Aiming for factor4 of molding factories
Three molding methods to save weight of plastic molded products.
2023.03.17
Reducing the weight of molded products has been one of the most important issues for the molding industry. Reducing the weight of automobiles, aircrafts, and plastic products (for example, containers and pallets used to transport goods) will improve fuel efficiency and reduce CO2 emissions. In the housing and construction industry, the weight reduction of building materials improves earthquake resistance. Electronic devices and medical equipment reduce the burden when moving and using them. be connected.
For molding manufacturers, this also leads to a reduction in the amount of resin used, as well as lower raw material and production costs. In particular Reduction in part weight has become an even more important theme due to the recent global SDGs efforts and the energy situation such as soaring fuel prices.
In this column, we will take the automobile industry, which is our main customer, as an example, and introduce the importance and three molding methods that achieve Reduction in part weight.
The importance of weight reduction in the automotive industry
Since reducing the weight of automobiles improves fuel efficiency, conventional efforts have been made to reduce weight, such as by replacing metal parts with resin parts. In recent years, the shift to electric vehicles has progressed, and in order to achieve longer cruising distances, it is necessary to install a large number of batteries. In addition, cameras, monitors, and a large number of sensors are necessary for automatic operation, and the wiring and connector that connect them together are a factor in increasing weight. Further weight reduction of the car body is an important issue.
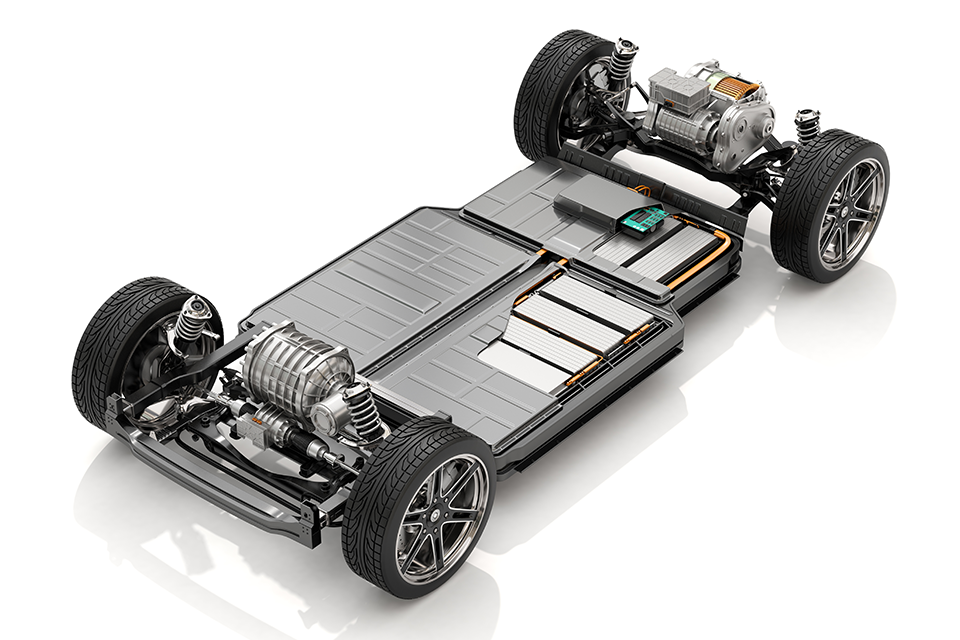
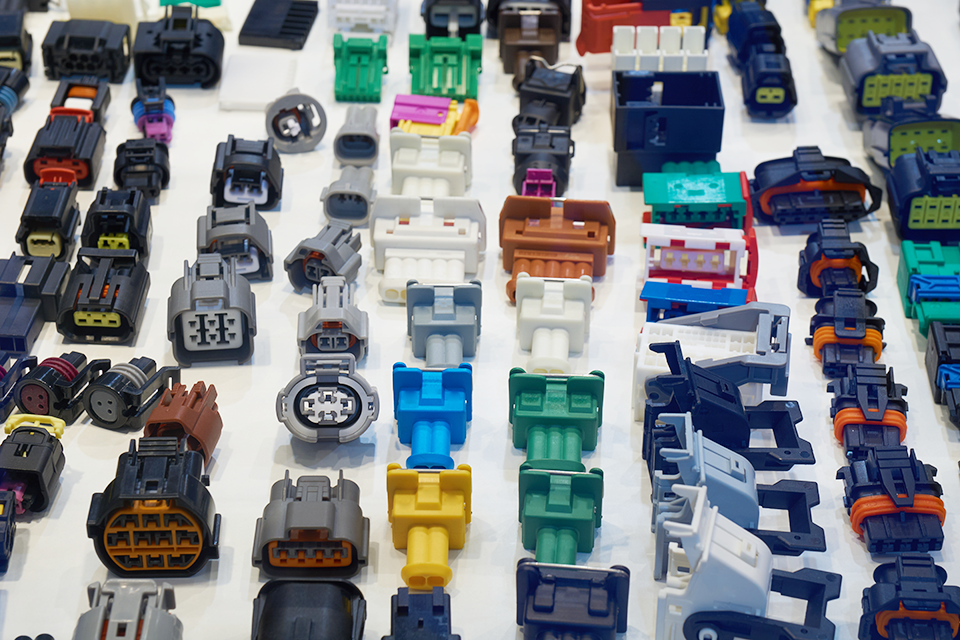
In addition to partial exterior panels, resin molded products for automobiles include engine-related parts, mechanical parts, as well as door linings, dashes, consoles, meter panels, monitors, switches, and more. used in the part of From this, it can be imagined that Reduction in part weight will greatly contribute to the reduction of vehicle weight.
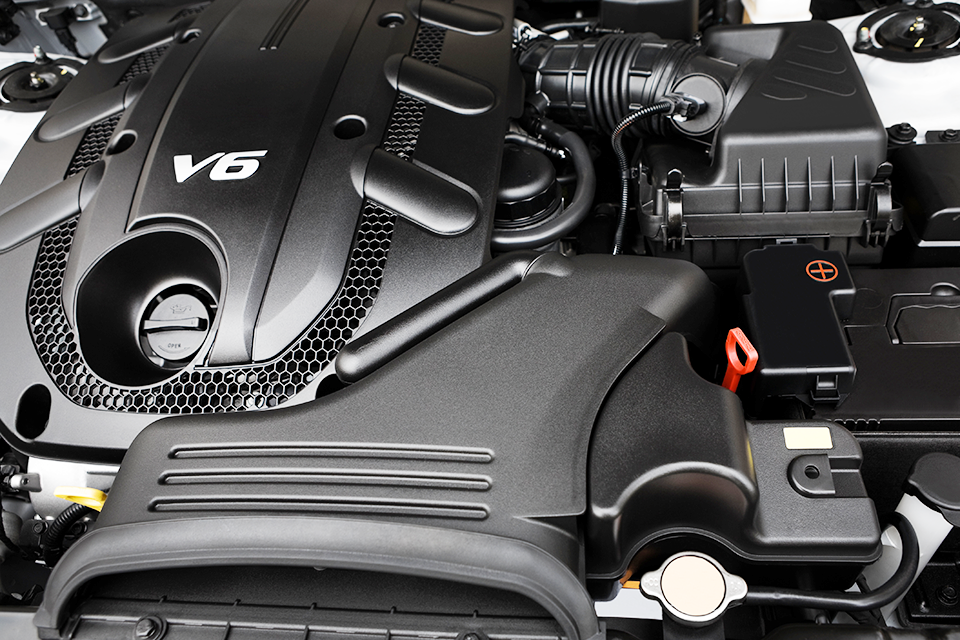
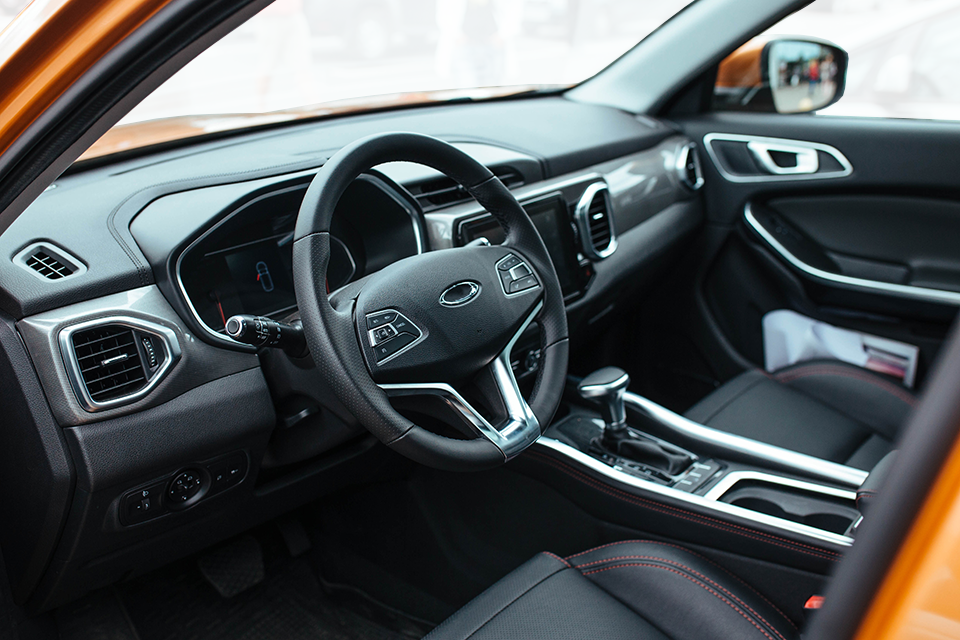
Issues in reduction in part weight
One of the challenges in reducing the weight of molded products is the strength of the molded product. If you reduce the amount of resin used for molding and make the wall thickness thinner, the strength will inevitably decrease. This is not such a problem if it is general merchandise that you use every day, but for safety reasons, it is necessary to ensure the strength and rigidity of the parts used in vehicles such as automobiles and airplanes that are involved in the movement and transportation of people.
