Aiming for factor4 of molding factories
Environmentally friendly plastics factories - The latter part
2022.08.30
Recycling of resin by molding factory
In the first part, we introduced solutions related to the reduction of CO2 emissions under the theme of environmental measures for plastic molding factory. In the second part, we will introduce what kind of approaches can be taken to reduce the waste of "resin," which is indispensable in molding factory.
As you know, the raw material of plastic resin is petroleum. When it comes to SDGs and carbon neutrality, plastic tends to be the bad guy, but plastic has become an indispensable part of our lives. What a plastic molding factory can do is to eliminate waste, recycle what can be recycled, and maximize the use of resources.
We have solutions for that.
Since there are a lot of items, I will put a table of contents...
1. Cut waste by reviewing the composition
- Reducing leftovers in equipment
- Review of color change process
- Optimized material mix
2. Easy-to-work on-site improvements
- bridging prevention
- Prevention of re-absorption
- Reduction of resin usage
3. Increased waste recycling rate
- Reuse of sprues and runners
- Repelletization of expensive engineering plastics
summary
Let's move on.
1. Cut waste by reviewing the composition
Some of you may be wondering, "Where should I start recycling?" In fact, there are many points that should be reviewed from the mixing process of raw materials, which is the very first stage of the molding process.
Reducing leftovers in equipment
In recent years, the trend toward high-mix low-volume production has become stronger, and the frequency of material replacement is increasing. Not only is it time-consuming to change molding materials and colors, but the materials left in the equipment are all discarded so that they do not mix with the next molded product, resulting in a lot of waste.
Gravimetric Blender JCW2-i is equipped with a self-control function that adjusts the amount of material supplied to match the amount of resin used by the molding machine. This has made it possible to reduce the amount of residual material remaining in the machine by up to 99%.
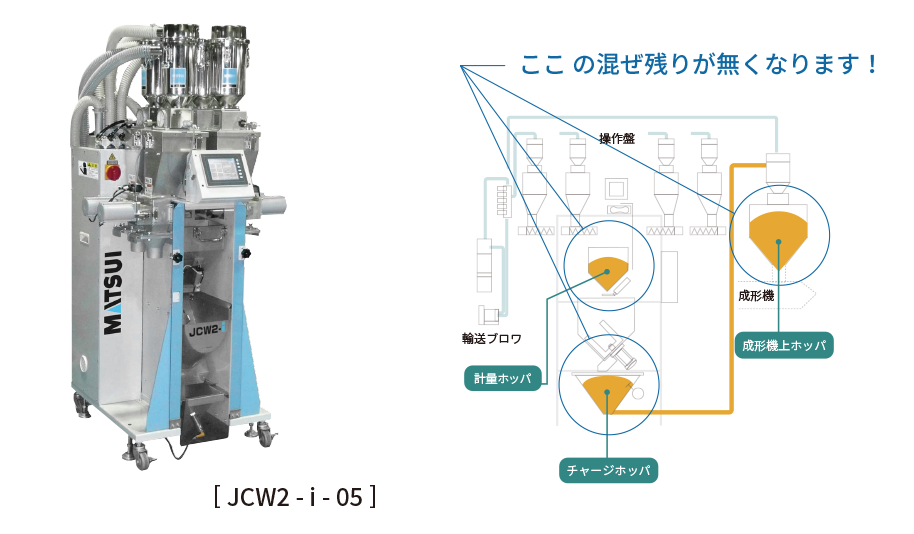
By using it in conjunction with a traceability system, it is possible to visualize the amount of resin used and manage raw materials without waste.
Review of color change process
There are various ways to reduce the waste that occurs when changing colors.
In general, mixing nozzles are required to have uniform material distribution and efficient material change performance. There are already a variety of mixing nozzles on the market, but even if there are nozzles that excel in one or the other, it is difficult to find one that combines both.
If you are dissatisfied with the mixing nozzle you are currently using, you may be able to obtain a greater effect by replacing it with this static mixer.
