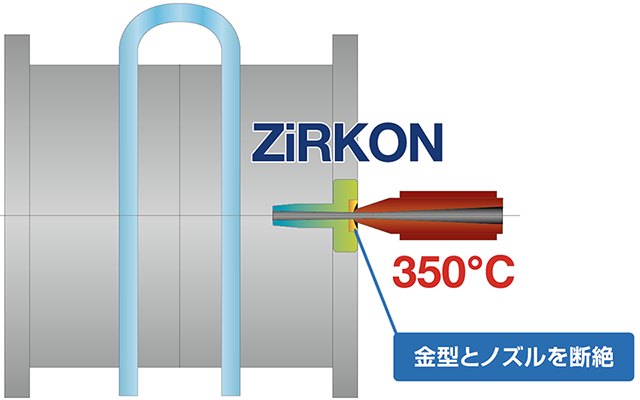
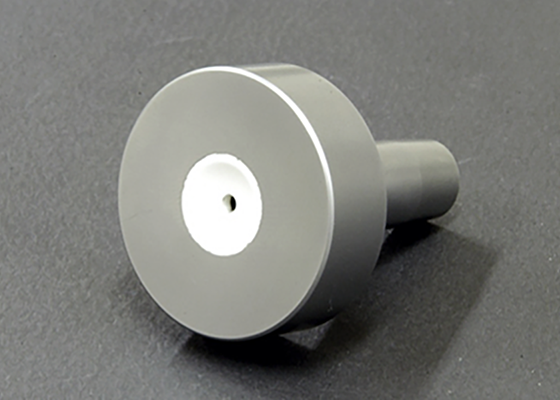
Heat Insulated Sprue Bush ZiRKON features a ceramic insert at the contact point with the nozzle. This prevents heat from being transferred to the mold. By blocking heat transfer to the mold, the resin inside the sprue cools and solidifies more quickly, reducing the risk of stringing.
Improving sink marks on uneven thickness
The neck is that the ribs attached to reinforce the thin part and the uneven thickness Construction such as the boss are easy to sink.
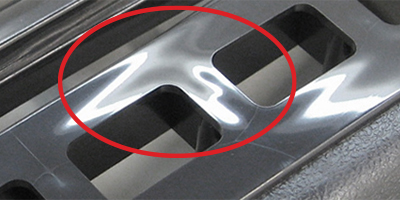
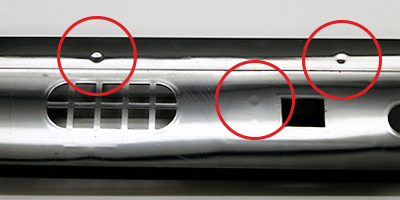
It is common to take a long cooling period to prevent sink marks.
"Foam molding" is an effective method to suppress sink marks without lengthening the cooling time. ⇒ MuCell
By injecting gas into the Dissolution resin, Inside foaming can occur in the resin and sink marks can be suppressed.
Reducing Cooling Time in the Sprue Area
When molding a Construction such as a thin wall, a large number of pieces, or a multi-point gate, the sprue part tends to be larger and thicker than the molded product. However, it takes a long time to cool down because it is necessary to wait until the thick sprue part hardens.
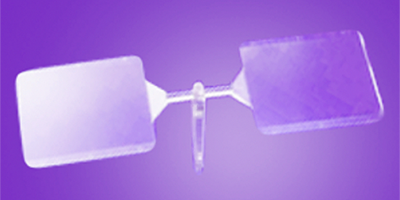
Therefore, there is a method of using a sprue bush with a 3D water pipe.
Nowadays, it is easier to manufacture water pipes with complicated three-dimensional Construction than 3D metal printers, so by actively cooling the sprue part, the cooling time can be shortened as a result.
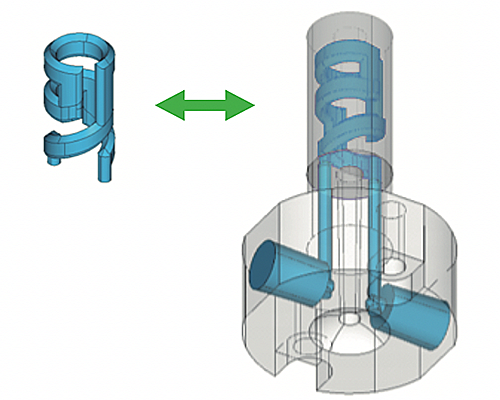
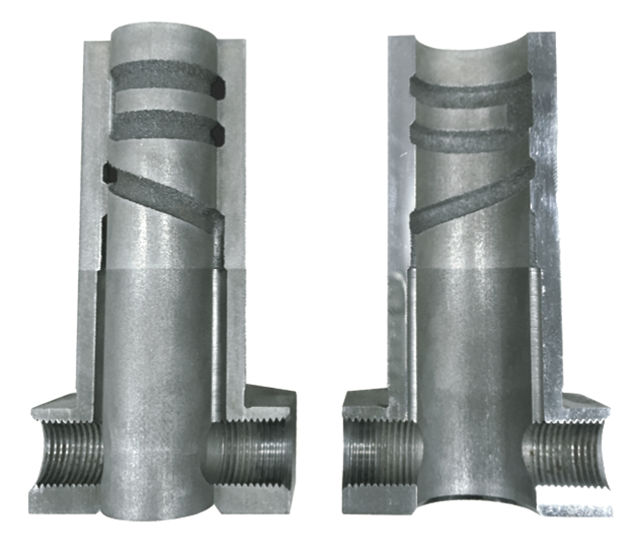
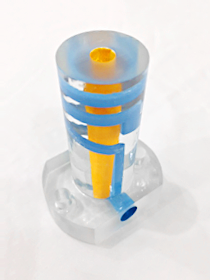
Water tube design to increase cooling efficiency
Spur is not the only place where complex water pipes can be applied.