In order to solve these seemingly contradictory issues, it is necessary to review new materials, technologies, and structural designs, and various manufacturers are conducting research on a daily basis.
Molding method that realizes reduction in part weight
There are various molding methods to Reduction in part weight, and we will introduce three molding methods that are used for automobiles and aircrafts.
Fiber reinforced plastic molding
The first is fiber reinforced plastic (FRP) molding. The types of materials include carbon fiber reinforced plastic (CFRP), glass fiber reinforced plastic (GFRP) and aramid fiber reinforced plastic (AFRP).
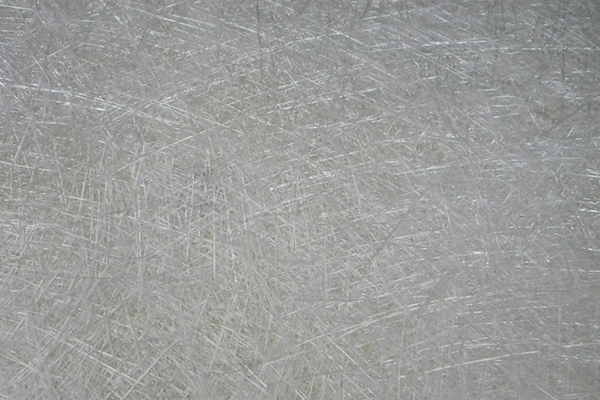
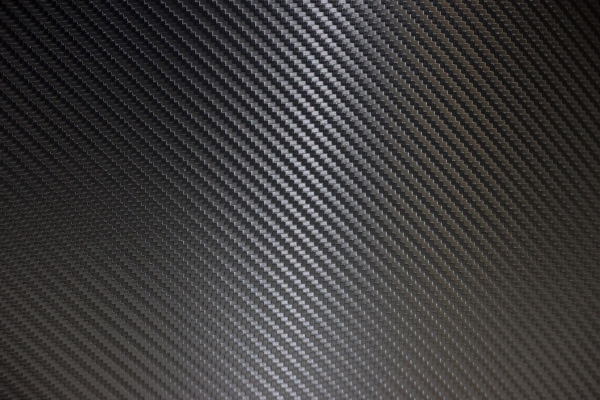
Compression molding is mainly used for large parts used in automobiles and aircraft, and injection molding is used for small precision parts. In both cases, fiber is mixed with the resin raw material and molded to obtain higher strength and rigidity than ordinary plastic, so it can be used as a substitute for metal parts, or because the thickness of itself can be reduced, strength is improved. This is a molding method that enables weight reduction while maintaining the weight.