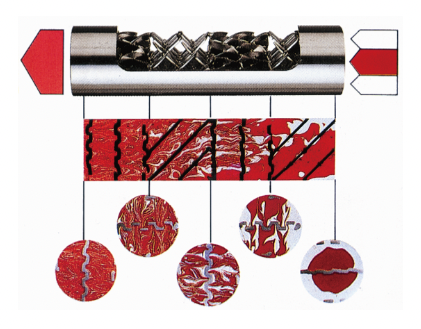
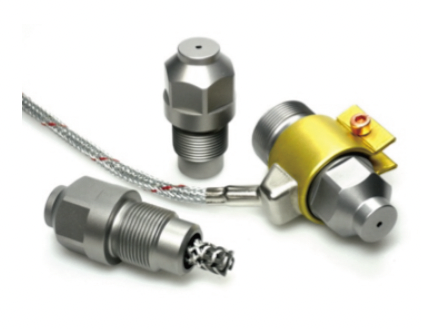
The static mixer has no moving parts, and by combining multiple elements, it efficiently distributes the coloring agent uniformly and suppresses the occurrence of color streaks.
Color change is completed in just 3 to 5 shots due to the retention-less structure, which greatly reduces the waste of resin when changing materials. It has a good reputation for realizing uniformity of material and temperature distribution and smooth material change.
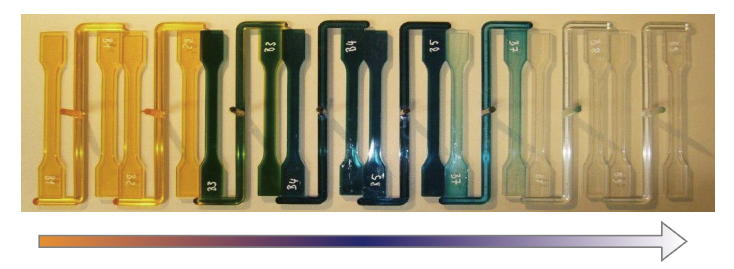
Improved uniformity of temperature distribution also prevents variations in molding quality. In addition, since no power supply is required, the investment can be recovered in a short period of time.
Optimized material mix
I think there are many molding factory that use Master batch for resin coloring. This Master batch is not only expensive, but also has a different size and specific gravity than the pellets, so there is a risk of color unevenness due to the material being unevenly distributed.
The mass-type compounding device JCLW can be installed on the molding machine for weighing and compounding, which not only eliminates the separation of materials during transportation, but also eliminates the need to mix the masterbatch because it feeds the masterbatch one by one at equal intervals. Since the appropriate amount can be blended with precision, the amount of masterbatch that was previously blended in excess due to color unevenness can be minimized.
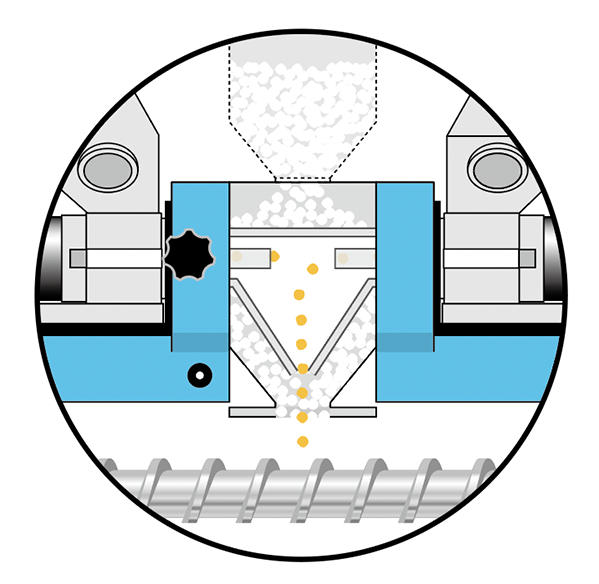
2. Easy-to-work on-site improvements
There are many processes other than compounding that should be paid attention to. Here are some examples of improvements that can be implemented.
bridging prevention
Does bridging occur in Conical section part of the drying hopper and block it when using recycled materials or soft materials? Once clogged, it is necessary to stop the molding machine and purge the residual resin inside the screw. It also interferes with planning.