Even if the water pipe cannot be designed due to the complicated structure on the core side, it can be handled by manufacturing the mold nest with a 3D metal printer. Click here for details ⇒ 3D Water Pipe Mold Nesting
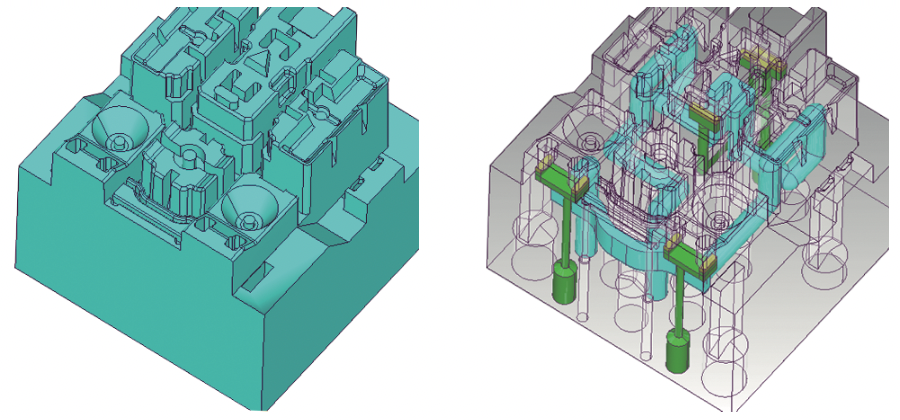
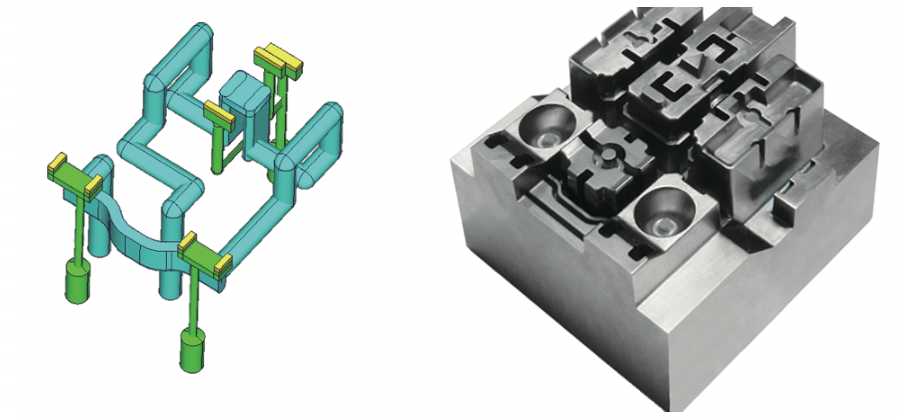
With a 3D metal printer, you can design the best water pipe for your product, even with complex shapes. By optimizing the water pipe, it can be cooled uniformly to improve efficiency, and good products can be obtained even in a short time. Depending on the conditions and materials, it is possible to significantly shorten the molding cycle time.
Prevent mold condensation
As a result of lowering the set temperature for the purpose Reduction in cycle time mold may be cooled too much and condensation may occur.
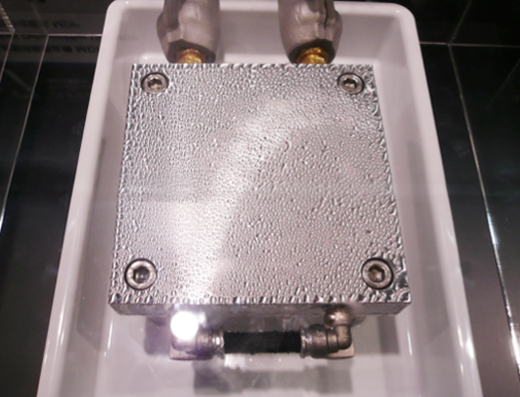
One of the solutions to the dew condensation on the mold is the"mold dew condensation prevention device".
By blowing low dew point air to reduce the moisture in the air around the mold and prevent dew condensation on the mold, the temperature of the chiller water can be set lower, which leads to shortening of the molding cycle.
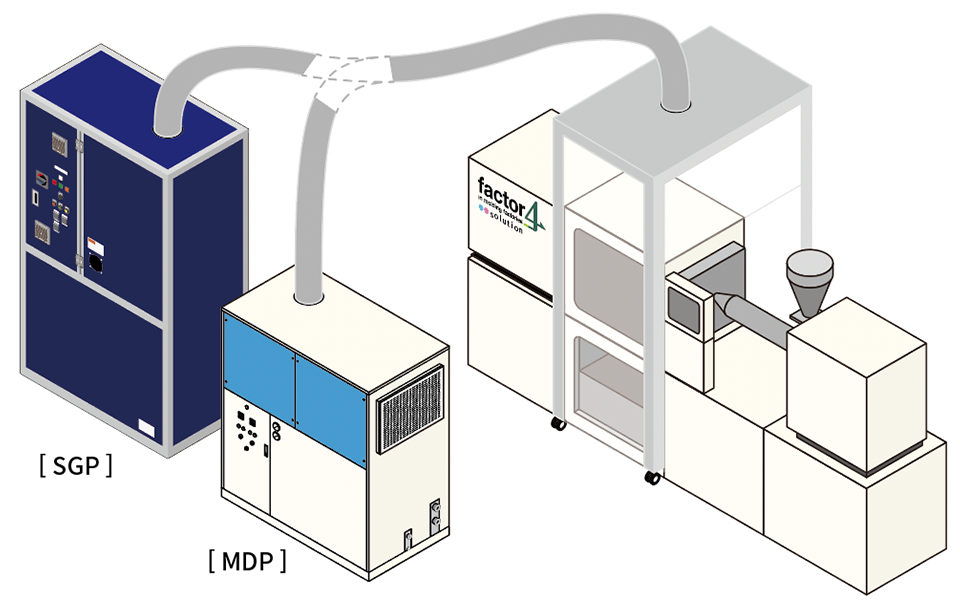
Click here for details ⇒ Anti-condensation machine SGP
How to maintain cooling time
A mold temperature controller and chiller are indispensable for cooling the mold. However, since these are cooled using water, rust, foreign matter, and scale will inevitably accumulate Inside after long-term use. Scale is a mineral such as calcium and magnesium contained in water, and when it precipitates and hardens, it becomes hard like a stone and cannot be easily removed.
