Aiming for factor4 of molding factories
Prevents uneven color in molding! Static control, changing the location of material blending, and blending uniformly.
2023.02.01
"Color unevenness" is a problem that worries everyone who is involved in resin molding. It is one of the appearance defects, but it is difficult to prevent these phenomena by molding conditions, such as differences in color shade between molded products and marble-like patterns in one molded product. It is a troublesome molding defect that makes it difficult to grasp the timing of occurrence.
There are probably many people who say, "In order to reduce production costs, natural materials are mixed with Master batch for coloring, but the color unevenness of the molded products is a problem."
In this column, we will introduce the causes of this color unevenness and specific countermeasures.
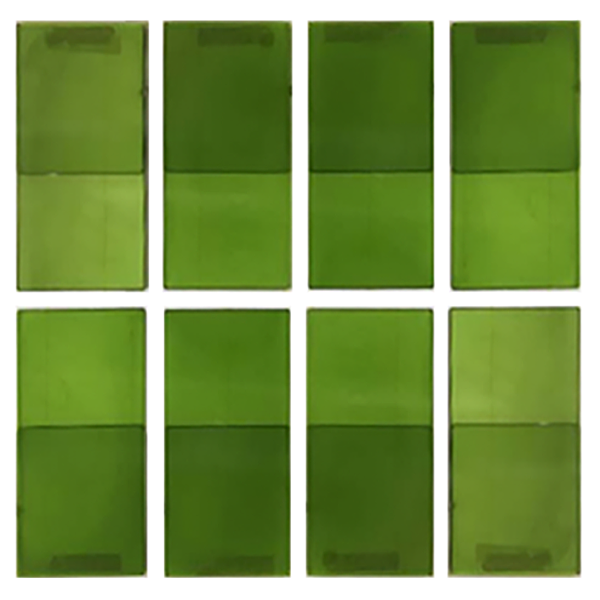
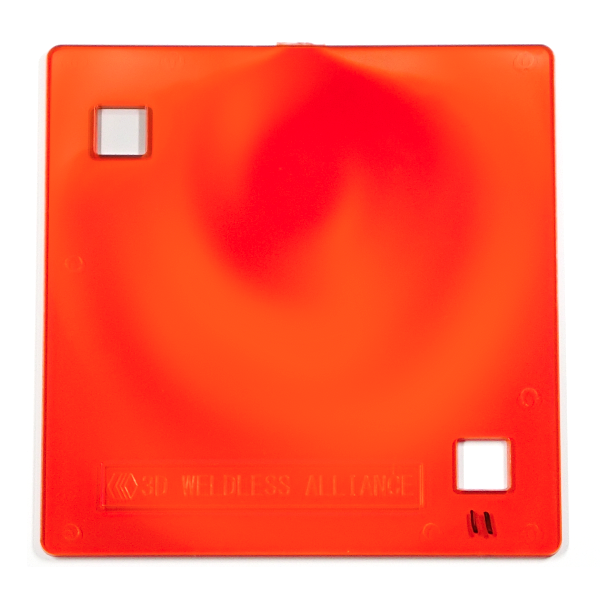
Why does color unevenness occur during molding?
Color unevenness in molded products is caused by changes in the mixing ratio of colorants and natural materials at the time of molding. Therefore, by using colored pellets (color compounds) in which coloring agents are kneaded in advance, this color unevenness is less likely to occur. There is a risk of having to hold an inventory of
Therefore, what kind of countermeasures should be taken to prevent color unevenness from occurring in molded products that are colored by mixing materials?
The first thing you can think of in order to equalize the mixing ratio is to thoroughly mix the Master batch material and natural material in a tumbler (Mixer), but that alone is not sufficient. In fact, there are many cases where the compounding ratio has changed during the material transportation process and at the point of supply to the molding machine. We will explain the causes and countermeasures step by step.
Why would the mix ratio change?
Master batch materials are coloring materials for plastics that are made by kneading high concentrations of dyes and pigments into resin. This is mixed with natural materials to match the color, but since the specific gravity differs between the Master batch material and the natural material, separation and classification occur due to differences in transportation speed and shaking during transportation. It will end up.
In addition, static electricity is generated in the pipes of the transportation route and the hopper on the molding machine, and the Master batch material (or natural material) sticks to the inner walls of those, and when it accumulates to some extent, it will fall off. , there will be light areas and dark areas.