This anti-bridging device rotates Blade along Conical section part of the drying hopper to keep the resin moving and prevent bridging. It can be retrofitted to Standard products.
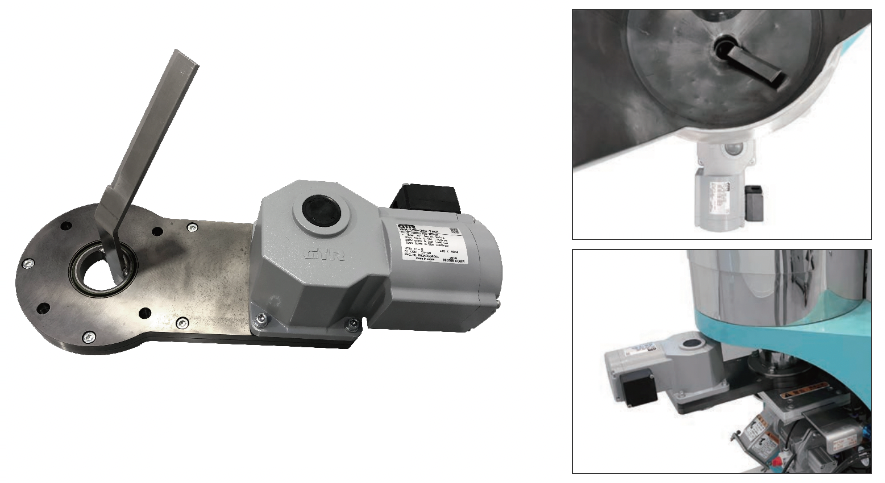
Prevention of re-absorption
The most effective measure to eliminate resin waste is to reduce molding defects. There are various causes of molding defects, but one possible cause is the moisture absorption of the resin remaining in the pipes. By simply attaching a push damper to the bottom of the hopper, you can prevent material from remaining and build a batch transportation system using the existing loader.
Reduction of resin usage
Efforts Eliminate wasted resin include recycling of waste materials, visualization of material usage and proper blending to minimize resin usage, efficient color change to reduce resin waste, blending unevenness and blocking. We have introduced a method to prevent molding defects by preventing this, but there is a molding method called foam molding that reduces the resin itself used for molding.
Our recommended microcellular foam molding technology, MuCell®️, forms a fine cell structure in the resin by diffusing and dissolving gas evenly in the dissolved polymer. By redesigning the molded product based on the premise of using this molding method, it is possible to reduce the weight by about 20% without compromising mechanical strength or dimensional accuracy. In addition, unlike methods that use foaming agents, it only uses gas, so waste materials can be recycled, which also leads to a reduction in the amount of resin used.