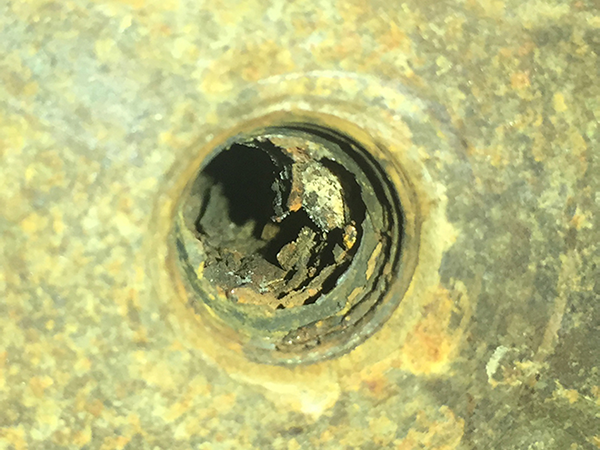
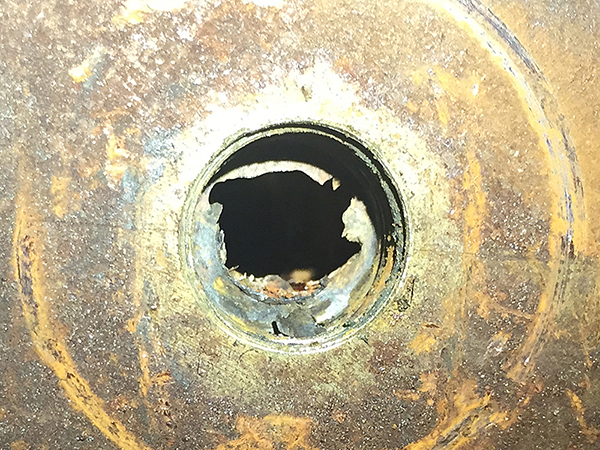
If the scale etc. sticks to the Inside of the water pipe of the mold, it will be difficult for water to flow and the water flow rate will drop.
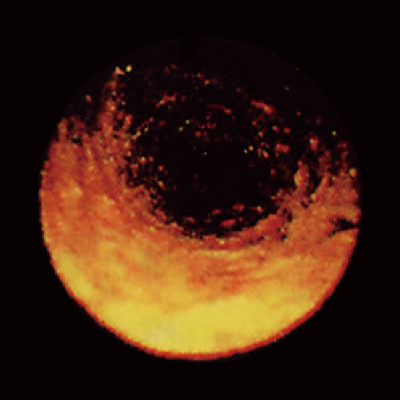
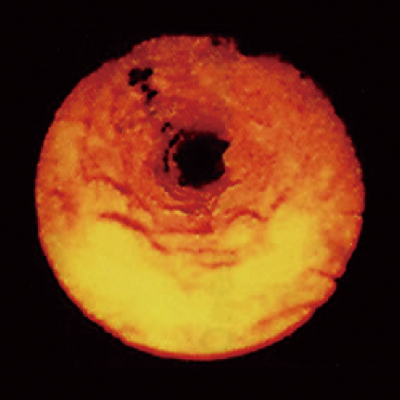
Actually, in the mold in the above picture, the water flow that was originally flowing at 18Lmin has dropped to 8Lmin. As the water flow rate drops, the heat Replacement rate also drops.
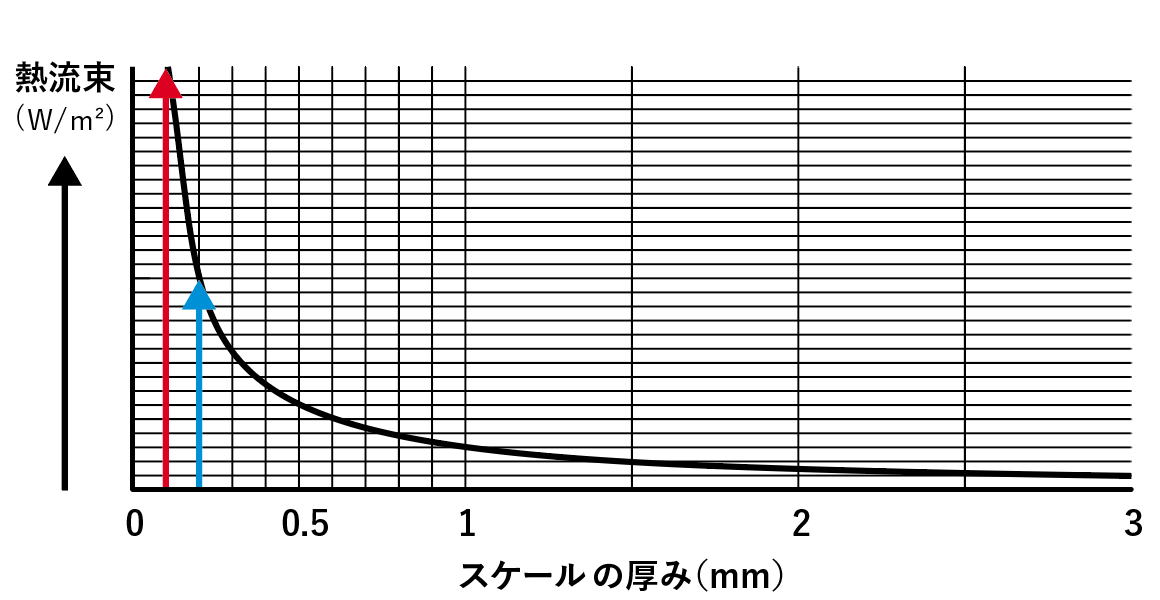
As shown in the graph, the heat flux is halved just by increasing the thickness of the scale from 0.1 mm to 0.2 mm. As a result, the heat Replacement efficiency deteriorates, and a longer cooling time is required compared to when molding started.