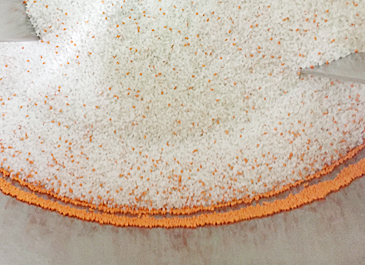
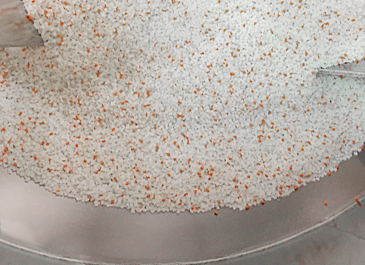
In other words, the mixing ratio changes due to vibration and static electricity during transportation, which causes color unevenness in the molded product. If the mixed material is separated when it is fed to the molding machine, it is difficult to prevent color unevenness due to molding conditions such as back pressure and screw rotation speed. It is important to
Static electricity countermeasures, compounding position change, uniform compounding
As mentioned above, the cause of color unevenness is mainly due to the difference in specific gravity between the Master batch material and the natural material, and the static electricity generated in the transportation route. If so, by changing the compounding position, you will be able to effectively suppress the variation in the compounding ratio.
Countermeasure against static electricity
Static electricity occurs in various places due to environmental humidity, potential difference of materials, friction during transportation, etc., so it is necessary to take countermeasures for each place.
For example, in a resin dryer, by attaching a Screen cone to the Chute inside the drying hopper, it suppresses the generation of static electricity that occurs when transported resin collides with each other and prevents it from adhering to the inner wall of the hopper.
In addition, static electricity is especially likely to occur when materials rub against Conveying hose on transportation routes, so ionizers and KI blow static eliminators are effective. By installing it at the transportation pipe or hose connection part, it prevents the material from sticking to the inside of the pipe or the inner wall of the collector. Because it is small and lightweight, it can be attached to the hopper on the molding machine.
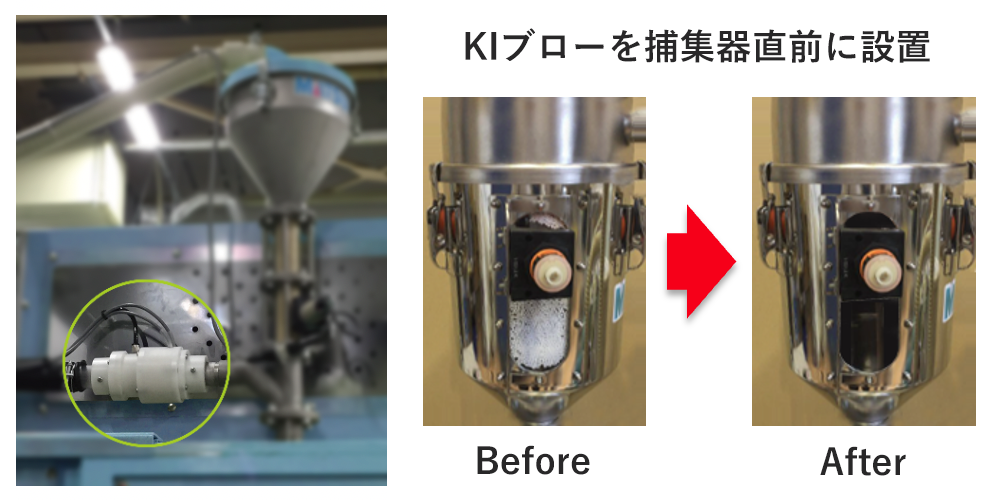
Blending position change, uniform blending
It can be said that it is a very effective measure to review transportation after compounding, which causes separation and classification, and to install Blenders on the molding machine.
With JCLW, a Gravimetric Blender specially designed for installation on the molding machine, the Master batch materials and natural materials are transported by separate routes, and weighted and blended on the molding machine, so the materials are separated and classified during transportation. I don't. In addition, the specially designed dosing system enables a stable supply of the Master batch material directly above the molding machine, allowing it to be mixed uniformly, so there is no unevenness in the mixing ratio regardless of where it is cut.
