What is Heat & Cool Molding?
Heat & Cool molding, also known as weld-less molding, is a molding method in which the mold temperature is rapidly heated to the resin softening point during one molding cycle, and then rapidly cooled to a temperature at which the part can be removed, improving mold transferability and achieving surface quality that cannot be achieved with general molding. The surface quality that can be achieved is expected to include improved weld lines, surface gloss, and reduced warping and sink marks.
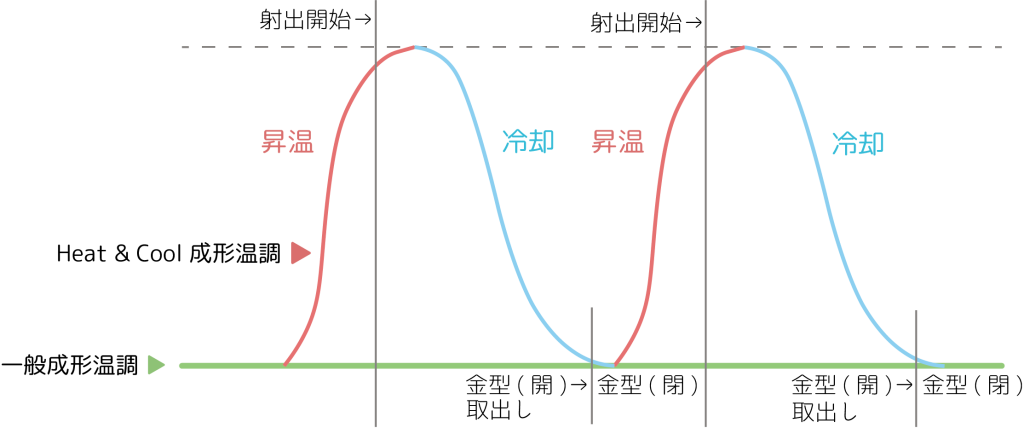
In heat and cool molding, mold temperature is regulated by repeatedly increasing and decreasing the temperature.
[Purpose of each process]
・ Heat: Rapidly heat the mold surface temperature and increase the fluidity of the molten resin inside the mold.
・ Cool: The mold surface temperature is cooled rapidly, maintaining the shape of the molded product.
*Linear scratches that occur when the leading edges of resin flow collide. Weld lines are a defect in appearance products, and are also a defect in functional parts because they cause a lack of strength. Welds occur when a molded product has an opening or is injected through a multi-point gate.
Heat & Cool Solutions
1. Improvement of weld lines
Heating the mold to a high temperature increases the resin fluidity, which in turn improves adhesion between the flow ends of the molten resin compared to regular molding, making it possible to reduce weld lines to a level that is no longer visible to the naked eye *.
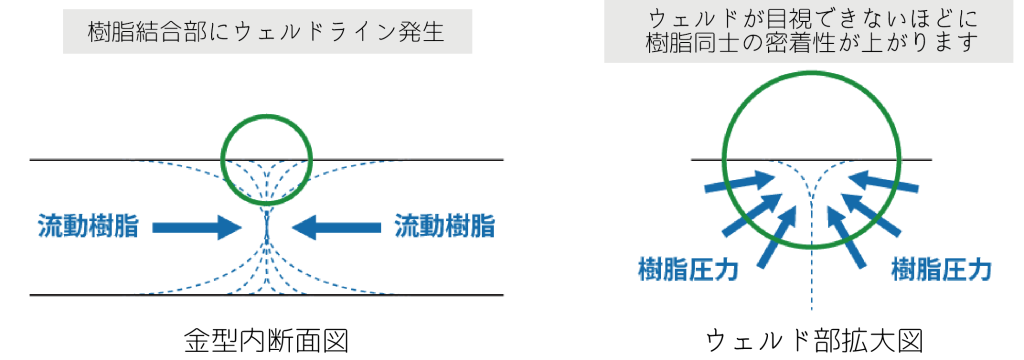
*The physical action of resins colliding with each other remains unchanged. It improves the adhesion of the resin fused area and makes the weld invisible.
2. Improvement of poor transfer
Heating reduces the viscosity of the molten resin in the mold and improves its fluidity, allowing the resin to reach every detail of the mold's molding surface, improving transfer defects. Therefore, it is possible to achieve matte molding with texture transfer and glossy molding with mirror transfer with Heat & Cool molding.