Cleaning the scale of the mold water pipe
There are several methods for removing scale from mold water pipes, including using chemicals, re-drilling holes, scraping with a grinding wheel or wire brush, and ultrasonic cleaning.
However, there are risks associated with chemicals, such as harmful effects on humans and the environment, and damage to the mold. We would like to introduce a method called low-pressure combined water jet cleaning as a solution to scale problems.
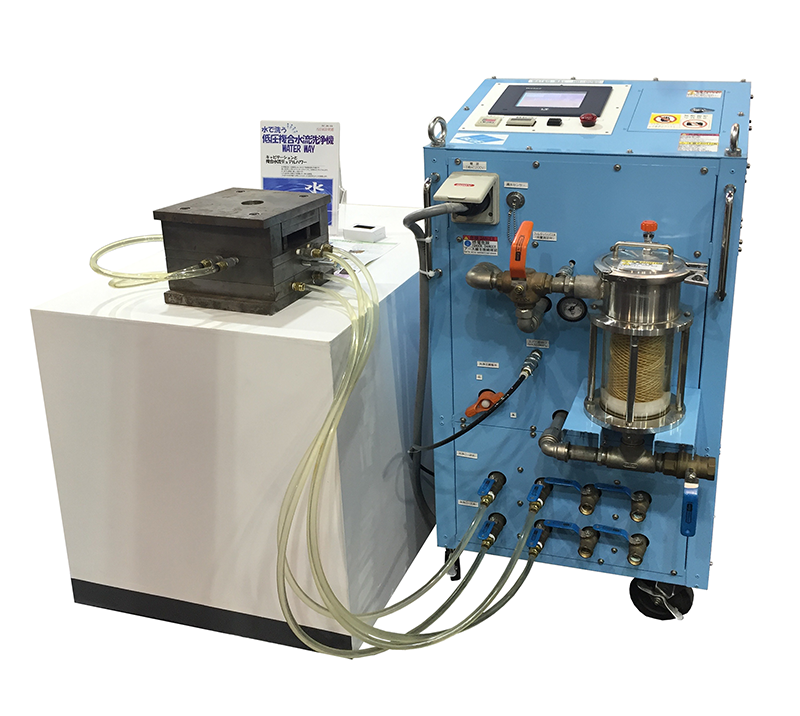

The greatest feature of low-pressure composite water jet cleaning is that it does not use any chemicals.
Water containing air is passed through the water pipe to generate cavitation and remove scale and rust inside the water pipe. Since only water and air are used, the water used for cleaning does not need to be neutralized or treated as industrial waste, and can be discharged as is.
Preventing scale formation by improving water quality
There is also a method of suppressing the generation of scale itself by improving the water quality.
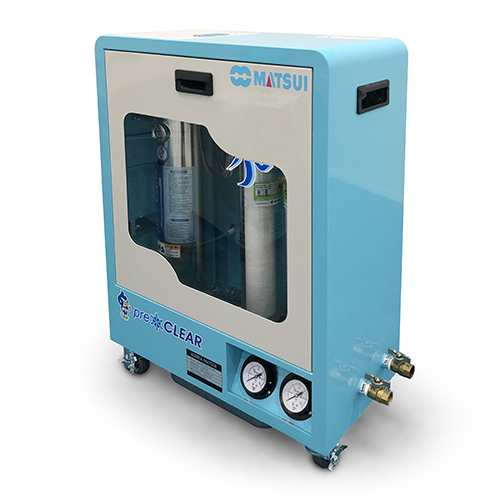
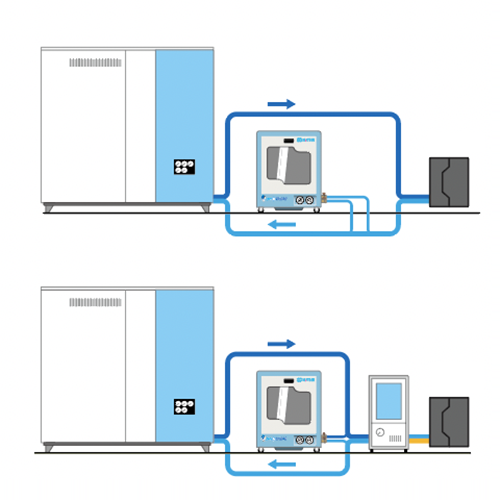
Ion exchange type water softeners with filters use the principle of ion exchange to separate minerals that cause scale, such as magnesium and calcium, dissolved in water, and soften the water. Any floating foreign matter is filtered out by the filter. ⇒ preClear
Another advantage is that it can be easily connected to existing circulation lines, eliminating the need to change large-scale piping lines.
There is also a method without filters. Filterless filters use a gravity centrifuge to remove contaminants that are heavier than water. Foreign matter collects under the body and can be easily discharged from the bottom. Since there is no filter, there is no need to replace it, and it is maintenance-free.