Foam molding
Foam molding is a molding method that reduction in part weight by creating a cellular structure inside the resin and reducing the amount of resin used. Of course, if a molded product is made by foam molding with the same shape (structure) as that made by normal molding, the strength will decrease due to the reduction in the amount of resin used, but the characteristics of foam molding will be understood. By reviewing the structure of the molded product, it is possible to reduce the weight without reducing the strength while maintaining the same external shape.
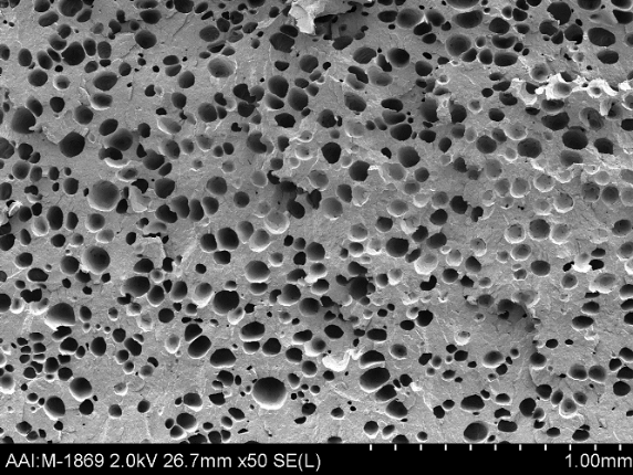
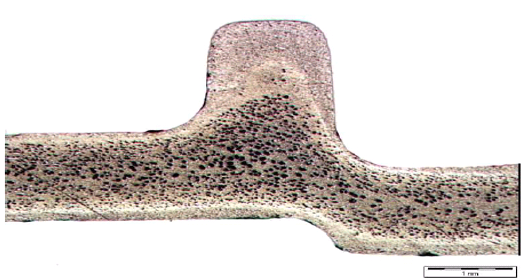
There are two major types of foam molding: chemical foaming and physical foaming.
Chemical foaming
Chemical foaming is a method of foaming by mixing a chemical foaming agent into resin. This has the advantage of reducing the initial introduction cost because there is no need to make major changes to existing equipment. However, some types of foaming agents have disadvantages, including problems with odor after molding, generation of toxic substances by thermal decomposition, and corrosion of molds, as well as difficulty in recycling due to the presence of chemicals in the molded product.
Physical foaming
Physical foaming is a method in which a supercritical fluid (high-pressure gas) is melted in the melted resin material under high pressure, and bubbles are generated by the pressure drop during injection. This requires modifications to the molding machine, generation of supercritical fluid, control equipment, and a mechanism for injection into the cylinder of the molding machine, so the initial introduction cost is a disadvantage compared to chemical foaming. Become. However, since no chemicals are used, there is no need to worry about the problems caused by the chemicals mentioned above, and since the physical properties of the raw material itself do not change, it is easy to recycle. Therefore, from the perspective of SDGs, it seems that many major manufacturers are introducing this physical foam molding.
Matsui has partnered with TREXEL, which provides this physical foaming method, MuCell® Microcellular Foam Molding. In MuCell® Microcellular Foam Molding, nitrogen or carbon dioxide is put into a supercritical fluid state and melted into the resin, and a uniform microcellular structure is formed by the reduction in pressure when it is injected into a mold. By combining this with appropriate product design, it is possible to Reduction in part weight by 5 to 40% without reducing their strength.
