Features
1. Automatic switching of transport direction reduces setup time!
By automating the switching of piping lines for material transport, it is possible to eliminate the labor required for changing materials and complete the work in a short time. It also helps prevent human errors such as inserting the wrong material.
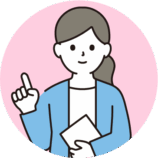
Switch from manual to automatic!
The molecular structure of plastics changes when exposed to heat, oxygen, moisture, and ultraviolet rays. When heat and oxygen in the air cause thermal decomposition and the physical properties decrease, this is called "thermal degradation." Although it depends on the molecular structure, it can cause discoloration and a decrease in strength.

2. Simple structure makes system modifications easy!
Because it is a simple unit with no stagnation points, you can easily build a switching system with any number of directions from the specified dryer to the molding machine. This not only reduces reconfiguration time but also reduces modification costs.
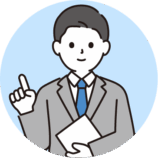
The transport direction is changed by sliding the damper!
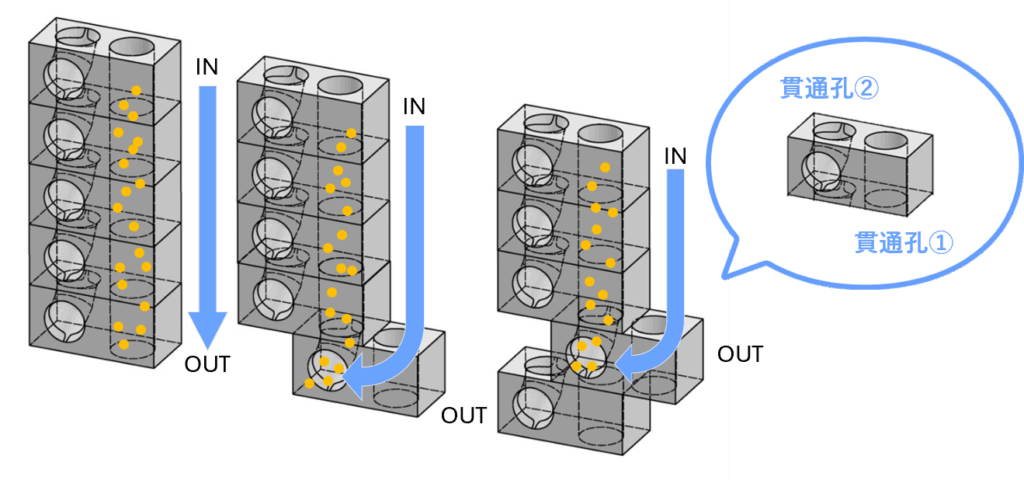
As the damper slides, through hole ① switches to through hole ②.
In this way, the transport switching devices are arranged in a parallel direction.
3. The compact design helps save space in factory!
This space-saving design consists of individual units stacked vertically. It helps to improve the efficiency of material transport in limited spaces without interfering with the flow of materials through the molding factory.
4. It helps prevent contamination caused by wear particles!
By forming an air layer, wear caused by sliding is minimized, making it possible to prevent contamination caused by wear particles. In addition, the switching core part floats and slides, so there is no problem with galling.
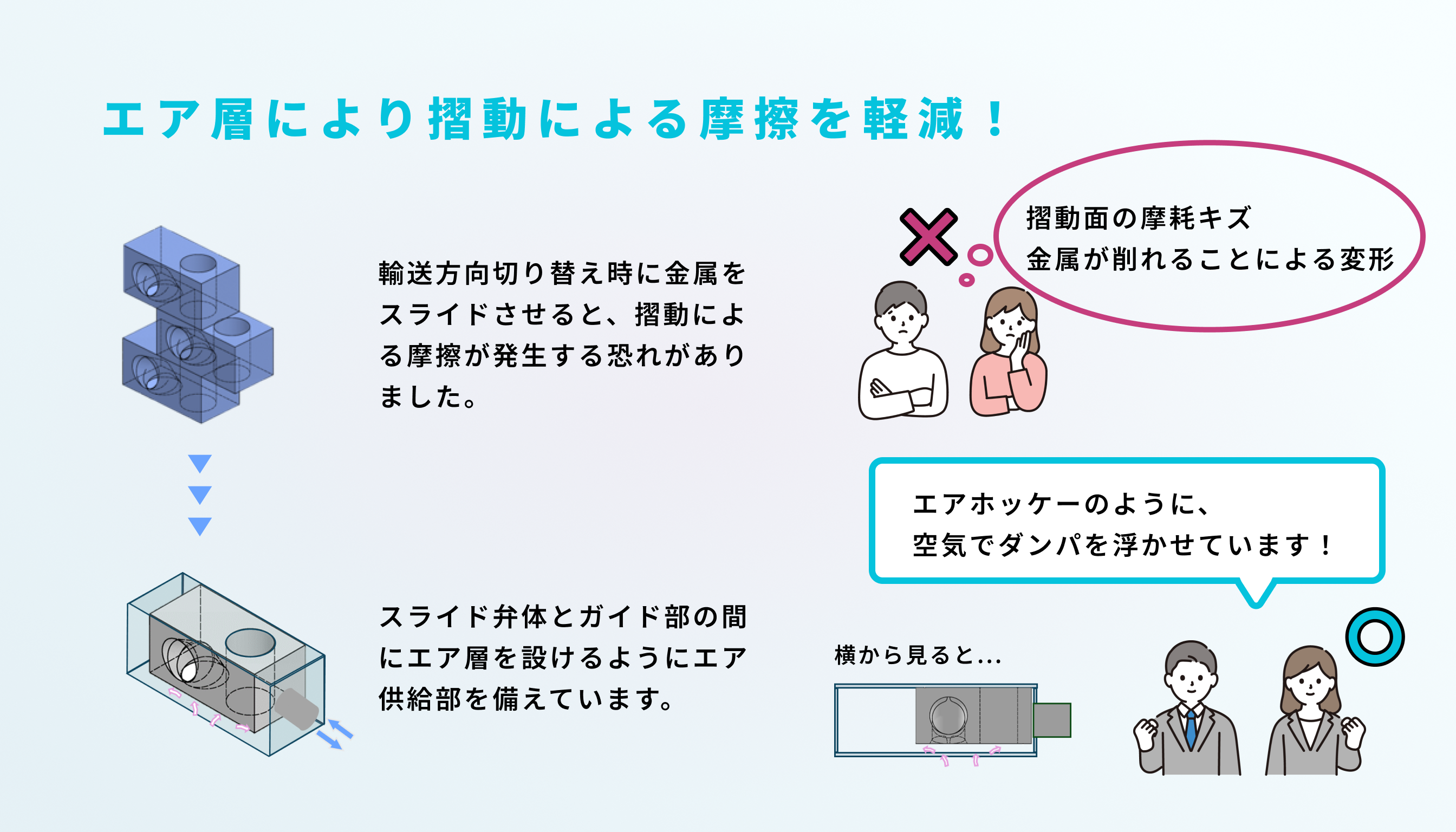
Usage Example
This is an example of using [3 by 3].