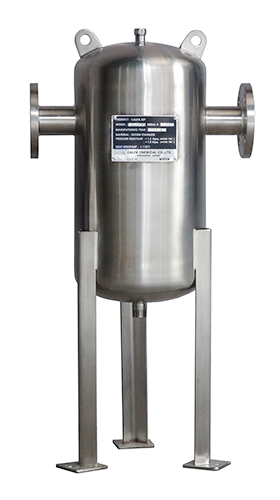
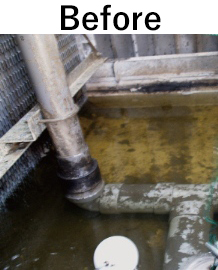

A New Choice for factory Cooling Systems
Current mainstream is Water cooling
Looking around the world, Water cooling cooling systems occupy an overwhelming share of the world market for cooling systems in factory.
Water cooling is roughly divided into an open type and a Closed type.
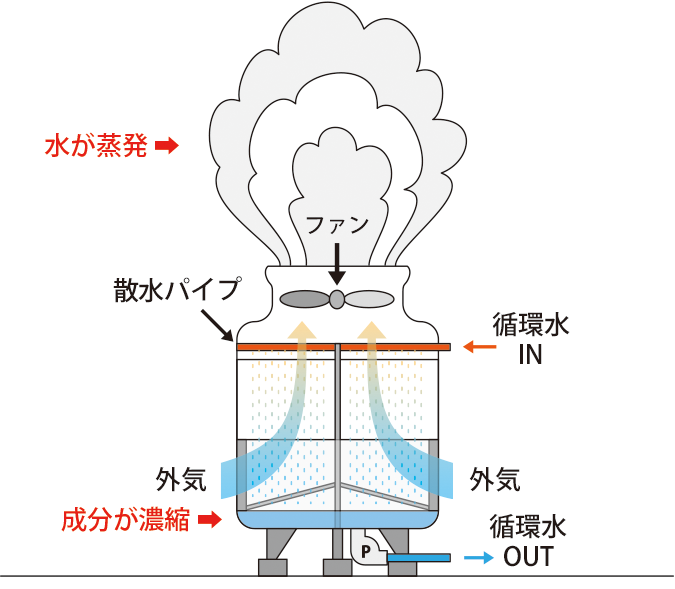
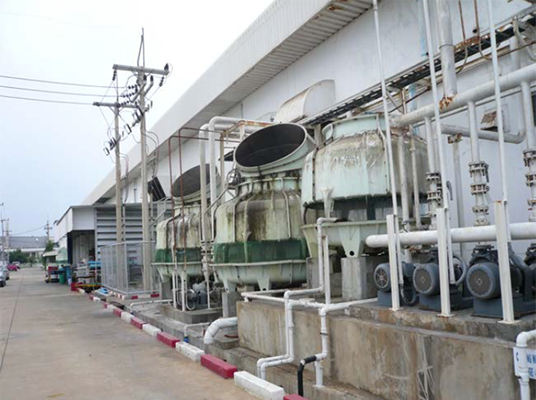
In an open cooling tower, Warm water (circulating water) discharged from the factory is sprayed downward from the top of the tower, and the outside air is used to cool the tower. The cooled circulating water collects at the bottom and is returned to the factory by a pump. Cooling by active evaporation consumes a large amount of circulating water.
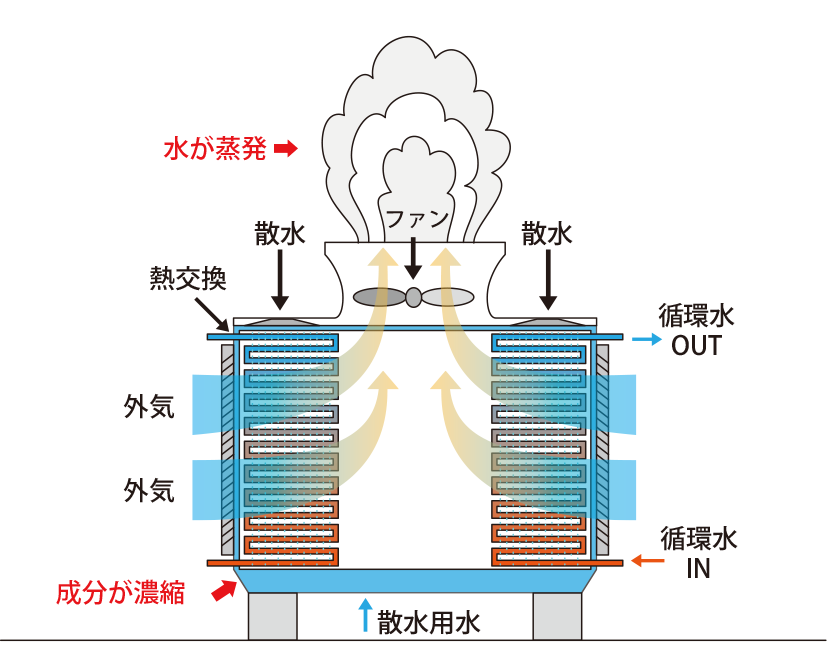
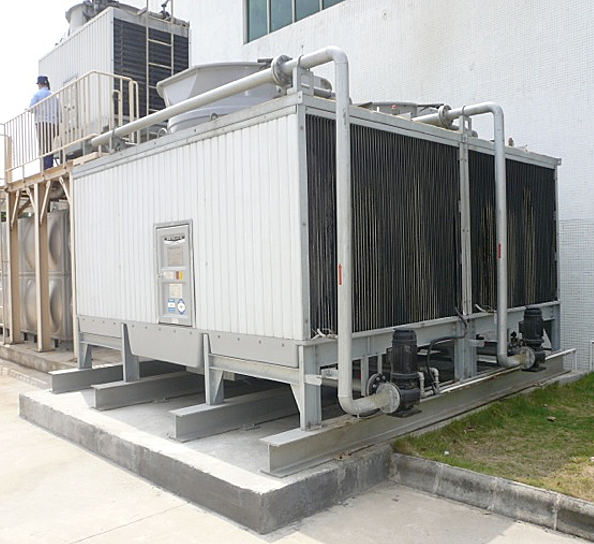
In the Closed type, the warmed circulating water passes through the copper tube Inside the cooling tower. By cooling the copper pipe with sprayed water, heat Replacement is performed and the circulating water is cooled. Since the circulating water does not come into contact with the outside air, there is no concern about pollution or evaporation, which is an advantage. But instead, a large amount of spray water to cool the copper tube evaporates.