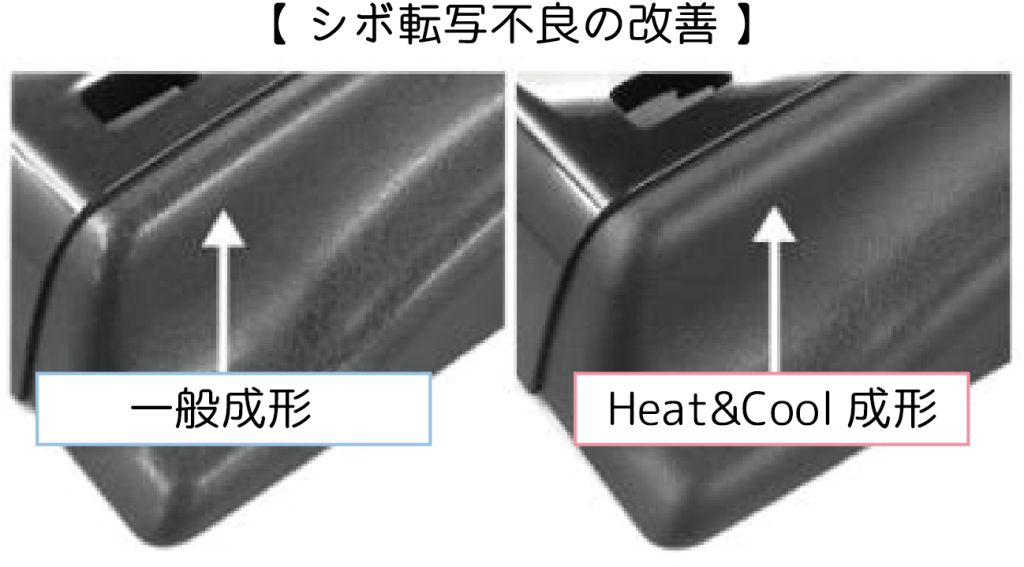
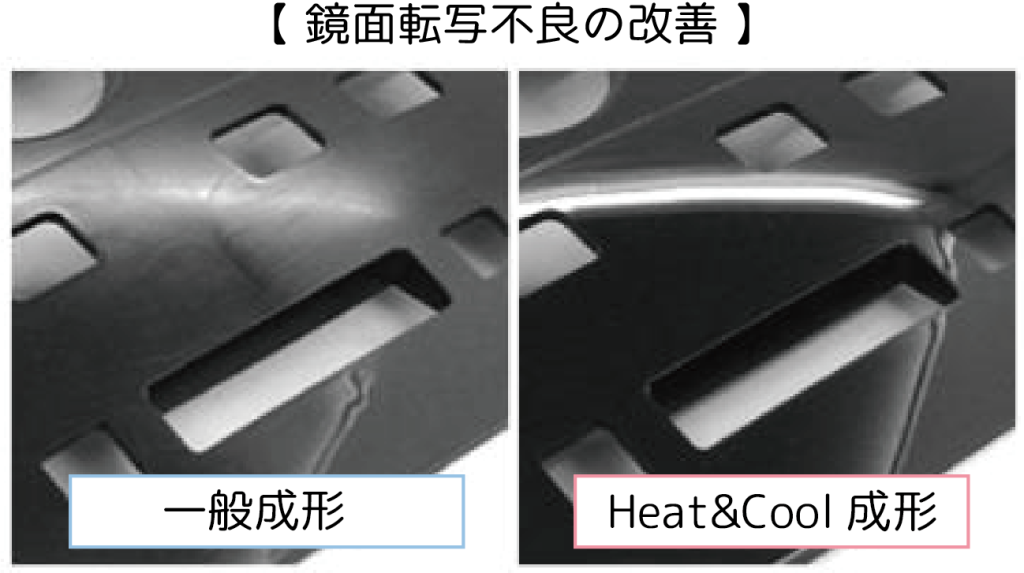
3. Improved filler exposure
Filler exposure refers to additives such as glass fibers that are mixed into resin to give it strength, heat-resistant resistance, and various other resistance properties, being visible on the surface of the molded product. Heat & Cool molding can suppress the exposure of glass fibers and achieve good surface quality.
[Mechanism of expression]
In general molding, the movement of the fountain flow causes the filler to fly outward from the flow front, where it solidifies while pressed against the mold wall, leaving the filler visible on the surface.
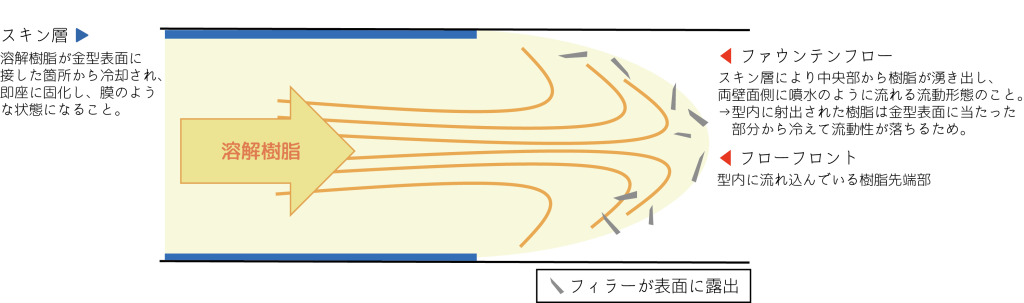
[Improvement mechanism]
Because the temperature of the mold wall is high, the molten resin around the pressed filler is kept warm, and during this time the molten resin covers the filler due to the mold pressure, making it possible to prevent the filler from exposing.