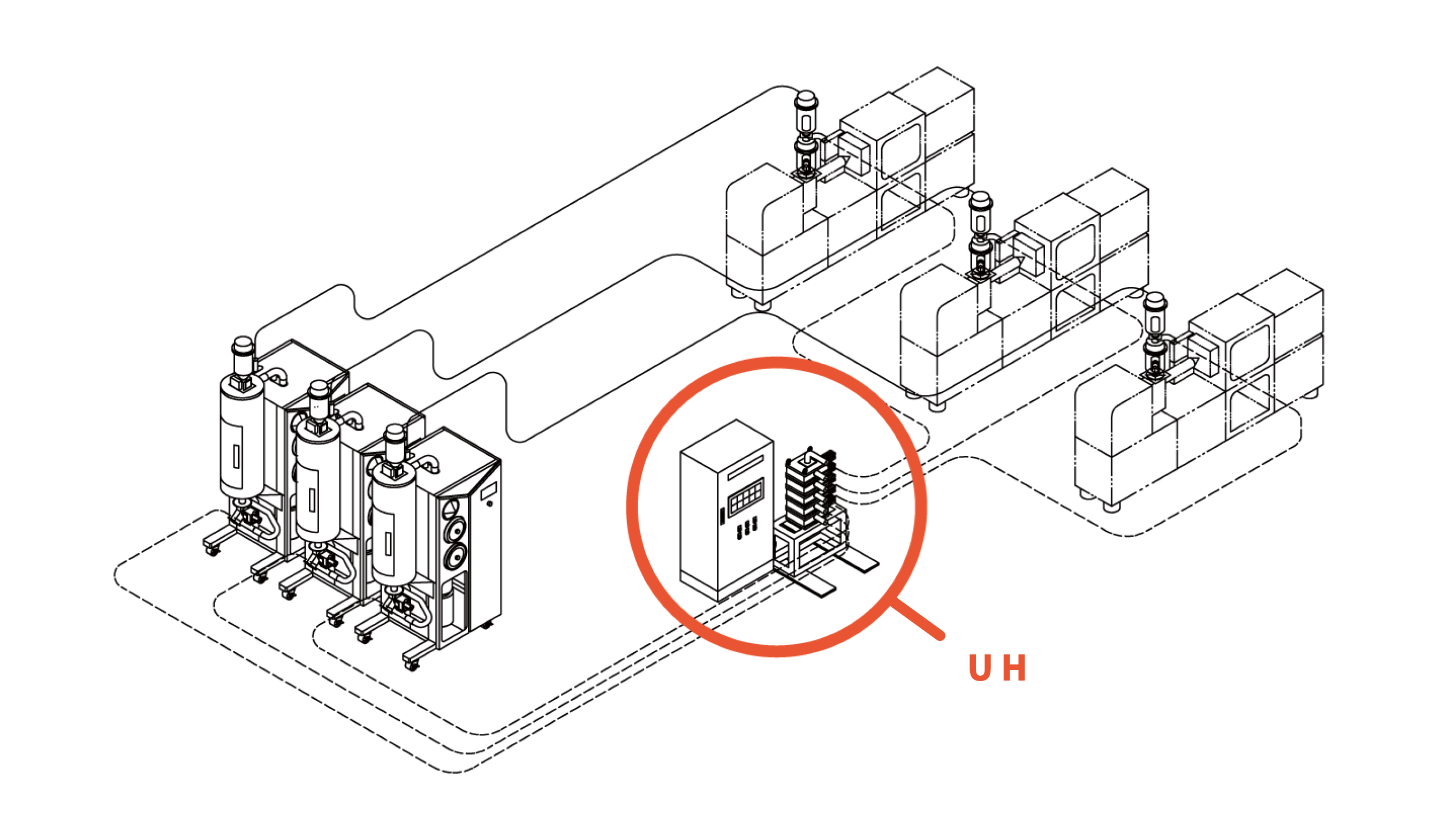