Water cooling problem
Since Water cooling cooling systems use evaporation for cooling, 0.86% of the factory circulating water is lost to evaporation.
Also, there is about 0.05% carryover that is scattered in the air by the fan. Furthermore, as the water evaporates, the impurities in the water become concentrated, so it is necessary to remove the water, which is called blowdown. You also need 0.4% for this blowdown.
Therefore, all together, 1.3% of the circulating water volume is wasted.
In addition, since the circulating water evaporates a large amount of water, impurities such as bacteria and scale remain and are concentrated. The polluted water will affect the environment and equipment.
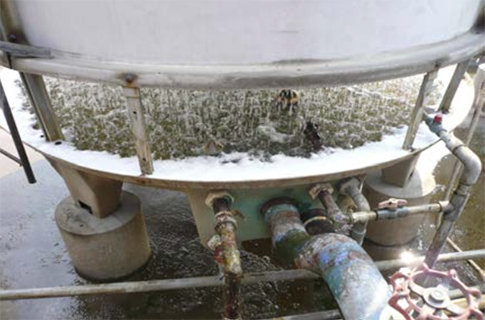
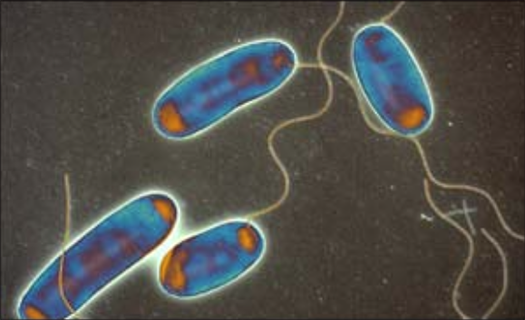
Cooling towers are generally in an environment where Legionella bacteria can easily grow. When water droplets are scattered by the fan, the Legionella bacteria may be scattered to the outside. In some cases, health hazards have occurred, and it is necessary to take measures using chemicals and duct hoods.
If bacteria or algae grow in the circulating water or impurities such as scale accumulate, the piping will be clogged, the thermal efficiency of the cooling tower will decrease, and the cycle time will increase as a result.
Improves water quality to break down scale and prevent rust and corrosion
These problems can be prevented by using a "conditioner".
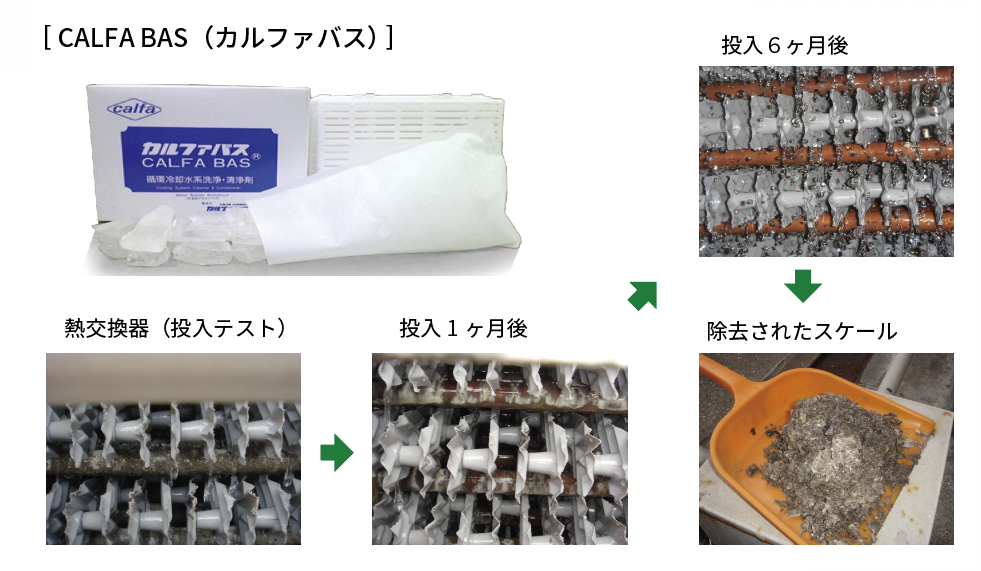
It can be used easily by simply placing a solid agent composed of phosphorus-free and nitrogen-free inorganic substances at the bottom of the cooling tower. It softens the scale inside the pipes and is also effective in preventing rust and corrosion. Environmentally friendly and wastewater free.
Next generation cooling system
There is also a new option, a dry cooler that is Closed and air-Water cooling instead of water-cooled.