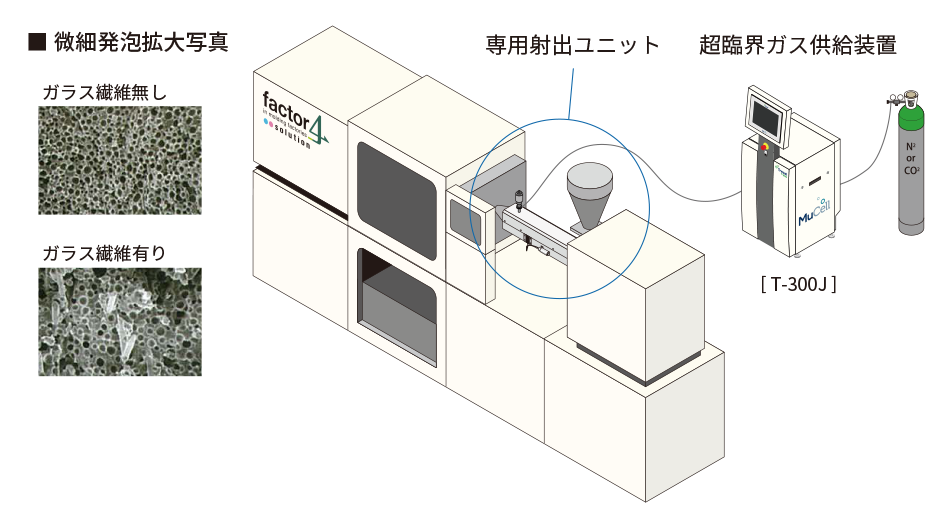
heat & cool molding
Heat & Cool Molding is a technology developed to eliminate weld lines that occur around the openings of molded products, and is a molding method in which the resin is injected while the molding surface of the mold is heated to the temperature range where the resin melts, and then rapidly cooled. Setting the mold temperature high during injection increases the fluidity of the resin, making weld lines less noticeable and improving transferability, and it is not only an innovative molding method that improves the surface quality of molded products, but also suppresses deformation after molding by uniformly rapidly cooling, leading Improve Dimensional Precision.
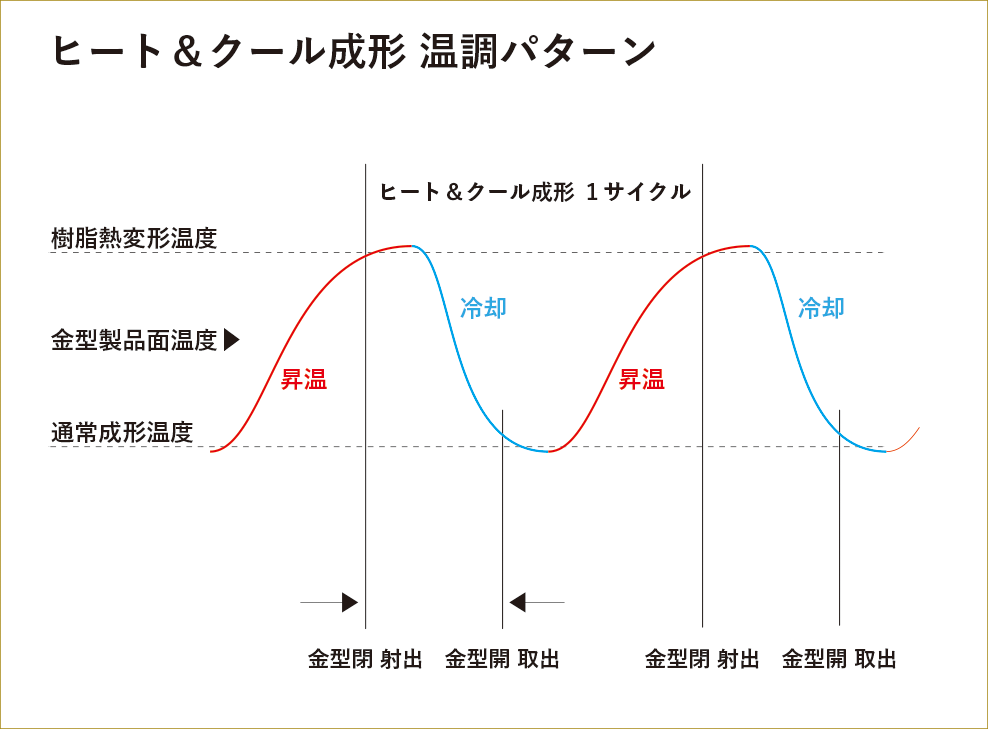
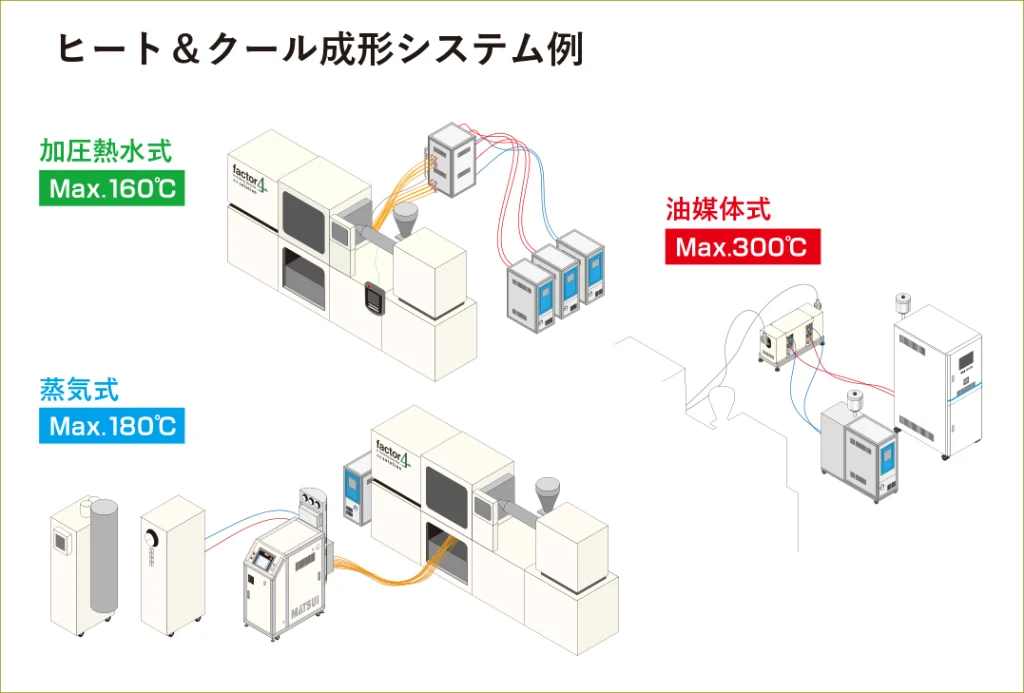
Reduction in part weight by heat & cool molding improves the fluidity of the resin, so it is effective in that it can be set to the minimum necessary thickness (no excess material is used), so this molding method is the only method. effect is not very large. In fact, we can maximize the synergistic effect by combining it with technologies such as "fiber-reinforced plastic molding" and "foam molding" introduced earlier.
With the two molding methods at normal temperatures, fibers, hot water lines, flow marks, swirl marks, etc. appear on the surface of the molded product. I was. However, by combining heat and cool molding, it became possible to obtain a beautiful appearance, and it is now widely used for exterior products that people see, such as home appliances and interior parts of cars.