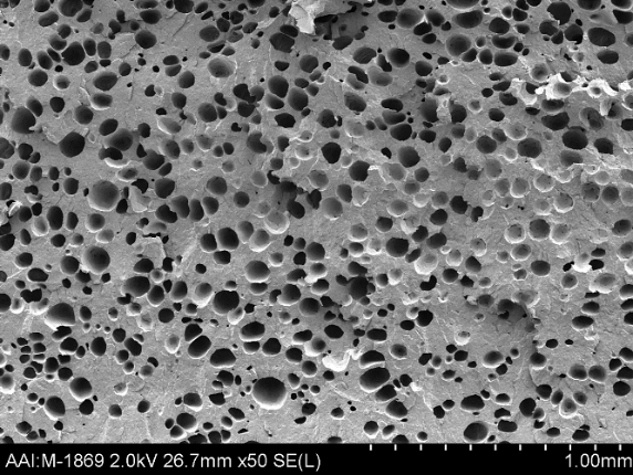
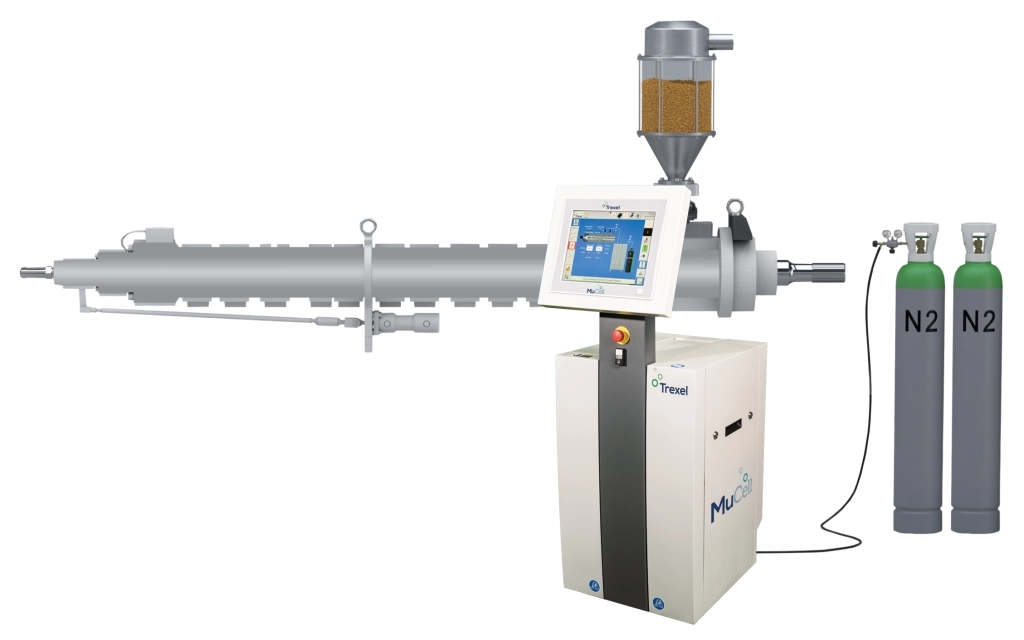
This technology is widely used in the molding of automobile parts, where weight reduction is desired, but with the recent focus on sustainability, it is expected that it will be adopted in more molded products in the future.
3.Increased waste recycling rate
Finally, we must not forget to recycle the waste generated during molding.
Reuse of sprues and runners
When thinking about waste recycling, the first thing that comes to mind is probably the recycling of sprues and runners.
In small precision molded products, the sprue and runner are often larger than the product, and it would be a waste to throw them all away.
With conventional granulators, there was a problem of miscutting and dusting, which led to molding defects when regrind material was used for recycling. The granulators must be cleaned every time changing color of the molded products or type of resin, which is a big burden.
For this reason, many molding factory discard sprues and runners due to concerns about molding defects and the complexity of cleaning, even though they know that it is better to crush and recycle them.
Matsui's Low -speed Granulator SMGL3-G3/G1 and elastomer-specific Granulators MGL2-TPE suppress miscuts and the generation of powder with a newly designed cutter and screenless structure. With SMGL3, the cleaning area can be opened wide and work can be done from the front, so cleaning can be done easily and reliably in a short time while the machine is still set. MGL2 can also fully open the cleaning area without tools. , so you don't have to worry about your work.