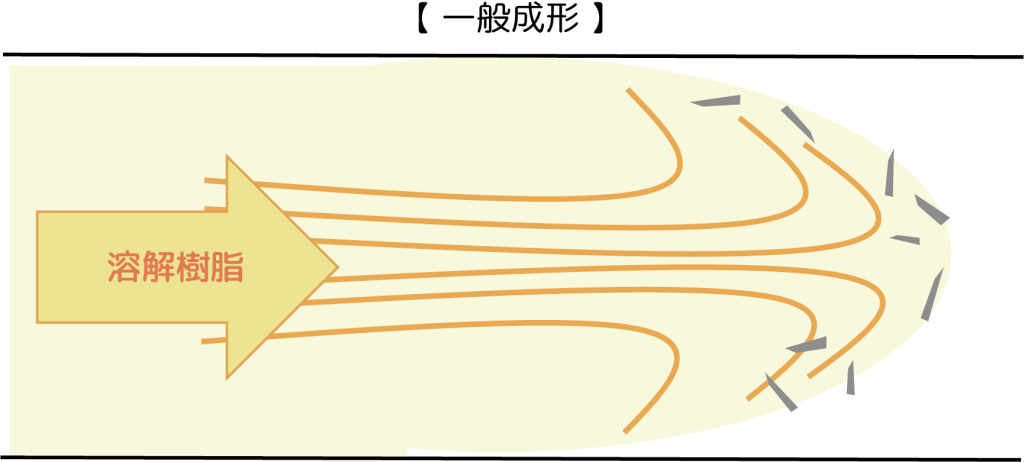
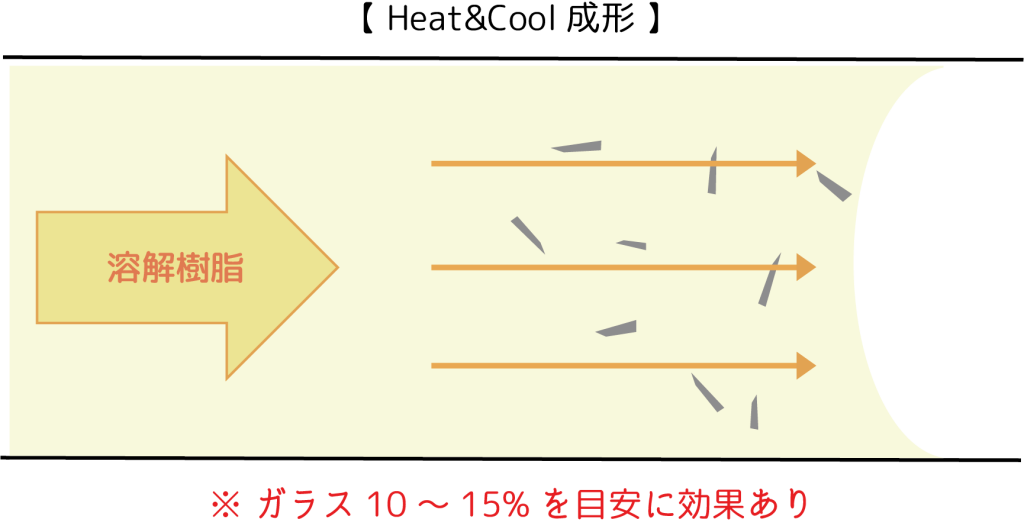
Features of Steam Heat & Cool
Steam-type Heat & Cool molding uses steam, which has high thermal conductivity, for heating, making it possible to heat the mold 2.5 to 6 times faster than hot water. In addition, by using a dedicated mold, the mold surface can be heated and cooled uniformly in a short time.
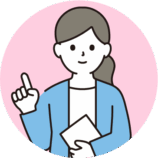
💡ポイント
The boilers are simple and do not require a license. In addition to fuel-fired boilers, electric boilers are also available.
We provide total support from model selection to installation and start-up.
Heat & Cool molding lineup
Matsui offers three types of Heat & Cool molding. If you have any questions about the steam type using RHCM or other molding methods, please feel free to contact us.
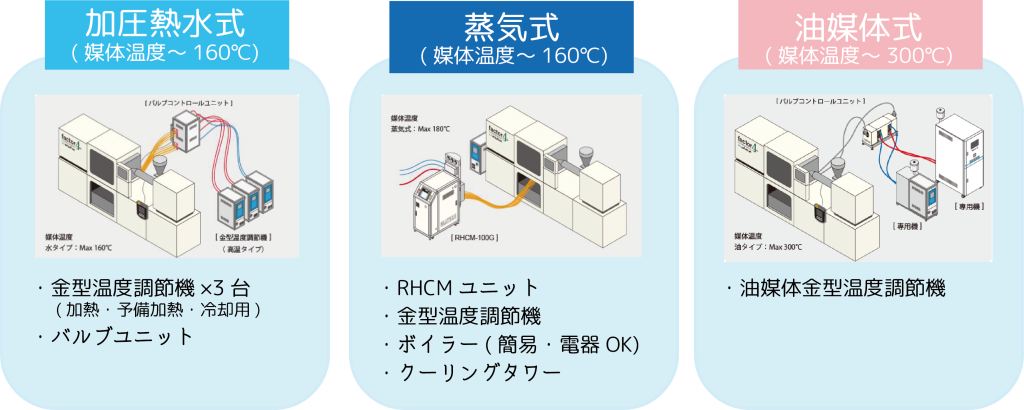