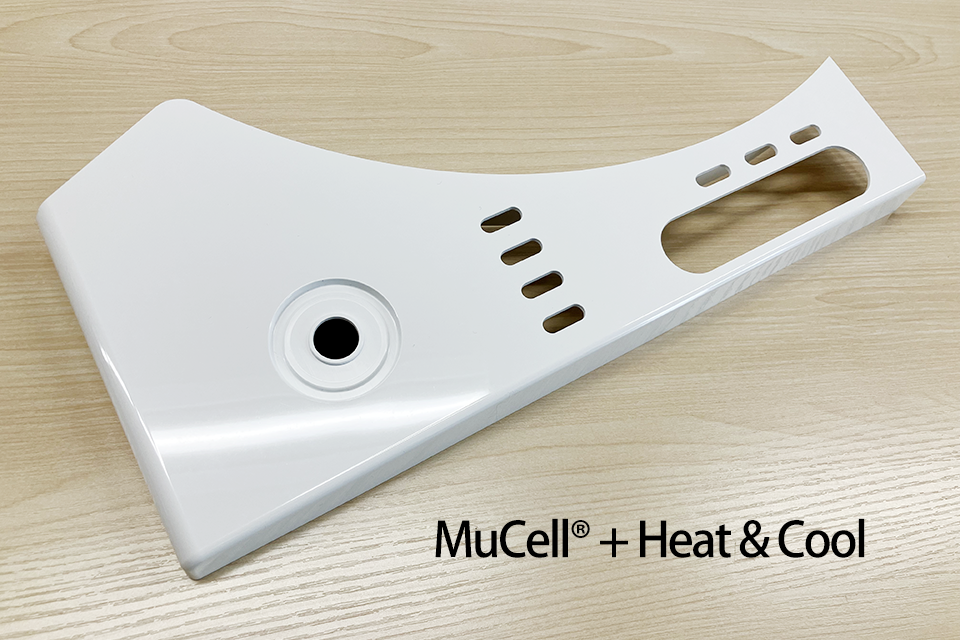
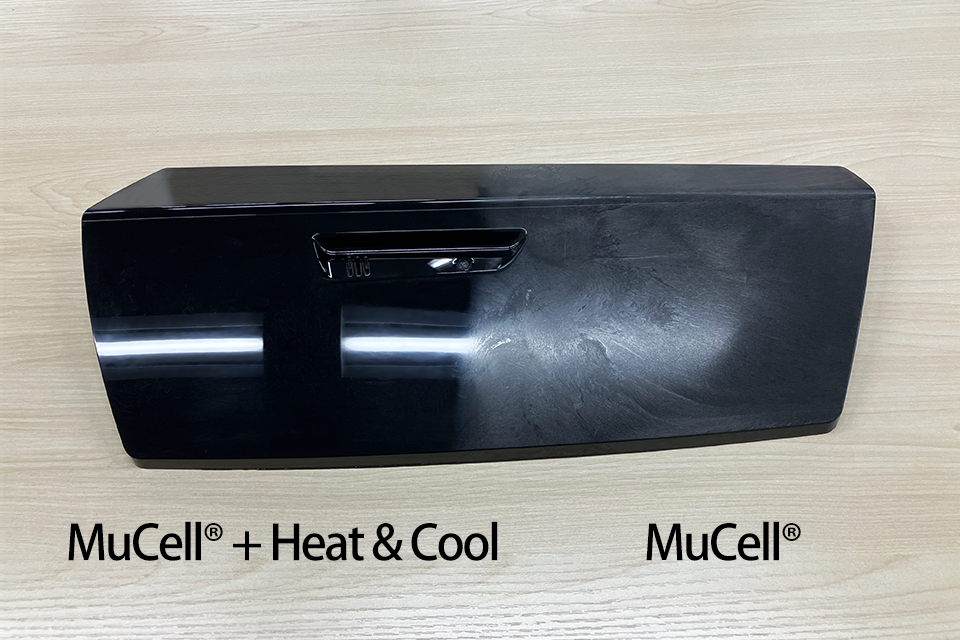
Summary
Reduction in part weight is now a global trend because it leads to reductions in the amount of resin used, production costs, energy consumption, and CO2 emissions. There will be a demand for further weight reduction not only in automobiles and aircraft but also in various other fields.
In addition to the ones introduced this time, there are various technologies and molding methods to reduce the weight of molded products. In order to produce a higher effect, it is necessary to introduce methods and equipment suitable for the production form and molded products.
MATSUI 's mission is to "realize 'factor4' in molding factory", and we propose various solutions to improve the resource productivity of molding factory and improve the added value of molded products and molding factory. Please feel free to contact us.
CX Design Department Yasuhiko Iijima