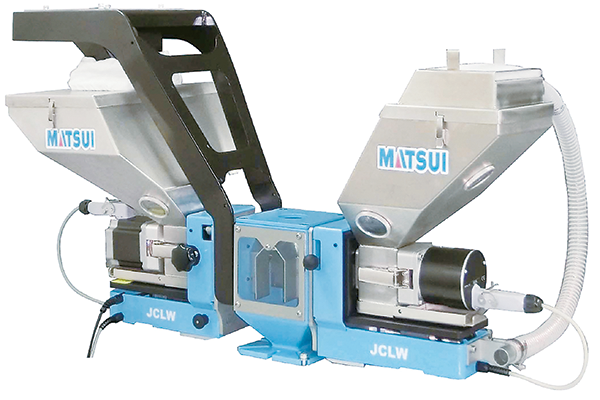
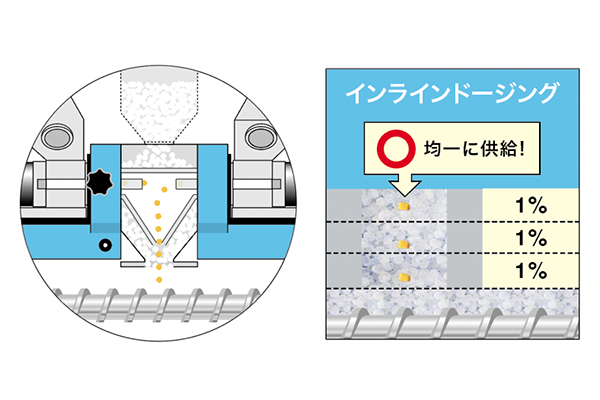
Click here for details ⇒Mass Gravimetric Blender (Calculation Type) JCLW
There is also a method of using a liquid color Blenders instead of a Master batch material for transparent light-colored molding where color unevenness tends to be noticeable.
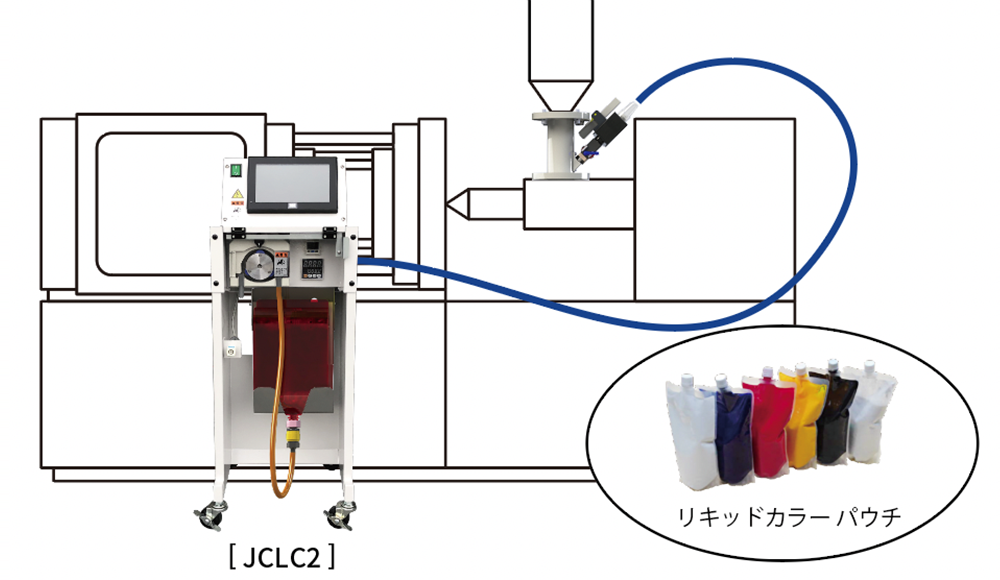
Just before the natural material enters the molding machine, by supplying the liquid color that is easy to mix evenly, it realizes uniform blending with the transparent resin and prevents color unevenness in the transparent light-colored molded product.
Summary
Color unevenness in molded products is difficult to visually inspect, and because it occurs randomly, it is difficult to manage lots. Since it is difficult to prevent it under molding conditions, it is effective to take measures such as optimization of transportation, formulation, and countermeasures against static electricity. Anti-static measures also prevent contamination and contribute to stable molding quality.
MATSUI proposes various solutions to improve the productivity of molding factory. Please feel free to contact us.
CX Design Department Yasuhiko Iijima