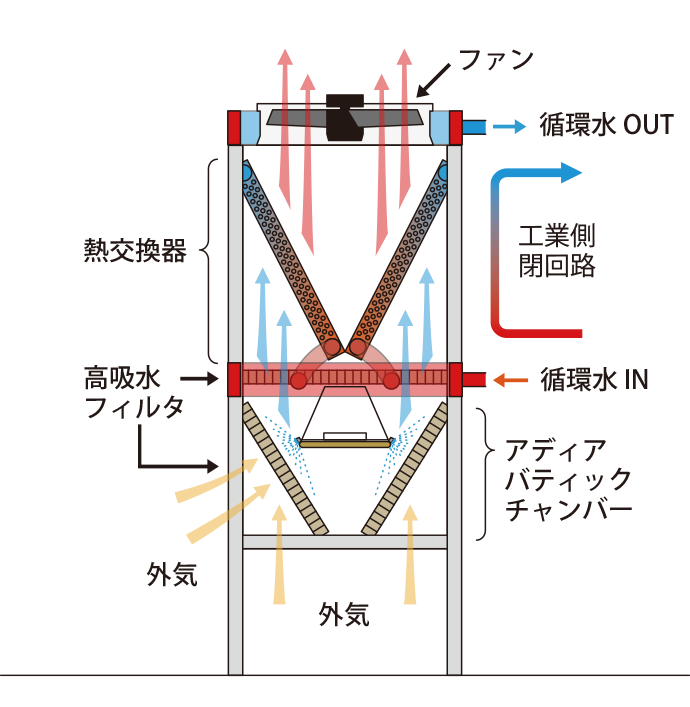
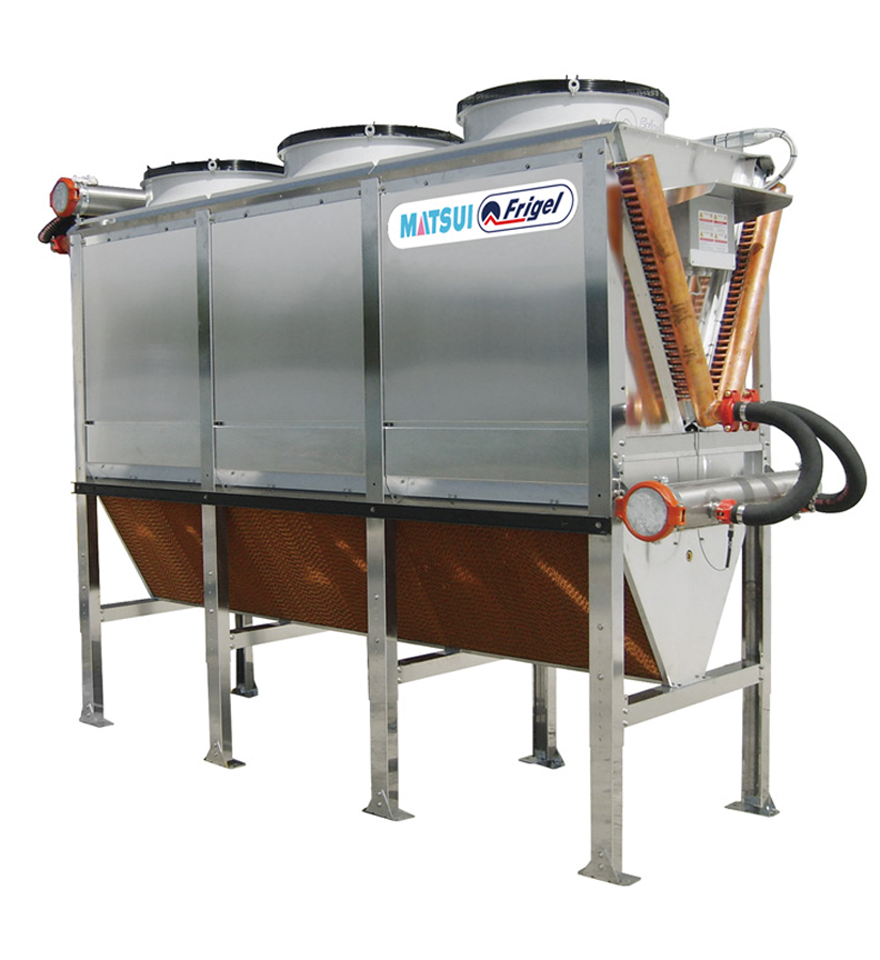
In this cooling system, the circulating water through the copper pipes is cooled by outside air instead of by water. Therefore, compared to the conventional method, the amount of water that has been wasted can be reduced to 1/20. The sealed piping system does not evaporate the circulating water, and the quality of the water is maintained, leading to maintenance of the molding cycle time. Almost no on-site maintenance is required.
Click here for details ⇒ Air Cooled Closed Type Water Cooling System ecobrid
Examples of cycle time reduction
Cycle time shortened by introduction of 3D water tube sprue bushing
37 seconds before introduction to 15 seconds after introduction ⇒ Approximately 60% reduction in cycle time!
- ・Target molded product: Mini DC Jack
- ・Resin used: PET
- ・Product weight: 1.3g (16 pieces)
- ・Runner sprue weight: 2.56g
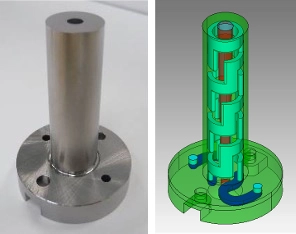
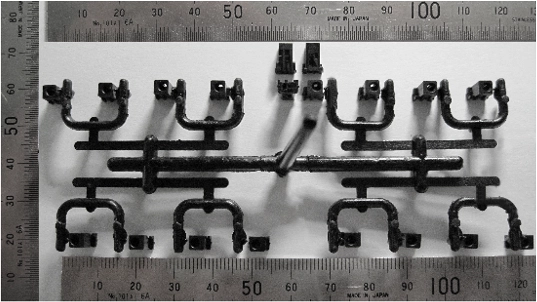
3D Water Pipe Sprue Bush made by metal photo-fabrication 3D printer allows effective temperature control and cooling of the sprue portion and is highly effective in shortening the cycle time of molded products with a thickness of 1.6 mm or less.