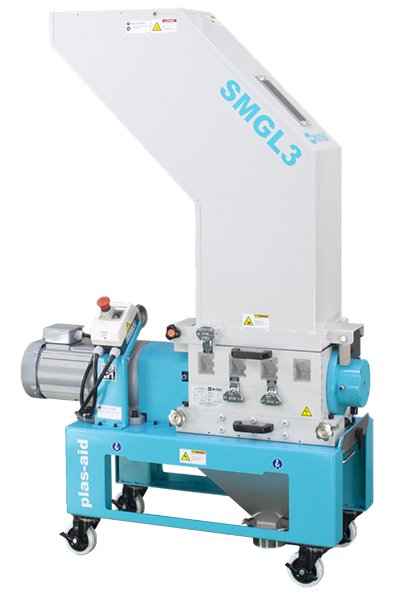
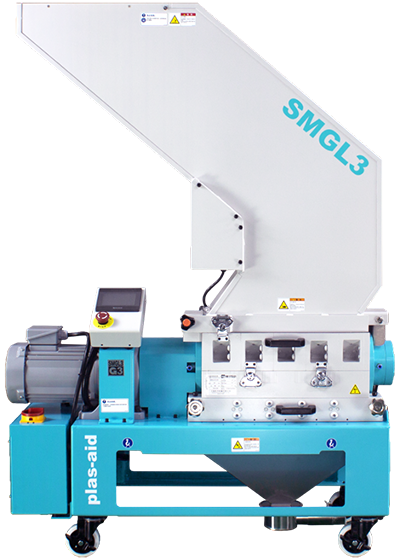
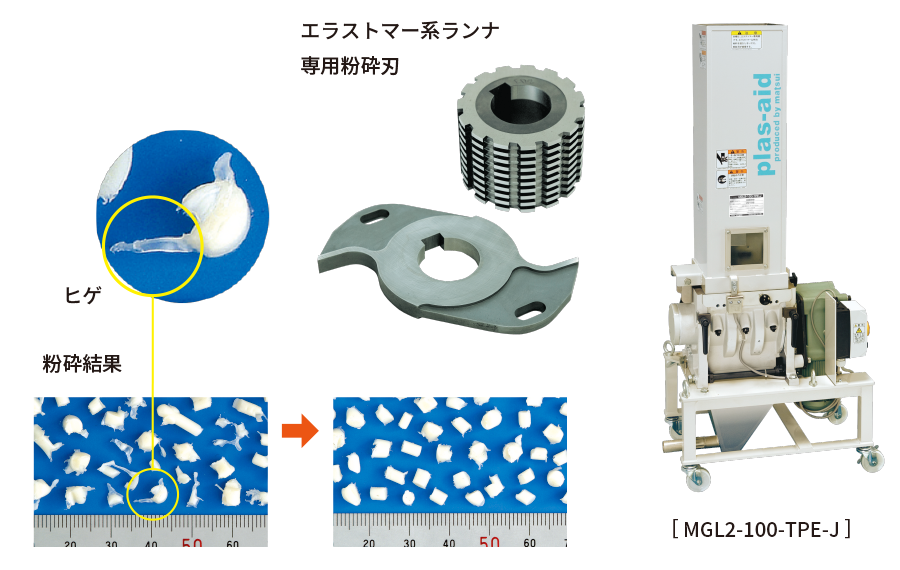
By using these granulators, you can reduce the possibility of molding defects and the trouble of cleaning when changing materials. Why not try recycling sprues and runners?
Repelletization of expensive engineering plastics
The amount of high-performance engineering plastics (engineering plastics) used is increasing year by year. Until now, engineering plastics have been difficult to recycle, and sprues and runners had to be discarded. This is where the pelletizer for engineering plastics comes into play. Equipped with a non-shearing plasticizing screw assembly "SPIRAL LOGIC", it eliminates the occurrence of contamination and black spots due to carbonization, and realizes stable injection. .
A combination of fine mist and air cooling eliminates the need for a water tank and prevents yellowing of the pellets. We have a track record in PA, PC, LCP, etc.
Engineering plastics are expensive materials, so recycling them would lead to significant cost reductions.
Summary
With the SDGs and carbon neutrality, it is expected that the tough situation will continue for the plastics industry. However, new technologies are being developed to meet these trends, and by effectively incorporating them, we can not only solve environmental issues, but also improve corporate value.
Besides introducing large-scale equipment and equipment, there are easy-to-apply solutions to prevent resin waste. Not only is it environmentally friendly, but it also maintains productivity, reduces the burden on workers, and improves the work environment.
At MATSUI, based on the concept of factor4, "Double wealth, half resource consumption", we will actively propose ways to improve the environmental friendliness and resource productivity of molding factory. Please feel free to contact us if you have any problems.
CX Design Department Yasuhiko Iijima