Click here for details ⇒ 3D water pipe sprue bush
Cycle time shortened by introduction of 3D cooling water pipe mold
53 seconds before introduction to 38 seconds after introduction ⇒ Approximately 28% reduction in cycle time!
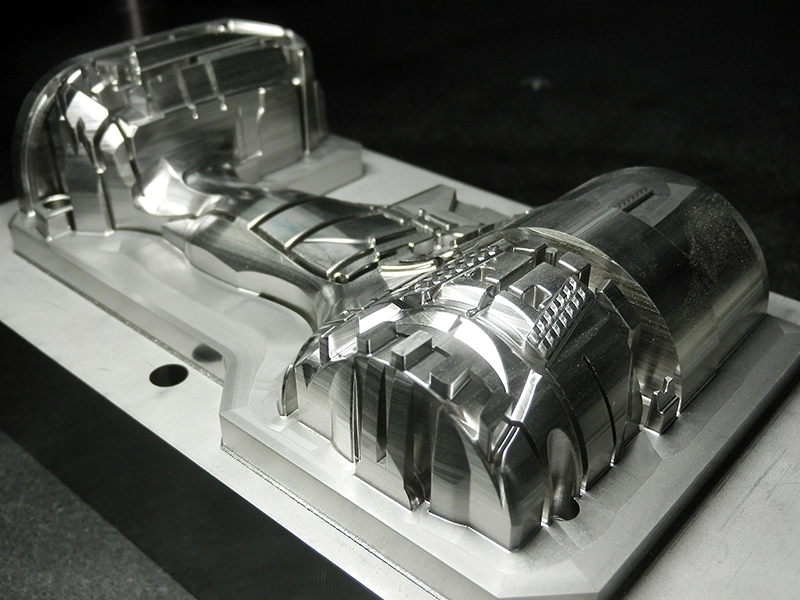
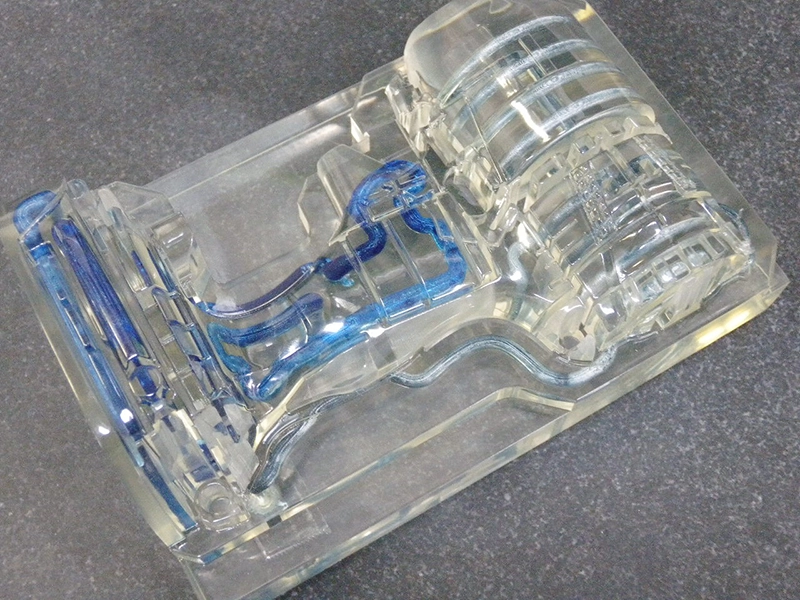
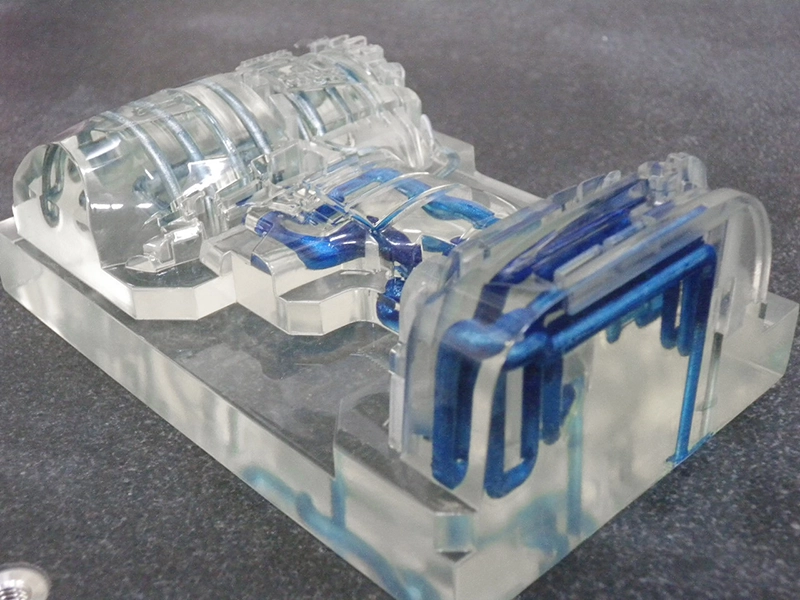
Since the 3D cooling water pipe uses a metal 3D printer, it is possible to freely construct the optimum water channel according to the product. This improves cooling efficiency and Reduction in cycle time.
Click here for details ⇒ 3D water tube mold insert
Summary
Focusing on cooling, we have shown you how to shorten and maintain your molding cycle. It's not as simple as improving one thing and reducing it dramatically. It is important to take appropriate measures for each issue.
MATSUI 's mission is to "realize 'factor4' of molding factory", and we aim to improve the resource productivity of molding factory. We will develop products and propose optimal solutions for various issues in each molding process.
Please feel free to contact us if you have any problems regarding injection molding, such as shortening the molding cycle.
CX Design Department Yasuhiko Iijima